Estimated reading time: 4 minutes
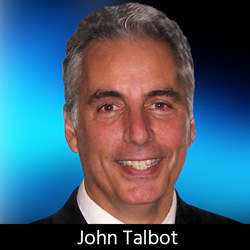
Consider This: Heavy-Copper Flex Circuits See Large Growth
Flex circuits can be designed and manufactured to handle heavy currents. Thicker copper—3 oz. to 20 oz.—prevents true high cycle flexing. However, the circuit can be used in “bend to fit” and limited bend applications in high-current situations. Heavy copper—as thick as 20 oz.—has been manufactured in single-sided and double-sided applications. Multi-level flex copper circuits are used when the board must have a heavy, bendable copper section for power applications and a thin flex section for attachment purposes. This is similar to rigid-flex but all bendable, and some parts are as normally flexible (1 oz. RA copper).
The flex base material has a very high voltage breakdown rating of 2000 volts per mil of thickness, which allows higher voltage use in a thinner, bendable package. The heavy copper can present difficulty during the etching operation, as the etch solution will etch down through the thick copper, creating a tapered effect. Typically, the amount of sidewall width lost is 1.5–2 times the copper thickness. This etching undercut means your line width to space is much larger than a typical 1-oz. copper circuit.
A 6-oz. copper line and space minimum starting width is around 30 mils. When you start with a 30-mil-wide trace in 6-oz. copper, the final trace width will be in the area of a 20-mil-wide trace. This loss of sidewall width must be accounted for in your Gerber data. Additionally, the spaces will widen by the same formula, creating wider spaces between tracks. Each manufacturer has its own set of design rules for etching heavy copper. Before you start to design your heavy-copper flex circuit, talk to your flex PCB shop to make sure you understand their different production guidelines and heavy copper limits as to thickness, trace, and space etching losses.
The heavy-copper flex can have plated vias, as well as multiple traces and circuitry. Some heavy-copper flex circuits can have components designed onto the surface, although they must be placed clear of any bend area. Heavy-copper flex-based circuits are used in applications where a flat, stiff, circuit board will not fit. Typically, heavy-copper flex circuits are single- or double-sided circuits with simple, open designs. Crowded, highly populated circuits do not bend well because the components do not bend.
When designing a bendable, heavy-copper flex circuit, consideration must be given to the placement of the components. All components must be kept clear of the bend lines. If only a small bend radius is required, some components, such as capacitors, will allow a very small radius.
Multilayers are possible but with limits on layer counts and significantly decreased ability to bend. As a multilayer is a composite construction consisting of many layers, it imparts a larger stiffness in the inability of adjoining layers to move in relation to each other, creating a rather stiff but bendable package.
A typical flex solder mask or cover coat can be used. The solder mask must be sprayed or applied in such a way as to cover the sides of the tall, heavy-copper traces. When a cover coat is used, extra layers of glue sheets are used to fill the gaps in between the higher heavy-copper traces.
An additional use of bendable, heavy circuit boards is the creation of vertical surface buss bars made by combining the attributes of a bendable flex board with heavy copper and designing the fingers to be soldered into the main PCB. These heavy-copper fingers that protrude off the board are made by removing the flex material portion with a sculpting laser, leaving the copper behind (Figure 1).
A bendable buss bar can snake around the surface vertically, supplying power and carrying heavy currents. The base printed circuit could be less expensive—typically a 1- or 2-oz. FR-4 PCB with the vertical, bendable power board carrying the current. Thermal dissipation would be increased because the buss bar would be vertical, increasing the thermal shear and airflow. Single-layer, double-layer, and multilayer designs could reduce the clutter and cost of a medium heavy-copper FR-4 PCB.
When designing bendable, heavy-copper flex buss bars, the copper must be thick enough to support the attachment fingers. The fingers could fit into a slot on the base FR-4 PCB or be surface mounted by bending the fingers at 90 degrees. A bendable, heavy-copper flex circuit can snake around the surface of a PCB, vertically supplying power and carrying heavy currents, creating a standard PCB with the bendable power board designed to carry the current throughout the entire rigid FR-4 PCB. Single, double, and multilayer heavy-copper flex designs could reduce the clutter and cost of a medium heavy-copper FR-4 printed circuit.
When a bendable, heavy-copper flex circuit is used for the previously noted PCB buss bar and plated with 10 oz. of copper, it will possess considerable strength. You can bend it into any shape, including 3D shapes, and it will retain that shape due to the thickness of the copper.
A bendable, heavy-copper circuit can withstand a small number of flex cycles. However, it is not designed to flex repeatedly. A properly designed and manufactured bendable, heavy-copper flex circuit of 6 oz. copper can bend as far as 360 degrees, in as little as one-inch diameter, for a few times—enough to shape and solder the heavy-copper flex circuit to the PCB base board. Some mechanical attachment device is suggested to keep the circuit in the desired shape if it utilizes 4 oz. of copper or less.
The heavy-copper, flex-based, buss bar can have plated vias, as well as multiple traces and circuitry (Figure 2). Some buss bars have components designed onto the surface, but they must be placed clear of any bend area.
When a heavy-copper flex PCB is used for a power supply, buss bar, and plated with 10 oz. of copper, it will possess considerable strength and weight with higher-than-normal reliability.
This column originally appeared in the October 2020 issue of Design007 Magazine.
More Columns from Consider This
Consider This: Designing Via-in-Pad for Higher Density Flexible CircuitsConsider This: Termination of Flex Circuits
Consider This: Reaching the Limit on Stiffeners
Consider This: PCB Technologies We Need Now and Later
Consider This: Advancements in Printed Circuit Manufacturing Equipment
Consider This: Buried Capacitance Power Planes
Consider This: Let’s Talk About the Basics of Flex
Acrylic vs. Epoxy Adhesives for Flexible Circuits