-
- News
- Books
Featured Books
- pcb007 Magazine
Latest Issues
Current IssueInventing the Future with SEL
Two years after launching its state-of-the-art PCB facility, SEL shares lessons in vision, execution, and innovation, plus insights from industry icons and technology leaders shaping the future of PCB fabrication.
Sales: From Pitch to PO
From the first cold call to finally receiving that first purchase order, the July PCB007 Magazine breaks down some critical parts of the sales stack. To up your sales game, read on!
The Hole Truth: Via Integrity in an HDI World
From the drilled hole to registration across multiple sequential lamination cycles, to the quality of your copper plating, via reliability in an HDI world is becoming an ever-greater challenge. This month we look at “The Hole Truth,” from creating the “perfect” via to how you can assure via quality and reliability, the first time, every time.
- Articles
- Columns
- Links
- Media kit
||| MENU - pcb007 Magazine
Estimated reading time: 3 minutes
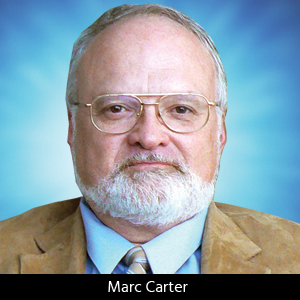
Contact Columnist Form
Better to Light a Candle: Chapter 10—Expanding the Base and Building the New
Editor’s Note: This column documents an effort to address one (of many) needs in developing the next generation of electronics manufacturers. This started with the university course in PCB manufacturing at Michigan Technological University (MTU). This class serves as a prototype for additional industry/academia local collaborative education/training classes in other parts of North America.
The first nine issues of this column series reported progress building grass-roots industry/academia collaborative efforts to prepare the next generation of PCB “experts.” Individuals and companies from all over the U.S. came together to pass on PCB experience through the prototype of a hands-on design, build, assemble, and test opportunity at MTU. You can review that history in back issues of this column here.
In this issue, I will concentrate on the remarkable line-up of guest lecturers (Figure 1) that will provide (due to COVID impediments) virtual lectures to this year’s class at Michigan Tech. Remote-learning sessions started on January 11. Most of these virtual lectures will be available as curriculum material as we build additional similar candidate groups for local academia/industry teams at other “nodes” around the country. Each of these industry/academia collaborations must be tailored to local workforce needs, academic capabilities, and the resources available to become self-sustaining.
In my February column, I’ll update you on the current status of expansion efforts at other locations and collaboration with other organizations.
Figure 1: The 2021 Michigan Tech Guest Lecture series. Note: lectures listed in red are not yet completely confirmed. As has been the case since the first year of this effort, we have more willing speakers than available sessions, as inevitably business travel, illness, etc., will force a change.
This year’s content provides a greater emphasis on design considerations, especially relating to “DFX” where “X” is electrical performance, manufacturability, or reliability, in both printed circuit fab and in assembly operations. For the first time, we’re addressing electronics packaging technologies and requirements with lectures from Vern Solberg and Steve Greathouse.
Most of these lectures will be included in a catalog of curricula materials that can be used to supplement or “core” in building additional local industry-academia education partnerships, tailored to local workforce needs, resources available, etc.
Those of you who have been in the industry will recognize some of the names on the list as “giants” in our world, and we’re humbled, grateful, and not surprised that they’re eager to give back some of their expertise to help ensure the ongoing strength of electronic manufacturing here.
Presently, a core team comprised of leaders from the industry, educators, SMTA, and DoD is meeting every other week to provide status updates on the other developing “nodes” around the country. The other sites under development range from two-year tech programs to four-year engineering degree add-ons, with content customized to match the local industry consensus on workforce need. The DoD input provides some travel and logistic support, if guest lecturers or set-up/start-up help is needed to fill a local gap, out of their concern for future availability of advanced electronics for the warfighter. Otherwise, the effort is exclusively voluntary at the individual level, though we’re extremely grateful to the participating corporations for their support of time, personnel, and materials.
Get Involved
Whether you’d like to be a part of this effort, or we can help you with a local project in electronics manufacturing workforce development along different lines, please reach out to one of the team.
Marc Carter has worked in the electronics interconnection industry since 1984 in a variety of roles in fabrication and assembly materials, processes, environmental compliance, and supply chain management activities around the world. He has had the honor and privilege of working with and learning from many of the true giants of this industry in multiple functions over many years. His experience includes a major mil-aero OEM, field and development work at materials suppliers to the printed circuit industry, and an educational stint as the sole proprietor of a manufacturer’s agency representing multiple high-tech mil-aero material suppliers. For further information, he can be reached at pmcarter01@outlook.com.
More Columns from Better to Light a Candle
Better to Light a Candle: A Solid Training Ground in New HampshireBetter to Light a Candle: Chapter 12—Light at the End of the COVID Tunnel
Better to Light a Candle: Chapter 11—Expanding and Adapting in the Face of the Pandemic
Better to Light a Candle: Chapter Nine—Growing Interest Around the Country
Better to Light a Candle: Chapter 8—Expanding the Model in This New Reality
Better to Light a Candle: Chapter Seven—Coping With COVID-19
Better to Light a Candle: Chapter Six—Spreading the Word
Better to Light a Candle: Chapter Five—2020 Reprise of MTU PCB Course