-
- News
- Books
Featured Books
- smt007 Magazine
Latest Issues
Current IssueWhat's Your Sweet Spot?
Are you in a niche that’s growing or shrinking? Is it time to reassess and refocus? We spotlight companies thriving by redefining or reinforcing their niche. What are their insights?
Moving Forward With Confidence
In this issue, we focus on sales and quoting, workforce training, new IPC leadership in the U.S. and Canada, the effects of tariffs, CFX standards, and much more—all designed to provide perspective as you move through the cloud bank of today's shifting economic market.
Intelligent Test and Inspection
Are you ready to explore the cutting-edge advancements shaping the electronics manufacturing industry? The May 2025 issue of SMT007 Magazine is packed with insights, innovations, and expert perspectives that you won’t want to miss.
- Articles
- Columns
- Links
- Media kit
||| MENU - smt007 Magazine
This Month in SMT007 Magazine—Continuous Improvement: As Simple as X = Xc – 1
January 4, 2021 | I-Connect007 Editorial TeamEstimated reading time: 2 minutes
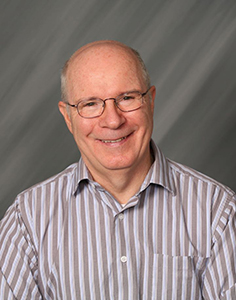
X=Xc– 1 is a conceptual equation for continuous improvement. You define X and work to reduce it by a factor of 1. This could be one work hour, one process step, one day less in a cycle, and so on. We recently met with Ronald Lasky, Ph.D., PE, Sr. Technologist, Indium Corp. and Professor of Engineering at Dartmouth College, to discuss the concept of X=Xc – 1 and get his advice on generating enthusiasm among readers and the next generation about continuous improvement. As this discussion illustrates, many process improvements are small in scale, not yearlong, major efforts.
Nolan Johnson: Continuous improvement is not a new idea, but we would like to shine a light on the idea of “X=Xc – 1.” To do this, first, you define what X is, and then you make an action plan to reduce it by one. It could be reducing your design spins, the number of steps in your process, or the number of gates in manufacturing. It could be any approach where you can incrementally improve, take something out, and get it done with fewer steps and iterations.
Happy Holden: It’s the concept of solid base hits rather than going for the home run all the time.
Ron Lasky: It’s sort of a formulaic approach, but maybe that’s better. Continuous improvement is the essence of Lean Six Sigma. There is a term in Lean Six Sigma called DMAIC (define, measure, analyze, improve, and control), assuming you want to improve something. You define what it is that you want to improve (D). You measure where you are (M). You collect some data and analyze it (A). Then, you improve it (I), usually with a designed experiment. Once that’s all set up, you must develop a plan to control it (C). That’s statistical process control.
For example, let’s say a small mom-and-pop shop collected the data for the year 2020, and they found that at the end of the line before repair, they had 2% fallout: 2% of the boards had to be repaired. They collected the data in a Pareto chart. If they made 100,000 boards, they had about 2,000 boards that were defective, and they found that the primary defect was shorts. That was 1,200, and then the second defect was a missing component and on down the list. Usually, you would want to attack the most significant defect mode. That was shorts. They started to look at what typically causes shorts. Two-thirds of end-of-line defects can be attributed to stencil printing, so that is good place to start.
This mom-and-pop shop may hire a local college student as an intern, who has a Lean Six Sigma Green Belt, and they teach the intern about electronic assembly. The company may also have pictures of all 2,000 defects. They analyze those images and decide that the main reason they had too many shorts is that there’s too much solder paste on the pads. When the component is placed, excess solder paste spills over the pad that occasionally, when it melts, creates a solder bridge to an adjacent pad. They do some more work and decide that maybe they should make all of their stencil apertures a little tighter, or maybe they should get a different solder paste. They call their current solder paste vendor and discuss some of these issues.
To read this entire interview, which appeared in the January 2021 issue of SMT007 Magazine, click here.
Suggested Items
Driving Innovation: Direct Imaging vs. Conventional Exposure
07/01/2025 | Simon Khesin -- Column: Driving InnovationMy first camera used Kodak film. I even experimented with developing photos in the bathroom, though I usually dropped the film off at a Kodak center and received the prints two weeks later, only to discover that some images were out of focus or poorly framed. Today, every smartphone contains a high-quality camera capable of producing stunning images instantly.
Hands-On Demos Now Available for Apollo Seiko’s EF and AF Selective Soldering Lines
06/30/2025 | Apollo SeikoApollo Seiko, a leading innovator in soldering technology, is excited to spotlight its expanded lineup of EF and AF Series Selective Soldering Systems, now available for live demonstrations in its newly dedicated demo room.
Indium Corporation Expert to Present on Automotive and Industrial Solder Bonding Solutions at Global Electronics Association Workshop
06/26/2025 | IndiumIndium Corporation Principal Engineer, Advanced Materials, Andy Mackie, Ph.D., MSc, will deliver a technical presentation on innovative solder bonding solutions for automotive and industrial applications at the Global Electronics A
Fresh PCB Concepts: Assembly Challenges with Micro Components and Standard Solder Mask Practices
06/26/2025 | Team NCAB -- Column: Fresh PCB ConceptsMicro components have redefined what is possible in PCB design. With package sizes like 01005 and 0201 becoming more common in high-density layouts, designers are now expected to pack more performance into smaller spaces than ever before. While these advancements support miniaturization and functionality, they introduce new assembly challenges, particularly with traditional solder mask and legend application processes.
Knocking Down the Bone Pile: Tin Whisker Mitigation in Aerospace Applications, Part 3
06/25/2025 | Nash Bell -- Column: Knocking Down the Bone PileTin whiskers are slender, hair-like metallic growths that can develop on the surface of tin-plated electronic components. Typically measuring a few micrometers in diameter and growing several millimeters in length, they form through an electrochemical process influenced by environmental factors such as temperature variations, mechanical or compressive stress, and the aging of solder alloys.