Understanding MIL-PRF-31032, Part 6
December 8, 2020 | Anaya Vardya, American Standard CircuitsEstimated reading time: 4 minutes
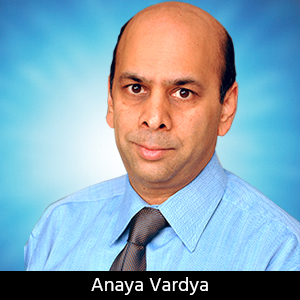
Concluding this six-part discussion on understanding the military PCB performance standard MIL-PRF-31032, I will address the remaining procedure required to address the unique requirements of the military.
PCI and CVI Inspection
The purpose of this document is to define periodic conformance inspection (PCI) and capability verification inspection (CVI) applicable to the qualified specification sheets, to be used for the purposes of quality monitoring and change control evaluation. These are both requirements that are performed by a DLA approved third-party lab. PCI is typically done monthly and CVI every two years.
PCI
PCI testing is performed on the most complex DoD lot built during the month and tested in accordance with the applicable specification sheet (slash sheet). The data and results of the PCI, including failure analysis, need to be available and submitted to the qualification activity monthly. Any PCI failure will require submitting a corrective action to DLA and also shall require notification to the affected customer within three working days (typically) of the discovery of the failure.
Conformance Inspection Vehicle
The PCI vehicle is generally incorporated into the panel as a dedicated test coupon but can also be a PCB, separate test vehicle, or any combination. Documentation and traceability procedures for conformance inspection shall be the same as for normal production and shall include the design, design rules, test procedures, and process rules. These requirements are normally contained in the production traveler package. The complexity shall reflect, as a minimum, the functionality of the process and technology characteristics, and the design of the vehicle shall reflect the worst-case conditions.
Selection and Submission of Samples for PCI
On a monthly basis, the most complex DoD performance specification lot shall be selected to perform PCI and must include each base material qualified and produced during the month. Preparation of the PCI package is generally done the first week of the month following the month being tested. Complexity must be in accordance with the qualified technology, including attributes such as microvias, layer count, line width, hole size and aspect ratio, etc. One way to determine which military lot was the most complex of the month is to review the microsection log. The location of the test coupons on the panel needs to be identified and documented.
Note: If the design has “foil construction,” surface peel strength samples need to be also submitted for testing. The deliverables to the testing lab include:
- Laboratory test request form
- Samples required for testing
- Master drawing
- Copy of purchase order
- Maintain a copy of all documents submitted to an outside laboratory
Required PCI Tests and Inspections
These include the following:
- Tensile strength
- elongation
- Copper purity
- Rework simulation
- Moisture and insulation resistance
- Surface peel strength (foil lamination lots)
Note: Tensile strength and elongation testing are required (monthly) regardless of whether DoD specification production occurred during the month.
Capability Verification Inspection
Thermal shock testing (typically every two years) is required for each base material type qualified. After thermal shock, the printed board test specimens need to meet the following requirements:
- Visual inspection: When inspected, there shall be no evidence of plating cracks, blistering, crazing, or delamination in excess of that allowed.
- The change in resistance between the first high-temperature cycle and the last high-temperature cycle shall not be more than 10%.
- Destructive physical analysis (DPA) by cross-sectioning: The PCB test specimen shall be vertically cross-sectioned and inspected; requirements specified shall be met.
- “Solder reflow thermal stress” and “direct current-induced thermal cycling” may be considered by the TRB team for CVI but is not required.
As with PCI, any failure will require submitting a corrective action to DLA and also shall require notification to the affected customer within three working days (typically) of the discovery of the failure. CVI reporting shall be approved by the TRB team and submitted to the qualifying activity in order to maintain current DoD qualifications.
The CVI report will outline the supporting data that is being used to support that the capabilities listed for each base material qualification have been met. Supporting data includes In-process, LCI, PCI, and thermal shock test reports. Other production supporting documentation may include the master drawings, lay-up sheets, travelers, etc. Reports are typically required to be submitted within 60 days from the end of the reporting period.
Slash Sheets
Specification or slash sheets can be a bit confusing, but they are basically just performance specs that cover the requirements for PCBs based on their technology as outlined here:
- MIL–PRF–31032/1: Printed Wiring Board, Rigid, Multilayered, Thermosetting Resin Base Material, With or Without Blind and Buried Plated Through-Holes, for Soldered Part Mounting.
- MIL–PRF–31032/2: Printed Wiring Board, Rigid, Single and Double Layer, Thermosetting Resin Base Material, With or Without Plated Through-Holes, for Soldered Part Mounting.
- MIL–PRF–31032/3: Printed Wiring Board, Flexible, Single and Double Layer, With or Without Plated Through-Holes, With or Without Stiffeners, for Soldered Part Mounting.
- MIL–PRF–31032/4: Printed Wiring Board, Rigid-Flex or Flexible, Multilayer, With Plated Holes, With or Without Stiffeners, for Soldered Part Mounting.
- MIL–PRF–31032/5: Printed Wiring Board, Rigid, Multilayered, Thermoplastic or Thermoplastic and Thermosetting Resin Base Material, With Plated Through-Holes, for High-Frequency Applications.
- MIL–PRF–31032/6: Printed Wiring Board, Rigid, Single and Double Sided, Thermoplastic Resin Base Material, With or Without Plated Through-Holes, for High-Frequency Applications.
Conclusion
This concludes this 6-part series on understanding MIL-PRF-31032. I hope the information presented here has been educational and helpful for anyone looking to manufacture for the mil-aero market.
Editor’s note: Read Part 1, Part 2, Part 3, Part 4, and Part 5.
Anaya Vardya is president and CEO of American Standard Circuits; co-author of The Printed Circuit Designer’s Guide to… Fundamentals of RF/Microwave PCBs and Flex and Rigid-Flex Fundamentals; and author of Thermal Management: A Fabricator's Perspective. Visit I-007eBooks.com to download these and other free, educational titles. He also co-authored “Fundamentals of PCB Technology.”
Suggested Items
BEST Inc. Introduces StikNPeel Rework Stencil for Fast, Simple and Reliable Solder Paste Printing
06/02/2025 | BEST Inc.BEST Inc., a leader in electronic component rework services, training, and products is pleased to introduce StikNPeel™ rework stencils. This innovative product is designed for printing solder paste for placement of gull wing devices such as quad flat packs (QFPs) or bottom terminated components.
See TopLine’s Next Gen Braided Solder Column Technology at SPACE TECH EXPO 2025
05/28/2025 | TopLineAerospace and Defense applications in demanding environments have a solution now in TopLine’s Braided Solder Columns, which can withstand the rigors of deep space cold and cryogenic environments.
INEMI Interim Report: Interconnection Modeling and Simulation Results for Low-Temp Materials in First-Level Interconnect
05/30/2025 | iNEMIOne of the greatest challenges of integrating different types of silicon, memory, and other extended processing units (XPUs) in a single package is in attaching these various types of chips in a reliable way.
E-tronix Announces Upcoming Webinar with ELMOTEC: Optimizing Soldering Quality and Efficiency with Robotic Automation
05/30/2025 | E-tronixE-tronix, a Stromberg Company, is excited to host an informative webinar presented by Raphael Luchs, CEO of ELMOTEC, titled "Optimize Soldering Quality and Efficiency with Robotic Automation," taking place on Wednesday, June 4, 2025 at 12:00 PM CDT.
CE3S Launches EcoClaim Solutions to Simplify Recycling and Promote Sustainable Manufacturing
05/29/2025 | CE3SCumberland Electronics Strategic Supply Solutions (CE3S), your strategic sourcing, professional solutions and distribution partner, is proud to announce the official launch of EcoClaim™ Solutions, a comprehensive recycling program designed to make responsible disposal of materials easier, more efficient, and more accessible for manufacturers.