-
- News
- Books
Featured Books
- pcb007 Magazine
Latest Issues
Current IssueInventing the Future with SEL
Two years after launching its state-of-the-art PCB facility, SEL shares lessons in vision, execution, and innovation, plus insights from industry icons and technology leaders shaping the future of PCB fabrication.
Sales: From Pitch to PO
From the first cold call to finally receiving that first purchase order, the July PCB007 Magazine breaks down some critical parts of the sales stack. To up your sales game, read on!
The Hole Truth: Via Integrity in an HDI World
From the drilled hole to registration across multiple sequential lamination cycles, to the quality of your copper plating, via reliability in an HDI world is becoming an ever-greater challenge. This month we look at “The Hole Truth,” from creating the “perfect” via to how you can assure via quality and reliability, the first time, every time.
- Articles
- Columns
- Links
- Media kit
||| MENU - pcb007 Magazine
Estimated reading time: 4 minutes
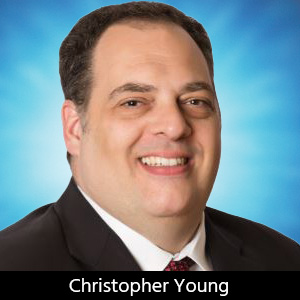
Adventures in Engineering: It's Pronounced 'Tooling Holes'
Tooling holes are more than a type of mounting hole used in PCBs to aid in the assembly of printed circuit board assemblies (PCBAs). Tooling holes are used for aligning, inserting, and extracting PCBAs in higher level assemblies because they are precise mechanical references embedded into the PCB. The differences between mounting holes and tooling holes are subtle but important, nonetheless. Tooling holes deserve their own designation within the PCB design environment.
As precise mechanical references, tooling holes are used in a wide range of higher-level assembly processes. When matched appropriately with dowel pins, tooling holes can be used for precision alignment of PCBAs in electromechanical assemblies. A dowel pin is typically a cylindrical metal rod that has a chamfered end. However, they do come in many shapes and sizes. The following image is an example of how a PCBA can be aligned with a pogo pin plate assembly and a board stiffener.
Figure 1: Example of a tooling hole.
Dowel pins are used to align a PCBA, board stiffener, and pogo pin socket plate. The sub-assembly shown is part of a clam shell test fixture used to test a panelized set of PCBAs (commonly referred to a DUT panel). This alignment is critical because the pogo pins that are inserted in the sockets interface with the panel PCBA for parametric and functional test of the individual devices under test (DUTs). Precise targeting of the pogo pins in the test fixture to test points on the DUTs is critical for repeatable error free high-volume throughput.
Tooling holes are not only just round holes in the PCB; they can take on many different shapes to aid in the higher-level assembly process. I have seen slotted tooling holes used to keep a PCBA locked in a single dimension so that two high insertion force connectors can be mated properly. Triangle, hexagon, and semi-circle shaped tooling holes have been used as keying mechanisms so that similar looking PCBAs do not get installed in a wrong backplane or assembly by mistake. The premise here is that tooling holes have a multitude of uses and vary in size/shape.
My main point of contention with identifying a tooling hole as a type of mounting hole is the ambiguity involved in such a classification. When designing the mechanical features of a PCB, how do you differentiate mounting holes from tooling holes? Is it implied by their locations? Do you have callouts in the fabrication data? Do you export a step file of your design for use in a 3D CAD tool? Is it based on the tolerances assigned to different drill holes in the design? This leads to miscommunication of where tooling holes need to be placed, usually because assumptions are made. The typical result is that a re-spin is in order.
Early in my career I was responsible for a board design that involved a right-angle, high-density connector with over 500 pins. Each pin had an insertion force of one-eighth pound and an extraction force of one-fourth pound. It took a little over 62.5 pounds to insert the board and over 125 pounds to remove the board. These force specifications were valid for a narrow angle of entry/exit of the right-angle connector to the backplane connector. Two sets of tooling holes were used to accomplish appropriate insertion/extraction. Round tooling holes served the dual functions of insertion/extraction load points and PCBA assembly/clamshell test alignment. Slotted tooling holes were used to minimize rocking at an angle during insertion/extraction of the PCBA. These tooling holes were placed and treated as mounting holes in the design. When these PCBs were built, the fabricator asked for relaxation of the requirements of the mounting holes in the design. They were given permission by our manufacturing engineer and the round tooling hole placement was adjusted on one side of the PCB only. This introduced a forced rocking angle that was not caught during development and certification of the product. When the product entered mainstream production with higher quantities and part variations, the backplane connectors started ripping out of the backplane when board extractions were performed. It turns out the uneven placement of the tooling holes were responsible for two connectors binding, and the press fit backplane connector ended up being the loser in the tug of war that would ensue. The root cause of the problem was identified as a lack of specifications surrounding specific mounting/tooling holes causing the manufacturing engineer to make an incorrect assumption. The result was three re-spins: my board, the backplane board, and the insertion/extraction tool, to specifically avoid this issue in the future.
How can we solve the issue of ambiguity surrounding tooling holes? CAD tool vendors have and are implementing cross platform integration between PCB and 3D CAD tools. This is progress in a good direction but does not solve the issue at hand. PCB and 3D CAD designers still need to communicate the specifics about what they are co-designing. Direct integration between CAD platforms do not differentiate between tooling and mounting holes because they are defined as the same thing, a mounting hole. What I am proposing is a specific designation for tooling holes within the CAD tools themselves—a separately searchable, reportable, and identified item defined explicitly as a tooling hole. This type of unique treatment is like a fiducial, test point, and/or mounting hole. The idea is to explicitly identify tooling holes within the CAD tool environment to avoid assumptions and miscommunications which inevitably lead to redesigns. I would like to start a new tooling hole motto, “There is no ‘M’ in Tooling Hole.”
Chris Young is owner/lead engineer of Young Engineering Services LLC and chief hardware engineer at The Goebel Company.
This column also appears in the June 2021 issue of SMT007 Magazine.
More Columns from Adventures in Engineering
Adventures in Engineering: A Penny Primer on PCB Design FundamentalsAdventures in Engineering: 5G Expansion and Radar Altimeters
Adventures in Engineering: Supply Chain Management
Adventures in Engineering: Data Management Not Just Checking the Boxes
Adventures in Engineering: Connectors—The Right Fit
Adventures in Engineering: A Purpose-Driven Prototype
Adventures in Engineering: Test Points—The Other Side
Adventures in Engineering: The Ecosystem of Autonomous Flight