-
- News
- Books
Featured Books
- pcb007 Magazine
Latest Issues
Current IssueSales: From Pitch to PO
From the first cold call to finally receiving that first purchase order, the July PCB007 Magazine breaks down some critical parts of the sales stack. To up your sales game, read on!
The Hole Truth: Via Integrity in an HDI World
From the drilled hole to registration across multiple sequential lamination cycles, to the quality of your copper plating, via reliability in an HDI world is becoming an ever-greater challenge. This month we look at “The Hole Truth,” from creating the “perfect” via to how you can assure via quality and reliability, the first time, every time.
In Pursuit of Perfection: Defect Reduction
For bare PCB board fabrication, defect reduction is a critical aspect of a company's bottom line profitability. In this issue, we examine how imaging, etching, and plating processes can provide information and insight into reducing defects and increasing yields.
- Articles
- Columns
- Links
- Media kit
||| MENU - pcb007 Magazine
Estimated reading time: 4 minutes
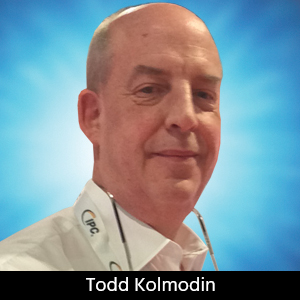
Testing Todd: The PCB Limbo—How Low Can You Go?
Welcome to the grand illusion. There I was, mid-1986, and in my first job with printed circuits. I knew what circuit boards were but had no idea about all the processes involved in their manufacture and test. Here in the Pacific Northwest, there were probably two dozen PCB manufacturers producing everything from double-sided to 16-layer stacks. All were PTH-only at the time. Surface mount technology was not to make its debut for a year or two.
Fixture testers were 100-mil grids (0.100”) and there were no such things as double-sided testers. What? There was no need at this point as SMT was not active. Test fixture manufacture was simple. You could either use the production drill file or alter the tool sizes for the test pins and drill. Once complete you could lay the plate over film and X-out the vias. Or you could digitize the outer layer and optimize mid-points and vias. Either way, you would then assemble the fixture and it was ready for the tester. There were no netlists back then, only self-learn or “golden board” learn.
As time progressed, SMT appeared on the scene and changed everything. Technology had evolved, and the PCB industry had to react to new equipment, processes, and ways to manufacture. ET had to evolve as well, such as with double-sided fixtures for single sided testers, and spring probes and wires translating the top-side fixture down through the bottom to the test field. This was expensive. However, the industry was booming on into the 1990s and life was good.
Everyone was enjoying the returns and competition was flourishing. Competition in an open market is good as long as margins remain safe and technology continues to advance. However, something went very, very wrong.
In the late ‘90s, the industry started to pull back. Demand dropped with the tightening economy. The supply of manufacturers outweighed the demand, and the wars broke out. It became a consumer’s market. Customers threatened to take business to other suppliers who offered discounted pricing. It was then that supplier XYZ would cave in and match the price. This is when the dominos started to fall.
As with any business, there are fixed costs: building/land, utilities, insurance, and taxes. These do not change, and in many cases some of them increase over time. Continuous pressure to reduce costs from the manufacturer started a practice of taking losses, in some cases, just to keep the business running. This worked somewhat during this time as margins could be made up on quick-turn or high-demand orders. The problem was that there was no lower control limit to stop the fall. This practice continued until smaller shops began to disappear, either crushed by the price-cutting competition or unable to keep up with the fast-changing technology with no margin to expand or upgrade.
Printed circuits are the building blocks to almost everything today. Even your toaster has one. The costs of production have not changed significantly. The same basic concepts still must be used to produce them. Yes, there have been efficiency enhancements and automation to lower production time, but these have also required capital investments requiring depreciation over time. The cost is fixed, yet the buyers and customers still demand price cutting. No one ever put the flag in the sand saying “enough.” Margins continued to decrease and what was a strong diverse group of manufacturers in the Pacific Northwest no longer remains. They are gone, stamped out or purchased by the mega-manufacturers. Making matters worse is the outsourcing offshore where certain variables have been manipulated or compromised to reduce cost.
The problem is that now customers do not have a vast selection of manufacturing vendors to choose from. The much smaller arena of manufacturers still fight for the business and still compete against the mega-manufacturers. Some find a niche and can continue to thrive, but others are finding the end to a dream.
Now, throw in a pandemic and the workforce disappears, or shops are forced to close due to cases of infection. The government kicks in and helps those in need but overlooked the scenario that the help was providing higher wages than minimum for the jobs that needed filling. Now the manufacturers are in trouble as they cannot find workers for their paid wage scale. Human nature is keeping workers away as they are financially better off staying home.
How low does this bar go? Had someone kept an eye on the downward spiral the industry may have stayed buoyant. However, it did not happen and now margins are at a bare minimum and mostly below healthy model limits. Since fixed costs could not be adjusted, wages and employee counts were the variable that had to be adjusted. The industry is no longer appealing to the college graduates as future projections are unstable and personal growth is limited in many aspects. Another economical problem is now we are down to a supplier pool approaching a monopolization. This “eggs in one basket” approach is dangerous for obvious reasons. If those suppliers fail or have extended production interruptions, it will cause an immediate supply chain crisis.
How to recover in this industry to make it stable will be a challenge. Unless mindsets and models change, this “limbo bar” will stay where it is and hopefully not go any lower.
This column originally appeared in the July 2021 issue of PCB007 Magazine.
More Columns from Testing Todd
Testing Todd: Why 4-wire Kelvin?Testing Todd: Why TDR?
Testing Todd: Positivity Boosts Employee Morale
Testing Todd: Preparing Employees for the Long Haul
Testing Todd: Where Can We Improve?
Testing Todd: Turning Into the Wind
Testing Todd: Coming Back to Life—Design Recovery
Testing Todd: Decision Time—Invest or Delegate?