-
- News
- Books
Featured Books
- pcb007 Magazine
Latest Issues
Current IssueSales: From Pitch to PO
From the first cold call to finally receiving that first purchase order, the July PCB007 Magazine breaks down some critical parts of the sales stack. To up your sales game, read on!
The Hole Truth: Via Integrity in an HDI World
From the drilled hole to registration across multiple sequential lamination cycles, to the quality of your copper plating, via reliability in an HDI world is becoming an ever-greater challenge. This month we look at “The Hole Truth,” from creating the “perfect” via to how you can assure via quality and reliability, the first time, every time.
In Pursuit of Perfection: Defect Reduction
For bare PCB board fabrication, defect reduction is a critical aspect of a company's bottom line profitability. In this issue, we examine how imaging, etching, and plating processes can provide information and insight into reducing defects and increasing yields.
- Articles
- Columns
- Links
- Media kit
||| MENU - pcb007 Magazine
Estimated reading time: 5 minutes
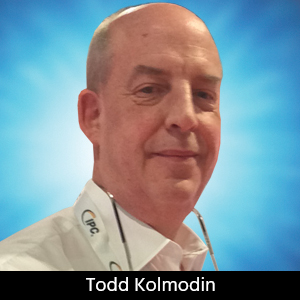
Testing Todd: Owning Your Processes
I hope everyone is getting through this pandemic as best as possible. Keep hanging in there. Things will improve. Speaking of improvement, how are your processes and work instructions holding up? I’m sure current times have caused modifications in how we do things now. Have you audited them lately? That’s what I figured. Don’t feel bad. It’s extremely common to write a process or work instruction and let it loose in the wild to thrive. The problem is, if there is a problem or a glitch it may never get noticed. Why, you ask? It’s simple. Humans have an extraordinary ability to adapt.
A perfect scenario is a process that was written to operate the Acme 1000 widget maker in 1983. Millions of widgets have been made since 1983. However, in 2007 the Acme 1000 was replaced by the Acme 5000. The new machine quadrupled output, everyone was extremely happy, and all was well with the world. That was until John abruptly left the company. He had operated that machine and process since 1983. The company adjusted, of course, and Susan took over. There was a work instruction for the process, so everything should’ve been fine, right? Unfortunately, output dropped, and the widgets were being rejected at quality control at a much higher rate than what was acceptable. What was Susan doing wrong? Was the machine broken? Neither. Remember we replaced the machine back in 2007? What happened? Well, we didn’t review the process when we updated the machine and John adapted. He adapted to the new environment—in this case the updated machine—and life went on. The pitfall was that, like an embezzler, the problems will not surface until the criminal is removed from the environment. By no means am I calling John a criminal but the oversight of reviewing the process or work instruction after the machine was upgraded led to unavoidable future problems.
Now, before management goes after Susan with torches and pitchforks, we need to understand what happened: we didn’t own the process. So often what happens is that a clinical process is written by engineering when the machine is placed, and then forgotten. As we all know, evolution is unavoidable and better techniques are found. We need to keep our thumbs on the pulse of processes and allow them to evolve. Therefore, we need to control them. I don’t know about you, but I have seen many times that the best way to develop a process or work instruction is to find the people that operate the machine or perform the task on a daily basis. You can have a fleet of engineers, which is fine, but I can tell you from experience that the best way to fine tune a process or work instruction is to gather valuable input from the operators who perform the task.
Since this is the year of continuous improvement, let’s look at a good foundation to own that process or work instruction. Although some what I’m going to outline may seem obvious, you would be surprised how many times it can be overlooked and cause unnecessary rework and corrective action.
The best way to start this activity is with both engineering and operators involved. The team approach works very well even if the team is only two participants.
Phase 1: Look at the task or process from the 10,000-foot level, meaning you should look at the task you wish to document as it may affect other activities related to it. Look at space requirements, labor burden, tools required, facilities, and ergonomics.
Phase 2: Clinically create the task or process. This can be anything from factory installation to operating instructions. Place necessary tools and supplies as needed. Once documented, perform a dry run through the process to make sure critical steps are captured.
Phase 3: Train your operators to the new document or process. Have them walk through it more than once. Now, this is normally where the process creation task ends and what causes the most problems. The operators are trained and off we go. The work instruction goes to the training library and the engineers move off to another new project.
But wait, there’s more! Now the control mechanisms need to be in place. This is what determines whether a process will thrive and evolve or whether it will eventually fail when minor attributes change.
Phase 4: Develop KPIs (key performance indicators) or control attributes. One can create many processes or instructions and never know whether they are a benefit or a distraction. A process or work instruction is created to standardize or create repeatability of a task. Without monitoring, the process or task can get out of control without any restraints which causes waste or scrap. Keeping a thumb on the pulse can quickly identify an anomaly before it affects down line processes or quality of the product.
Phase 5: Review the process. This is the game changer. A process or task should be reviewed at least once a year or whenever any significant change happens. (See Phase 1 objectives for a hint.) If something changes, what effects will it have on surrounding tasks or environment? Review your KPIs daily, weekly, or monthly depending on the importance of the task. Consult with the operators who perform the task and gauge repeatability between operators. If there is a difference, find out why. Did an operator evolve and find a better way to perform the task? Or are they cheating and jeopardizing the process? This is where adjustments can be made before control is lost. Using a 5S concept, look to see if the task or process can be improved. Look to eliminate waste, such as time, movements, or other factors. If corrections are found, go back to Phase 2, make the corrections and continue the loop.
This outline gives continuous control of tasks or processes and will not allow out-of-control scenarios to develop. If they do, depending on KPI review frequency, they can be captured and corrected expediently. It also keeps a standardization from operator to operator or shift to shift.
Stay safe!
This column originally appeared in the February 2021 issue of PCB007 Magazine.
More Columns from Testing Todd
Testing Todd: Why 4-wire Kelvin?Testing Todd: Why TDR?
Testing Todd: Positivity Boosts Employee Morale
Testing Todd: Preparing Employees for the Long Haul
Testing Todd: Where Can We Improve?
Testing Todd: Turning Into the Wind
Testing Todd: Coming Back to Life—Design Recovery
Testing Todd: Decision Time—Invest or Delegate?