-
-
News
News Highlights
- Books
Featured Books
- pcb007 Magazine
Latest Issues
Current IssueThe Hole Truth: Via Integrity in an HDI World
From the drilled hole to registration across multiple sequential lamination cycles, to the quality of your copper plating, via reliability in an HDI world is becoming an ever-greater challenge. This month we look at “The Hole Truth,” from creating the “perfect” via to how you can assure via quality and reliability, the first time, every time.
In Pursuit of Perfection: Defect Reduction
For bare PCB board fabrication, defect reduction is a critical aspect of a company's bottom line profitability. In this issue, we examine how imaging, etching, and plating processes can provide information and insight into reducing defects and increasing yields.
Voices of the Industry
We take the pulse of the PCB industry by sharing insights from leading fabricators and suppliers in this month's issue. We've gathered their thoughts on the new U.S. administration, spending, the war in Ukraine, and their most pressing needs. It’s an eye-opening and enlightening look behind the curtain.
- Articles
- Columns
- Links
- Media kit
||| MENU - pcb007 Magazine
Estimated reading time: 4 minutes
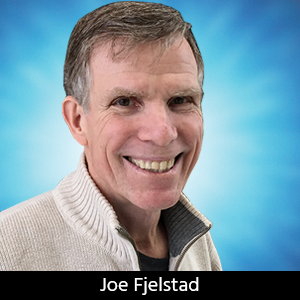
Flexible Thinking: Process Flow for Occam QFN Test Vehicle
If you have followed my quixotic pursuit to convince the electronics industry of the many benefits of fabricating electronic assemblies without solder over the last 13-plus years, you are likely (or hopefully) familiar with the structures and methods I have advocated to build what I call Occam process assemblies. The solutions I have offered in my writings (there is more than one way to build such assemblies) can significantly reduce the number of process steps required to manufacture an electronic module or assembly (perhaps by as much as one-third) and in the process make electronic assemblies more reliable and less costly by fundamentally focusing on the elimination of solder and the soldering process.
Those who have been in the electronics manufacturing industry for any length of time likely know well that solder and the soldering process are the root cause of most defects and failures in electronics. According to one recent survey, approximately 80% of problems experienced in assembly are related to soldering, including not just faulty soldering but also damage to the PCB structure (delamination) and damaged plated vias.
My effort to teach the Occam process to the electronics industry culminated in a free book titled, Solderless Assembly For Electronics—The SAFE Approach. For those who have not yet downloaded and flipped through the pages of this short book, the Occam Process is fundamentally a reverse order approach to manufacturing electronics assemblies; that is, rather than building a circuit board and soldering components to it surfaces, the suggestion is that the industry design and build “component boards” and then build up the circuits on the assembly. Originally, I called it a Reverse Interconnection Process with “RIP” as its acronym, but quickly realized that such an acronym would not instill confidence in prospective users (wink).
In my book, I have listed many reasons why it makes arguable sense to adopt the “SAFE” approach, but for the purpose of this column the focus will be on one benefit that is becoming increasingly important: thermal management of electronic components. Why? Because heat has always been an enemy of electronic assemblies. Every heat exposure above a certain threshold reduces the long-term reliability of an electronic module by a small amount, those exposures have a cumulative effect, and they add up. Moreover, one of the biggest thermal shocks inflicted on an electronics assembly during its life occurs during the soldering process, which might happen two, three, or more times during assembly. This can be followed by rework which further degrades the electronics, so approaches that eliminate high temperature exposure (including pursuit of low temperature solders) are “low hanging fruit” from a targeting standpoint.
However, the thermal problem doesn’t end there. Heat of operation is another ongoing problem faced by the industry, and QFNs, as attractive as they are, are one of the more vulnerable component types. Over the last several years, QFNs are being increasingly called upon to address electronic module design due to their minimalist size and performance benefit, but making full solder connection to the thermal pad on the bottom of QFNs has been one of the more vexing problems facing assemblers. Thus for the balance of this article, QFNs will be used as exemplar components for this brief discussion and description of a method for building an electronic module that is, in and of itself, a thermal spreader.
The series of story board graphics and their accompanying descriptions are provided in the magazine version of this column and are intended to allow the reader to quickly grasp these concepts. What follows is an animation of the "12-Step Occam Process" of the just those graphics:
Discussion
What has been presented is a novel way to address the increasingly vexing problem that the industry has been battling for decades: effective heat removal from an electronic module. As one of my trusted advisors, thermal management guru Bernie Siegal, shared with me when I first showed him the idea a dozen years ago, “This approach allows the thermal guys to solve the thermal problems on the front-end design rather than at the end.”
Those who have skill in the manufacture of printed circuits should be able to appreciate the steps shown, and I trust they can also see how it can be done and accomplished using existing materials equipment and processes. No attempt is being made to identify all the prospective materials, both permanent and process consumable, that might be employed. There are simply too many to list, especially when the need to endure the soldering process is removed from the list of requirements and assembly must endure during manufacturing.
Presently there is an effort underway to build out demonstration Occam assemblies to once and for all remove doubt from the minds of those who have adamantly asserted that the concept will not work. As an optimist, I am inclined to share the words of a kindred iconoclast from early in the last century, Henry Ford, who opined: “Whether you think you can, or you think you can't—you're right.”
I look forward to sharing the results of the forthcoming efforts with readers when they are available.
For more details, the original version of this column appears in the May 2021 issue of Design007 Magazine.
More Columns from Flexible Thinking
Flexible Thinking: The Key to a Successful Flex Circuit Design TransferFlexible Thinking: Flexible Circuit Technology—Looking Back and Forward
Flexible Thinking: Mind-tapping into January
Flexible Thinking: Another PCB Design Paradigm Shift in the Works
Flexible Thinking: Rules of Thumb—A Word to the Wise
Flexible Thinking: Musings on High Density Interconnections
Flexible Thinking: Integrated Passive Devices—Design Solutions With Many Benefits
Flexible Thinking: Mechatronics in a Flex World