-
- News
- Books
Featured Books
- pcb007 Magazine
Latest Issues
Current IssueSales: From Pitch to PO
From the first cold call to finally receiving that first purchase order, the July PCB007 Magazine breaks down some critical parts of the sales stack. To up your sales game, read on!
The Hole Truth: Via Integrity in an HDI World
From the drilled hole to registration across multiple sequential lamination cycles, to the quality of your copper plating, via reliability in an HDI world is becoming an ever-greater challenge. This month we look at “The Hole Truth,” from creating the “perfect” via to how you can assure via quality and reliability, the first time, every time.
In Pursuit of Perfection: Defect Reduction
For bare PCB board fabrication, defect reduction is a critical aspect of a company's bottom line profitability. In this issue, we examine how imaging, etching, and plating processes can provide information and insight into reducing defects and increasing yields.
- Articles
- Columns
- Links
- Media kit
||| MENU - pcb007 Magazine
Estimated reading time: 6 minutes
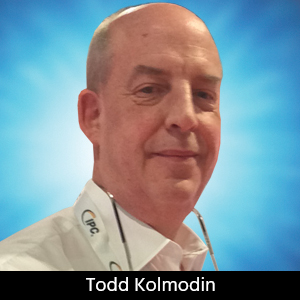
Testing Todd: Homing in on the Target
Although electrical testing provides a beneficial safeguard against an electrically inferior product reaching a customer, it does require adherence to critical processes. One of those processes is the inspection for witness marks or pin marks. The caveat of electrical test is that it needs to be done but at the same time, optimally, there should be no evidence it was performed. This can be a difficult process, especially on some of the more delicate finishes such as immersion silver or soft gold. The horrors of a complex multilayer order scrapping because of one stuck test pin during electrical test keeps sales personnel awake at night. Therefore, a robust inspection process is necessary.
In the past this was not as critical, as bare copper is robust and HASL could easily be reworked. However, as surface finishes have advanced and pad sizes reduced, a stuck fixture pin or overly aggressive flying probe compression can be catastrophic. In Figure 1, we see an example of severe damage caused by a malfunctioning test fixture. In most cases this scenario is fatal to the product.
A live inspection process is the most successful approach to minimizing loss due to test damage. This is not just limited to inspecting the product (which we do) but must include steps prior to that before product is even tested. Although this is more critical with fixture testers, inspection of the test probes, clamping mechanism, and automatic handlers (if applicable) should be inspected prior to testing on flying probes as well. For fixture testers it becomes more in-depth. First, you have the fixture itself which, depending on the scenario, may be a new build or an older repeat part where the fixture was stored for a length of time. This requires inspection of the fixture for missing or bent pins, faulty assembly, or damage incurred during storage. Next is the fixture integration to the fixture tester. The fixture needs to operate freely with no stuck pins. The largest variable contributing to damage is a bent pin or pin side-loading (pin sticking to the side wall of grid stripper plate), which locks the pin from free movement. Once this has been performed the electrical validation should take place. This includes a continuity and isolation test against a copper sheet (continuity) and non-conductive sheet (isolation.) These tests conclude the following:
- Continuity: All pins are moving freely and conduct correctly to the fixture tester electronics. This will also identify faulty connections or missing pins.
- Isolation: Provides validation that no shorts exist in the test matrix, either pin-to-pin in fixture or faulty test electronics.
It should only be after these critical setup steps are performed that the product be committed to test. When to inspect is now the question, isn’t it? Absolutely. On fixture testers the optimum scenario is to run a test cycle on a pre-scrap board if one is available. However, many times there are none available and a live board must be used.
(Personal note: If the fixture has a diary or log of past performance, do not just use the logged compression values! This can be fatal as mechanical changes may have been made due to maintenance or service repairs.)
Always run at the least possible compression to provide desirable results. Once the board has been tested, regardless of the result, it should be inspected for witness marks. Do not trust your eye alone as with product technology today you will not be able to perform a valid inspection with the naked eye. It should be viewed under a scope.
Now, what to inspect? The examination should cover the entire board, but significant detailed inspection should isolate on the high-density areas and small pads. These areas are more prone to heavy witness marks as the pins are usually quite small and are more susceptible to damage. Figure 2 shows an example of higher density areas that should warrant higher scrutiny. Once the inspection is complete it can be determined whether continuing with testing is allowed or intervention is required. Intervention is usually an adjustment in compression or perhaps replacement of a test pin or two.
Once testing has begun it is recommended that an inspection matrix be created. How often should we inspect the product during the process? Inspecting 100% of a large order is counterproductive, I understand. Therefore, the matrix is necessary. Should we inspect every 10, 20, or 50? Early rules suggest first, middle, and last board of an order. This can work if the order is only 10–15 boards. Worst case scenario if the fixture test causes damage, it would be caught at the inspection interval. If we had 15 boards, we could catch it after board 5, or board 10. Although it could result in a loss of product it would be limited due to the inspection interval. It may be your local process to inspect all boards in that size of order and this is fine. The question really is based on large orders. We should still inspect the first and last board but if we wait until the middle of a large order, we could lose a significant amount of product, especially if the order is 100 pieces or larger. Here is where QMS discretion is advised. The matrix could break down the order by percentage and create an interval for inspection or it could simply state that on orders of X pieces or larger, every X board needs to be inspected. This allows containment quickly should a fatal error occur during test. It must also be noted that there should be a referee inspection done during these inspection intervals. This is simply referred to as a “buddy check.” It is proven that the second set of eyes may capture a witness mark defect that is overlooked by the primary inspector. Repeatedly inspecting small pads and lines can be monotonous and pattern recognition fatigue can cause the visual senses to tire.
So now we have a setup process and a good understanding of the inspection process, and how, where and when to do it. Again, this all is part of the continuous improvement and quality assurance discipline. We need to own our processes and live them as well. Having integral steps in a process where it requires more than one person during a KPI check or inspection is always beneficial. This is by no means a knock to the primary operator but as humans, we can get tired, fall into repetition, and with that comes an increased margin for error.
As newer technologies emerge the ultimate solution would be to add AVI (automated visual inspection) to the final FA process. Even though we are inspecting the boards at regular intervals there remains a margin for error. Using a process where the test is performed and then an AVI is used to scan the surface of the board and sort by “pass” and “fail’ would capture any and all surface defects.
Line = ET Tester + AVI Inspection + Auto sort pass/fail.
Another item to mention is where the mark may be placed. Many specifications call out the probing area “allowed.” Many times, mechanical drawings may state a “pristine area” of the pad. This cannot have any marks whatsoever. It can be difficult many times, but when it’s unavoidable, the absolute lightest contact must be made. In Figure 3, we show very light contact in a high-density BGA.
Today’s extreme densities and small pads are getting to the point that pinned fixtures are no longer the solution and flying probes or high-density wired dedicated fixtures are required.
I close with some finishes (Figure 4) that we come across routinely. By far the most susceptible finishes are the soft gold and immersion silver families.
Stay safe!
This column originally appeared in the March 2021 issue of PCB007 Magazine.
More Columns from Testing Todd
Testing Todd: Why 4-wire Kelvin?Testing Todd: Why TDR?
Testing Todd: Positivity Boosts Employee Morale
Testing Todd: Preparing Employees for the Long Haul
Testing Todd: Where Can We Improve?
Testing Todd: Turning Into the Wind
Testing Todd: Coming Back to Life—Design Recovery
Testing Todd: Decision Time—Invest or Delegate?