-
- News
- Books
Featured Books
- pcb007 Magazine
Latest Issues
Current IssueSales: From Pitch to PO
From the first cold call to finally receiving that first purchase order, the July PCB007 Magazine breaks down some critical parts of the sales stack. To up your sales game, read on!
The Hole Truth: Via Integrity in an HDI World
From the drilled hole to registration across multiple sequential lamination cycles, to the quality of your copper plating, via reliability in an HDI world is becoming an ever-greater challenge. This month we look at “The Hole Truth,” from creating the “perfect” via to how you can assure via quality and reliability, the first time, every time.
In Pursuit of Perfection: Defect Reduction
For bare PCB board fabrication, defect reduction is a critical aspect of a company's bottom line profitability. In this issue, we examine how imaging, etching, and plating processes can provide information and insight into reducing defects and increasing yields.
- Articles
- Columns
- Links
- Media kit
||| MENU - pcb007 Magazine
Estimated reading time: 3 minutes
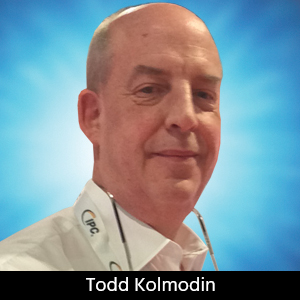
Testing Todd: A Point of Order—Do Not Just Rearrange the Pencils!
In our concentration on continuous improvement, we should look at the order of things. Efficiency comes from streamlining processes, effective training, and the ability to monitor success through KPIs and feedback on deliverables.
Most companies are familiar with or have implemented Quality Management Systems (QMS). Continuous improvement is a key factor in all quality programs. You simply cannot improve if you don’t know where you are! There are many tools out there to review and monitor efficiency. Honestly, the most effective process is one that provides maximum output with minimal effort or cost, right?
“Lean and mean” is the way to go and to get there we need to get Lean. One of the best tools available to gauge and review processes and work areas is the 5S discipline.
This process, developed in Japan, provides two frameworks: one by Osada, the other by Hiroyuki Hirano. Both follow the steps of the discipline but the compressed “4S” model combines “Set in Order” and “Shine” into one step. I’ve been involved in many 5S workshops and it can be applied to the simplest of tasks as well as to large multi-faceted departments. Let’s get Lean!
Sort (seiri)
This fundamental step begins the process. As I mentioned, we cannot improve unless we know where we are. Take a “bird’s eye” view of the task, workspace, or process. Look at the flow, tools, equipment, tables, chairs, etc. Decide what items are absolutely needed. Remove items that are redundant, unnecessary, or distracting. What we are trying to do here is simplify the task or process utilizing space and increase safety by eliminating distractions and possible hazards.
Set in Order (seiton)
Now that we know all we need for the task or process, we need to review it for efficiency. This can be placement of equipment, desks, tools, and other such items necessary. Look at the flow and optimize as necessary. This should consider distance movements, ergonomics, and safety. Remember, a high percentage of down-time or failure in a process is related to the human variable.
Shine (seiso)
With our task or process optimized, we need to keep it that way. We need to keep the area clean and maintained. Depending on the task or process, this may be daily cleaning, sweeping, or inspection. This keeps the area on-point and continuously operating as we designed.
In some operations as noted in the beginning, “set in order” and “shine” are combined, resulting in a 4S plan. Still valid as all steps are considered.
Standardize (seiketsu)
This step is why I like the 5S discipline. Here is where the new process is documented once you have all the steps in place. We have outlined what is necessary, removed clutter, and organized for optimum efficiency. Now we document the process so that the task is repeatable and defined. We now know where we are and can duplicate the results. Well done!
Sustain (shitsuke)
Now that we have a perfect process or workflow, we have come to the last and most difficult step. What happens in many instances is that we develop the great process and workspace only to review it in a month’s time and it has fallen into utter chaos. Am I right? You are nodding your head. This is the step that gets forgotten. We need to police the area regularly to validate the success. Optimally this can be done by a performance indicator (KPI) or maintenance interval where the area is reviewed, equipment and tools inspected, and, importantly, debrief of operators involved for feedback. Adjustments can then be made with emphasis on reviewing the first four steps to see if there is an impact.
I know I am not bringing up anything new and I am sure many of you have already lived through the 5S discipline workshop. However, as 2021 is focused on continuous improvement it is appropriate to revisit some of the tools that can positively impact manufacturing and general workflow.
Within our group we always strive to find 5S projects as part of continuous improvement. However, when identifying these project areas, we must not “just 5S” because I must find one. 5S is a discipline and not just a project. Rearranging pencils or cleaning one’s desk does not really cut it as a 5S unless one embraces the five (or four) steps needed with the discipline. Countless times I have seen an office 5S where, of course, it is neat and tidy initially only to be a train wreck three weeks later. 5S = Fail!
Stay Lean, my friends!
This column originally appeared in the April 2021 issue of PCB007 Magazine.
More Columns from Testing Todd
Testing Todd: Why 4-wire Kelvin?Testing Todd: Why TDR?
Testing Todd: Positivity Boosts Employee Morale
Testing Todd: Preparing Employees for the Long Haul
Testing Todd: Where Can We Improve?
Testing Todd: Turning Into the Wind
Testing Todd: Coming Back to Life—Design Recovery
Testing Todd: Decision Time—Invest or Delegate?