-
- News
- Books
Featured Books
- pcb007 Magazine
Latest Issues
Current IssueInventing the Future with SEL
Two years after launching its state-of-the-art PCB facility, SEL shares lessons in vision, execution, and innovation, plus insights from industry icons and technology leaders shaping the future of PCB fabrication.
Sales: From Pitch to PO
From the first cold call to finally receiving that first purchase order, the July PCB007 Magazine breaks down some critical parts of the sales stack. To up your sales game, read on!
The Hole Truth: Via Integrity in an HDI World
From the drilled hole to registration across multiple sequential lamination cycles, to the quality of your copper plating, via reliability in an HDI world is becoming an ever-greater challenge. This month we look at “The Hole Truth,” from creating the “perfect” via to how you can assure via quality and reliability, the first time, every time.
- Articles
- Columns
- Links
- Media kit
||| MENU - pcb007 Magazine
Estimated reading time: 3 minutes
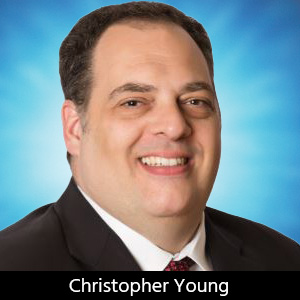
Adventures in Engineering: Connectors—The Right Fit
Connectors, the physical medium our printed circuit board assemblies (PCBAs) use to purposely interface to their external environment, can make or break your design. I have seen many designs fail due to improper connector design, selection, and usage. Most often, simple oversights were the cause of these failures due mostly to an assumption of knowledge a designer may possess. As someone who has dealt with many self-inflicted connector wounds, I would like to offer my two cents on this topic, a “Penny Primer,” if you will…
Who selects the connectors used in a PCBA design? A mechanical engineer, an electrical engineer, the system architect, the PCB designer, or do we use what worked last time? Technical consensus is a great opportunity to set the stage for selecting a connector that is the right fit for your design. An approach I have found reasonable to implement is to realize the technical consensus in the form of a list/table of selection criteria with specific items separated by their technical origin.
Table 1: Connector selection criteria.
The formality of the selection criteria depends on the processes/practices your company uses, which can range from a simple list to a worksheet that is completed and archived as prescribed by a technical instruction/process. Regardless of formality, selection criterion should be straight forward, measurable, and traceable. Now that we have our selection criteria, how do we use it? Let’s work through a couple of the items identified in Table 1.
24V Input Power
The safe operating voltage of a connector is significantly influenced by its environment. Air quality (pollution degree) and altitude directly affect the minimum creepage and clearance for a given voltage. Safety documents such as IEC 60664-1 and IEC 61010-1 can help determine appropriate creepage and clearance distances. Clearance is the shortest distance in air between two conductors and creepage is the shortest along the surface of an insulator between two conductors. Regarding creepage, the minimum distance may be increased by strategically placing bumps on the surface of the insulator between conductors. The point where the connector is installed in/onto a PCB is covered by IPC-221B. The minimum distance at the PCB includes the conductive pin pads on the PCB, which can be significantly shorter than the spacing between connector pins themselves. Consider the following example: At an altitude of less than 2000 meters, a voltage of 24 volts in a laboratory setting (pollution degree 2) has a creepage distance of 0.5 millimeters (20 mils). The same voltage in an industrial setting (pollution degree 3) has a creepage distance of 1.25 millimeters (50 mils). Please note that the increased pollution degree increased the distance requirement by a factor of 2.5. At the PCB interface, the minimum outer layer conductor distance is around 0.25mm (10 mils). IDC header and standard DSUB connectors typically have a creepage/clearance distance of around 2 millimeters and a PCB surface conductor spacing of 1 mm, which make them good first round picks for low voltage (less than 50V) applications.
1A Max Continuous Current—Power
It is important to understand that the specified current rating of a connector is most often the current carrying capacity of only a single pin at a specified ambient temperature (usually between 20–30°C). The power input and power return pins count as current carrying pins (X power pins and Y return pins = X + Y current carrying pins). A handy rule of thumb is that if 50% of the pins are carrying current, then the per pin current carrying capacity is reduced by 25%; if 100% of the pins are carrying current, then the per pin current is reduced by 40%. This deration is independent of ambient temperature and the per pin current carrying capacity is further derated as temperature increases above the specified ambient temperature. A typical low-cost IDC header connector has a current rating of 3A at around 25C. The max ambient temperature (125°C) is where the current carrying capacity is 0 amps. An ambient temperature of 85°C will cut the current carrying capacity roughly by 60% down to 1.2 amp from 3.0 amps. This should be sufficient for a supply and return current of 1 amp. Additionally, a DSUB connector has a typical current carrying rating of 5 to 6 amps which also makes it a good candidate for relatively low current applications.
The application of connector selection criteria involves a significant number of details some of which may be ambiguous or complex. It is important to understand these ambiguities or where to go if you need help. Many connector manufacturers have application notes, white papers, and technical presentations that give insight into these details; however, practical experience is usually what is needed for a deeper understanding. I suggest finding someone or a technical forum that can serve as a means of technical guidance and getting as much practice finding connectors as possible.
Chris Young is owner/lead engineer at Young Engineering Services LLC.
More Columns from Adventures in Engineering
Adventures in Engineering: A Penny Primer on PCB Design FundamentalsAdventures in Engineering: 5G Expansion and Radar Altimeters
Adventures in Engineering: Supply Chain Management
Adventures in Engineering: Data Management Not Just Checking the Boxes
Adventures in Engineering: A Purpose-Driven Prototype
Adventures in Engineering: Test Points—The Other Side
Adventures in Engineering: The Ecosystem of Autonomous Flight
Adventures in Engineering: It's Pronounced 'Tooling Holes'