-
- News
- Books
Featured Books
- pcb007 Magazine
Latest Issues
Current IssueInventing the Future with SEL
Two years after launching its state-of-the-art PCB facility, SEL shares lessons in vision, execution, and innovation, plus insights from industry icons and technology leaders shaping the future of PCB fabrication.
Sales: From Pitch to PO
From the first cold call to finally receiving that first purchase order, the July PCB007 Magazine breaks down some critical parts of the sales stack. To up your sales game, read on!
The Hole Truth: Via Integrity in an HDI World
From the drilled hole to registration across multiple sequential lamination cycles, to the quality of your copper plating, via reliability in an HDI world is becoming an ever-greater challenge. This month we look at “The Hole Truth,” from creating the “perfect” via to how you can assure via quality and reliability, the first time, every time.
- Articles
- Columns
- Links
- Media kit
||| MENU - pcb007 Magazine
Estimated reading time: 4 minutes
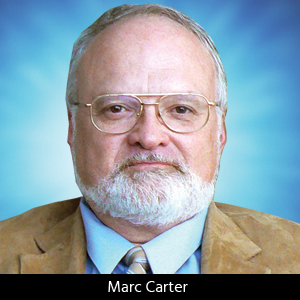
Contact Columnist Form
Better to Light a Candle: Chapter 12—Light at the End of the COVID Tunnel
Editor’s Note: This column documents an effort to address one need (of many) in developing the next generation of electronics manufacturers. This started with the university course in PCB manufacturing at Michigan Technological University (MTU). This class serves as a prototype for additional industry/academia local collaborative education/training classes in other parts of North America. The lecture side of this course, now completing its third year, is outlined in Appendix A, while the hands-on student design/fab/assemble/test opportunity has resumed full-force as we emerge from COVID pandemic constraints.
The past 11 issues of this column series reported progress building on the foundation of a prototype grass-roots industry/academia collaborative effort to prepare the next generation of PCB “experts.” This effort exists to support and facilitate post-secondary educational programs for next generation electronics manufacturing staff here in North America. The most recent column talked about some of the exciting new/expanding projects that are taking root around the country.
In this issue, we’ll continue in that direction, and report on a remarkable, exciting and daunting increase in attention this effort has received since last time. The “Electronics Manufacturing Technical Education Project” is a workforce development project that has attracted more official notice from Washington, with the concomitant more frequent demands for progress reports, etc. Whether it is linked to that, the perception that we’re coming out of the COVID tunnel, or just that the word is finally getting around, we’ve been approached by more companies and educational organizations asking about participation. This is good news, but we’ll see about how the bandwidth fares. In addition to more prospective nodes than we can handle with the original core team, we already have more lecture content and lecturers than can be included in one semester’s available lecture periods, which is a good problem to have.
Here’s a graphic submitted this past week in response to a query from (we’ve been told) Congress.
Figure 1: Key collaborations between academia and DoD suppliers.
And this (due to space considerations) omits ongoing and upcoming discussions with candidate “nodes” in Texas, Wisconsin, etc. To discuss possibilities in your region, contact myself or Tanya Martin, tanya@smta.org.
This is growing beyond our original, fairly modest, plans for three or four “startups” over a three-year period, and has already engendered a potential spin-off group pursuing professionally polished distance learning materials. Other organizations are leaning toward creating programs around elements of what we’ve begun, under their own brand, and we’re collaborating by offering “gap-filling” content as their success serves the ultimate goal of getting more young people in the pipeline to replace the dwindling “boomer” technical experience. More power to them!
As we’ve stressed repeatedly, our effort is just one thread in the larger tapestry needed. In our little corner, each of these industry/academia collaborations must start with a local industry consensus on short-term workforce needs, academic capabilities, and the resources available to maximize their chances to become self-sustaining. We’re trying to minimize “scope creep” by sticking to the original North American focus, but other groups are looking further afield. There are “nodes” that appear to be concentrating on microelectronics manufacture, flex-hybrid electronics, design focus, and ranging from short-duration “certificate” programs up through and including Master’s level programs.
As you can imagine, when we started this expansion effort in earnest (mid-2020), we anticipated we would be well along in meeting with local industry/academia hubs in organizing additional offerings around the country. The extended impact of the pandemic has seriously delayed that plan, which is best handled by a sense of humor.
Currently, a core team of leaders from industry, educators, SMTA, and DoD is meeting every other week to provide status updates on the other developing “nodes” around the country. We are actively discussing with the DoD’s Industrial Base Assessment and Sustainment group, through their Cornerstone OTA structure, whether the lingering impact of the pandemic requires modification of their support boundaries and a significant expansion in logistics.
Get Involved
Whether you’d like to be a part of this effort, or if we can help you with a local project in electronics manufacturing workforce development along different lines, please reach out to one of the team.
For further information, you can reach me at pmcarter01@outlook.com.
Marc Carter has worked in the electronics interconnection industry since 1984 in a variety of roles in fabrication and assembly materials, processes, environmental compliance, and supply chain management activities around the world. He has had the honor and privilege of working with and learning from many of the true giants of this industry in multiple functions over many years. His experience includes a major mil-aero OEM, field and development work at materials suppliers to the printed circuit industry, and an educational stint as the sole proprietor of a manufacturer’s agency representing multiple high-tech mil-aero material suppliers. For further information, he can be reached at pmcarter01@outlook.com.
More Columns from Better to Light a Candle
Better to Light a Candle: A Solid Training Ground in New HampshireBetter to Light a Candle: Chapter 11—Expanding and Adapting in the Face of the Pandemic
Better to Light a Candle: Chapter 10—Expanding the Base and Building the New
Better to Light a Candle: Chapter Nine—Growing Interest Around the Country
Better to Light a Candle: Chapter 8—Expanding the Model in This New Reality
Better to Light a Candle: Chapter Seven—Coping With COVID-19
Better to Light a Candle: Chapter Six—Spreading the Word
Better to Light a Candle: Chapter Five—2020 Reprise of MTU PCB Course