-
- News
- Books
Featured Books
- pcb007 Magazine
Latest Issues
Current IssueInventing the Future with SEL
Two years after launching its state-of-the-art PCB facility, SEL shares lessons in vision, execution, and innovation, plus insights from industry icons and technology leaders shaping the future of PCB fabrication.
Sales: From Pitch to PO
From the first cold call to finally receiving that first purchase order, the July PCB007 Magazine breaks down some critical parts of the sales stack. To up your sales game, read on!
The Hole Truth: Via Integrity in an HDI World
From the drilled hole to registration across multiple sequential lamination cycles, to the quality of your copper plating, via reliability in an HDI world is becoming an ever-greater challenge. This month we look at “The Hole Truth,” from creating the “perfect” via to how you can assure via quality and reliability, the first time, every time.
- Articles
- Columns
- Links
- Media kit
||| MENU - pcb007 Magazine
Estimated reading time: 4 minutes
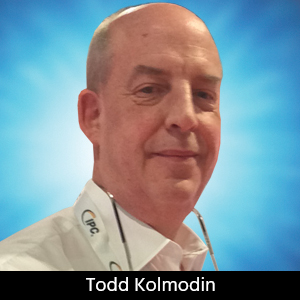
Testing Todd: Meet Mr. Henry and Do Not Blow a Fuse
Volts, amperes, and ohms: in electrical test, these terms are very familiar. Combinations of these electrical elements make up the standard electrical test of the average PCB. Standard electrical test uses the IPC specification 9252 as a baseline. Depending on the performance class, different parameters are used to screen the board. There are many machines out there that can perform these basic tests, and this has been the way of life for decades.
However, life changes. These design guys and gals do not stop the train of evolution. Packages become smaller, PCBs become smaller, and newer electrical characteristics come in to play. Now we must deal with farads and Mr. Henry—after Joseph Henry. See what I did there?
Today, new requirements bring buried capacitance and inductance. Although today’s flying probe machines are familiar with capacitance via the indirect test and capacitive discharge analysis, direct measurement of the actual values become more challenging. If the design drawing is provided and locations for direct capacitive measurements are given (with values), the machines of today can provide this test much akin to buried resistance.
However, inductance becomes more of a challenge. Most fixture testers are ill-equipped to test anything other than the standard ET parameters using volts, amps, and ohms. Mr. Henry introduces a variable that these metering systems simply cannot measure. Buried or active inductance is not anything new to PCBs but the ability to properly measure the inductance is. In the past, simple primary and secondary passive coils are laid out in a PCB resembling nested circles or blocks. Resistance of the primary and secondary circuits can easily be measured but if there is a short in either the primary or secondary circuits to itself (remembering the circular patterns) the change of resistance in the primary or secondary circuit within itself is not large enough to cause a continuity failure.
Therefore, the actual inductance of the coil should be measured to ensure a breakdown of the primary, secondary, or both is not present. Some newer flying probes have developed software modules that can measure this inductance. Just like buried resistance, the inductance (in Henry’s) is pre-programmed within the netlist and the flying probe measures the inductance of the coil circuit just like any other network. However, this does require an upgraded metering system beyond the standard out-of-box configuration. If you are interested in automated inductance testing, consult your preferred equipment vendor, and discuss what options may be available to you.
Another caveat of the electrical test arena is the presence of high-resistance shorts, sometimes referred to as high-Z or micro-shorts. The problem these phenomena bring to detection is that they can be present momentarily at the time of test but due to current flow of the test machine being used, they can “blow” like a fuse. Although electrical testers use a minimum of current flow during test, these micro-shorts can be extremely small, like slivers or whiskers. It takes a minimum of current to blow them open. A technician may attempt to verify the short reported, only to find that it has disappeared, and the retest of the PCB will pass. Unfortunately, a ticking time-bomb remains. The board now passed and moves on to assembly and finally into service. However, deep inside the board a process called electro-chemical migration may be taking place. Due to the internal burn of the “blown fuse,” there are burn deposits left behind. Over time, this process can migrate metal ions from one electrode to the other—in this case between the once shorted tracks or traces. In the worst case, this can cause an electrical path to return and a high resistance short may reappear. This can cause the final product to have degraded functionality in the field or fail altogether.
To combat this, extremely low current should be applied to the circuits while still having the ability to detect the high resistance short. Many times, these shorts will register well above the standard ET parameter for isolation such as 10 or 20 megohm. Using a “micro-short” algorithm some test machines can identify these defects without destroying them. Keeping the current to the lowest possible limit while still looking for the high resistance fault is the key. Using standard methodology, the current may exceed the resistance threshold of the short and it heats up and finally burns. This can happen almost immediately so this test should be done prior to standard ET screening. That way the micro-shorts will be identified immediately before higher current is applied.
Doing a micro-short test after standard ET defeats the purpose of the test, as any damage may have already occurred. One must also remember that these shorts can exhibit very high resistance and a standard “off the shelf” ohmmeter may not have the resolution to verify the high resistance present. So, in micro-short detection one must not assume the defect is fake because an ohmmeter does not detect it. If you don’t have the correct verification equipment, retest the board. If it fails again, believe the machine, fail the board, and have it examined. Second guessing a fault such as this only results in disaster.
Be safe!
This column originally appeared in the June 2021 issue of PCB007 Magazine.
More Columns from Testing Todd
Testing Todd: Why 4-wire Kelvin?Testing Todd: Why TDR?
Testing Todd: Positivity Boosts Employee Morale
Testing Todd: Preparing Employees for the Long Haul
Testing Todd: Where Can We Improve?
Testing Todd: Turning Into the Wind
Testing Todd: Coming Back to Life—Design Recovery
Testing Todd: Decision Time—Invest or Delegate?