-
- News
- Books
Featured Books
- pcb007 Magazine
Latest Issues
Current IssueInventing the Future with SEL
Two years after launching its state-of-the-art PCB facility, SEL shares lessons in vision, execution, and innovation, plus insights from industry icons and technology leaders shaping the future of PCB fabrication.
Sales: From Pitch to PO
From the first cold call to finally receiving that first purchase order, the July PCB007 Magazine breaks down some critical parts of the sales stack. To up your sales game, read on!
The Hole Truth: Via Integrity in an HDI World
From the drilled hole to registration across multiple sequential lamination cycles, to the quality of your copper plating, via reliability in an HDI world is becoming an ever-greater challenge. This month we look at “The Hole Truth,” from creating the “perfect” via to how you can assure via quality and reliability, the first time, every time.
- Articles
- Columns
- Links
- Media kit
||| MENU - pcb007 Magazine
Estimated reading time: 6 minutes
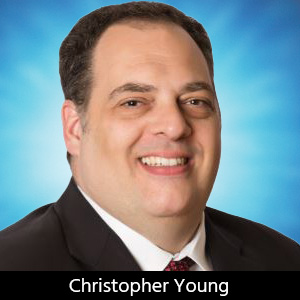
Adventures in Engineering: A Penny Primer on PCB Design Fundamentals
The prevalent mindset of late seems to be “tools maketh the designer.” I have noticed this in ECAD tool marketing, discussions with customers (past, present, prospective), and conversations with colleagues. While I am an advocate of having the right tool for the right job and possessing good tools, this should be tempered with good old-fashioned know-how. A firm understanding of PCB design (mechanical fit, electrical compatibility, producibility, and testability) is essential to developing oneself into a skilled designer. This begins with the basics; hence, I present to you a penny primer on PCB design.
A reasonable starting point is to establish physical boundaries for your specific board design, commonly known as the board outline. The board outline can be derived from mechanical outline drawings, formal requirements documentation, 2D DXF files, solid CAD models (SOLIDWORKS, NX, FUSION 360, Onshape, FreeCAD), or empirically. Once the board outline has been established, then identify where the mounting holes should be located. Mounting holes can be plated or non-plated holes that are round, slotted, square, rectangular, or ambiguous in shape. It is most common to use round or slotted mounting holes. Next, establish if you need tooling holes. Tooling holes are non-plated holes in the PCB with a tighter hole/location tolerance (+/- 0.001 inch) than typical mounting holes (0.01-0.005 inches). Tooling holes are most often used to precisely align/position the PCB in reference to an assembly, test fixture, or another PCB.
The location and quantity of tooling holes can have many dependencies and should be coordinated with PCB fabricators, PCBA assembly houses, and manufacturing/mechanical/test engineering. Identify the stakeholders and make sure you are not missing something important because mistakes with tooling holes typically cause PCB re-spins. Identify any component height restrictions or placement keep outs on the board so that the printed circuit board assembly (PCBA) will fit in the next higher assembly. To summarize, establish the board outline, mounting hole size locations, tooling hole size/locations, component height restrictions, and placement keep outs.
The next phase is working with electronic design automation (EDA) computer-aided design (CAD) tools. Many times, the specific EDA CAD tool you use for PCB design is already chosen before you start work at a specific company. Regardless of the tool (Xpedition, Cadence, Altium, PADS, CADSTAR, Eagle, KiCad, PCB123, ExpressPCB) being used, I have found it most useful to establish the physical and electrical constraints early in the design process. The many configurable PCB constraints in a PCB design are derived from electrical/mechanical requirements, PCB fabrication capabilities, PCBA assembly requirements, testing requirements, and financial objectives. Constraints like PCB trace/track width/thickness/spacing are typically determined by items like characteristic impedance, current carrying capacity, signal sensitivity, copper weight, and temperature rise of the PCB trace under load. It quickly becomes apparent that there are a lot of factors involved in establishing PCB design constraints. Someone new to PCB design should become familiar with the constraints manager/editor tool within their specific EDA CAD tool and endeavor to master it. It is well worth your time to talk with an experienced PCB designer about setting up constraints within your design. If you do not know someone firsthand, I suggest seeking out membership to organizations that are geared toward understanding PCB design and mentoring/helping PCB designers of all capabilities.
Once you have your constraints established as best as you can, items like via definitions, mounting/tooling hole definitions, PCB layer stack-ups, and trace widths can be established. Vias types (through/blind/buried) and size are typically based on the PCB area constraints, PCB total thickness (aspect ratio), and the signals (high speed/analog/RF/power) with which they are associated. Mounting holes are sized to reliably fit the mounting screws used to secure the PCBA to a metal chassis, another PCBA, heatsink, or other higher-level assembly. A PCB layer stackup determines the number of metal layers and overall thickness of a PCB. The copper layers in a PCB design most often are defined as pairs to avoid deformation (warping) during fabrication or assembly. A low to medium complexity design will typically have between two to six copper layers. Increased design complexity/compactness typically results in an increased layer count in a PCB stackup.
Figure 1: The basic anatomy of PCB stackup and the standard via types.
The copper layers within a design are assigned as planes, signals, or mixed. A plane is often used for ground/power connections, while a signal layer is used for pin-to-pin signal routing. Mixed is just a combination of the two afore mention layer types. Copper weights (ounces) or thickness (mils/mm) of copper layers are typically assigned in the layer stackup. Dielectric thickness and type are also defined in the stackup. It is a good idea to coordinate your stackup with your PCB fabricator so that you stay within their capabilities. Most PCB fabricators will publish their capabilities on their websites. After a stackup has been established, the trace widths can be determined. Trace widths are typically most dependent on current carrying capacity and characteristic impedance targets. At this point the setup work has been mostly done and it is now time to move to the next step.
Time to make hay, and by that I mean draw, place components, and route. Start by drawing the board outline and board cutouts. Most EDA CAD tools allow the board outline to be drawn using lines, primitive shapes (polygons, circles, arcs), and by importing dxf files representing the outline itself. Next, place the mounting/tooling holes and any rule areas (component placement keep outs, rooms, routing keep outs).
Component placement typically starts with connectors, followed by integrated circuits and passive components. Component placement should be done in circuit groups as defined by the electrical schematics and coordinated with electrical and mechanical designers/engineers. A connector in the wrong place or circuit components not being tightly grouped are usually grounds for a PCB respin. The electrical connections within a PCB are defined by either a schematic (preferred and intuitive) or netlist (doable but not intuitive). Vias are used so that traces can traverse routing layers or connect component pins to ground/power planes. The first stage of routing is usually fanning out vias, this is the process of placing vias near component pins to assist in multi-layer routing. Based on the layer stackup, routing constraints (trace width/spacing/layer assignment), and electrical requirements, the routing can be done point to point free hand, semi-automated, or fully auto-routed.
Based on the type of electrical signals, routing can be single ended or differential (pair or parallel traces). Routing methodologies employed by the designer depend on the routing layer configuration (microstrip, stripline, dual stripline, asymmetrical stripline, and co-planer wave to name a few). For example, a designer may decide to employ a north/south, east/west routing strategy on a dual stripline configuration. When the designer is done with drawing, placement, and routing, the next step is the design rule check (DRC). The DRC is used to verify that the design adheres to the constraints established in the beginning of the design. A DRC check will produce a list of “violations” that should be addressed before fabrication and assembly data packages are created.
The process of designing a PCB is like solving a Rubik's cube. Establish a reasonable starting point, then algorithmically solve the cube until all sides are the same color. Just like a Rubik’s cube, there are many approaches to PCB design that will work, and it is up to you to figure out which algorithms work best for a given design. What also should be noticeable at this point is there are many aspects to PCB design, many are inter-related, and not all of them have been covered in this primer. Many EDA CAD software applications have internal tools to help sort out and organize these many details. A very handy third-party tool I use frequently is the PCB Toolkit provided freely by Saturn PCB Design Inc. It is EDA CAD platform independent and serves as a good technical reference as well as a functional glossary of PCB design terminology with references to IPC specifications. I also suggest learning about design for manufacturing (DFM), design for assembly (DFA), and design for test (DFT) and integrating these concepts into your design practice.
Chris Young is owner/lead engineer at Young Engineering Services LLC.
More Columns from Adventures in Engineering
Adventures in Engineering: 5G Expansion and Radar AltimetersAdventures in Engineering: Supply Chain Management
Adventures in Engineering: Data Management Not Just Checking the Boxes
Adventures in Engineering: Connectors—The Right Fit
Adventures in Engineering: A Purpose-Driven Prototype
Adventures in Engineering: Test Points—The Other Side
Adventures in Engineering: The Ecosystem of Autonomous Flight
Adventures in Engineering: It's Pronounced 'Tooling Holes'