Estimated reading time: 4 minutes
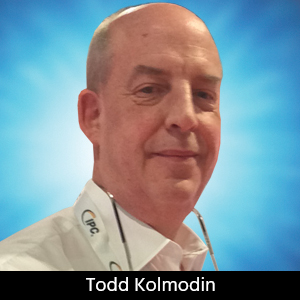
Testing Todd: Training the Force or the Few
As with any business, the quality of goods and/or services is of the utmost importance. Company reputations are gauged by the success or failure of maintaining high-quality outputs. Maintaining high-quality and on-time delivery depends on multiple factors: first, equipment and tools to produce the product or service, and second, the power of the workforce behind the product.
Machines and tools support the manufacturing of products, but they are built with the assistance of other machines and, most importantly, people—the human component. Machines do what they are told, and those instructions come from humans. Manual tasks are performed by humans to the point they may be deemed too repetitive, and the task is then given to robots. However, these robots are given instructions by humans. Companies that maintain superior on-time delivery and quality rely on a key factor within their organization: competence and training of their core workforce.
In the ISO9001:2015 standard, companies are required to demonstrate a system of competence measurement within the organization. This shall be demonstrated with documented information. However, how a company embraces this requirement is totally up to them. Tasks are usually documented by work instructions, which define how any given task is to be performed. Ideally, a stranger can walk up to a task, read the work instruction, and perform the task under supervision. In time, the new operator becomes more proficient in that task and no longer requires supervision. The training matrix should define when that time is, when the operator should be reviewed again, and at which point proficiency should be re-scored. A strong training matrix will encompass these disciplines.
Operator Task-Specific Training vs. Cross-Training
There are different camps when it comes down to task-specific training vs. cross-training. It really comes down to the size of the operation and management philosophies. In a ginormous operation, it may be prudent to train specific employees for specific tasks. If the depth of the workforce supports this, it may be the optimal solution.
If the department has but one function and many employees, it makes sense. New employees may start as a trainee and progress to a general operator, and this may work perfectly. Some general operators may elevate to a lead or supervisor. However, they still remain within the same department and perform the same tasks. Other departments within the facility will have the same matrix. If an employee calls in sick or quits, the depth of the workforce can handle the disruption, and although they may be one person shy, the void is filled by a new trainee.
What about the small “mom and pop” type operations? The depth of the workforce is hardly the magnitude of the ginormous example. This can also be the same in a large parent company with small divisional offices. Each of these operations may have small workforces that are required to perform multiple tasks. Is the single task training matrix feasible in this case? Perhaps. However, with these smaller operations, the loss of an employee, even for a day, can be stressful and cause disruption to delivery and perhaps quality.
This is where cross-training becomes an advantage. Employees are trained on multiple tasks; some, they do every day, while others may be performed on an as-needed basis. Even though the employee count is smaller, the depth of knowledge in the small workforce is strong. This allows the smaller operations to roll with the occasional employee illness, vacation, or other unforeseen circumstances.
How a training matrix is developed is solely up to the organization. However, it should provide the instructions for any given tasks to be performed, a way to gauge competency, and a time frame to review the competencies. Levels of competency are recommended so that an employee may perform a task without having mastered the task. Examples would be work with supervision, work unsupervised, and work unsupervised and train others. These could be outlined by proficiency percentages or levels, such as Trainee, Operator I, Operator II, and so on. Perhaps equipment may need attention, or other technical aspects are necessary. This may require higher levels of expertise. The matrix can encompass this as well.
Strong training systems may incorporate synergies between the training system and actual equipment or tasks. An example would be an operator who is disallowed the operation of a machine when they sign on because the machine consults the training matrix to validate the employee competence. The system has a self-check mechanism to guarantee employee competence is achieved and maintained.
Simply put, you cannot perform tasks for which you are not trained. This satisfies the competence and training requirement and also keeps a thumb on the pulse of the system. This type of system also maintains traceability in case there is a problem found. The training system can be consulted along with machine records to find out who, what, when, where, and finally, why.
Happy holidays! Be safe.
This column originally appeared in the December 2020 issue of PCB007 Magazine.
More Columns from Testing Todd
Testing Todd: Why 4-wire Kelvin?Testing Todd: Why TDR?
Testing Todd: Positivity Boosts Employee Morale
Testing Todd: Preparing Employees for the Long Haul
Testing Todd: Where Can We Improve?
Testing Todd: Turning Into the Wind
Testing Todd: Coming Back to Life—Design Recovery
Testing Todd: Decision Time—Invest or Delegate?