Foxconn’s Chengdu Campus Recognized as Lighthouse Factory
March 16, 2021 | FoxconnEstimated reading time: 3 minutes
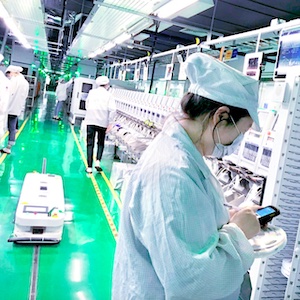
Foxconn Technology Group announced that a second of the company’s factories, a factory based in Chengdu, China, has been recognised by the World Economic Forum (WEF)’s Global Lighthouse Network (GLN) as a Lighthouse factory. The accolade is awarded to manufacturing leaders who have been successful in applying Fourth Industrial Revolution technologies to achieve profitable growth without increasing their environmental footprint. Confronted with fast-growing demand and labour skill scarcity, Foxconn Chengdu adopted mixed reality, artificial intelligence (AI) and internet of things (IoT) technologies to increase labour efficiency by 200% and improve overall equipment effectiveness by 17%.
The GLN is a community of production sites and other facilities that are world leaders in the adoption and integration of the cutting-edge technologies of the Fourth Industrial Revolution (4IR). Lighthouse factories apply 4IR technologies such as artificial intelligence, 3D-printing and big data analytics to maximize efficiency and competitiveness at scale, transform business models and drive economic growth, while augmenting the workforce, protecting the environment and contributing to a learning journey for all-sized manufacturers across all geographies and industries.
Foxconn Chengdu achieved its status through digitization
As the world’s leading electronic manufacturing group, digitization is a key strategy for Foxconn to continuously improve manufacturing and management capabilities to address the needs of customers who include many of the world’s leading technology companies. Innovative technologies continue to be a key driver of the company’s digital transformation, bringing about improved connectivity in human-human interaction, human-machine interaction and machine-machine connectivity.
At Foxconn’s Chengdu site, confronted with skyrocketing market demands, a shortage of skilled labour and rapidly growing product complexity, the company chose to extensively leverage cutting-edge artificial intelligence and IoT technologies to introduce worry-free production. As part of that process, the workforce was trained with advanced intelligent capabilities and as a result, achieved remarkable operational improvements.
The independent panel that evaluated the Chengdu site attributed five factors towards its recognition as a Lighthouse Factory:
- Increased labour efficiency by 200% and improved overall equipment effectiveness by 17%
- Artificial-intelligence-powered optical inspection – decreased manual inspection by 92%
- Predictive maintenance aggregating historical and sensor data – overall equipment effectiveness increased by 17%
- IoT-enabled manufacturing quality management – decreased quality alert time by 99%
- Production planning optimized by advanced analytics – decreased inventory by 25%
“It is an honour for us to have the WEF Future Manufacturing Council recognize our work with both the Shenzhen and Chengdu factories. It validates the hard work of our teams throughout the Foxconn Group. The first lighthouse factory meant that we had a factory that met the high standards of the Global Lighthouse Network. This second designation is testament to the system we have built in the operation of factories that play leading roles in the world’s industrial revolution. Foxconn is committed to continuously improving on our manufacturing systems and to building even more lighthouse factories as we serve our customers and contribute to a better world,” said Young Liu, Chairman, Foxconn Technology Group.
Francisco Betti, Head of Shaping the Advanced Manufacturing and Production Platform at the World Economic Forum said in commenting on the announcement of the new Global Lighthouse factories, “This is a time of unparalleled industry transformation. The future belongs to those companies willing to embrace disruption and capture new opportunities. Today’s disruptions, despite their challenges, are a powerful invitation to re-envision growth. The lighthouses are illuminating the future of manufacturing and the future of the industry.”
In 2019, Foxconn implemented Foxconn 2.0 as part of their digital transformation strategy. The main focuses of the initiatives were: customer experience, intelligent decision making and smart manufacturing—all areas where the lighthouse factory projects excelled. Digital tools, including Foxconn’s IoT platform, big data analytics, AI and other related technologies, are being harnessed in these and other Foxconn facilities around the world to build a more flexible and agile organization. Additionally, with the ability to better diagnose, predict, and design products and better manage their supply chain and manufacturing operations, Foxconn is realizing optimal production levels with higher levels of certainty.
Testimonial
"Our marketing partnership with I-Connect007 is already delivering. Just a day after our press release went live, we received a direct inquiry about our updated products!"
Rachael Temple - AlltematedSuggested Items
SEMICON Europa 2025 Spotlights Global Collaborations for European Economic Resilience
08/28/2025 | SEMISEMICON Europa 2025, co-located with productronica, will return to Munich from November 18-21 to mark its 50th anniversary, bringing together global industry leaders, innovators, and policymakers to strengthen Europe’s position in the global semiconductor landscape. Registration is open.
North American EMS Industry Shipments Down 4.1% in July
08/27/2025 | Global Electronics AssociationThe Global Electronics Association announced today the July 2025 findings from its North American Electronics Manufacturing Services (EMS) Statistical Program. The book-to-bill ratio stands at 1.23.
SIA Statement on Semiconductor Tariffs Announcement
08/27/2025 | SIAThe Semiconductor Industry Association (SIA) released the following statement from SIA President and CEO John Neuffer regarding President Trump’s semiconductor tariff announcement.
SMTA Elects New Board Members
08/27/2025 | SMTAThe SMTA is pleased to announce its election results for the Global Board of Directors for the term beginning October 19, 2025. Elizabeth Benedetto, HP Inc.; Pratish Patel, Electronic Interconnect; and Sutharshan Suppiramaniam, SMT Elite Corporation, have been newly elected to the Board of Directors for the term 2025-2028.
L3Harris Begins Sensor System Manufacturing in Poland
08/26/2025 | L3Harris TechnologiesL3Harris Technologies has begun manufacturing electro-optical/infrared (EO/IR) sensor systems at a 2,000-square-meter facility in Katowice.