-
- News
- Books
Featured Books
- pcb007 Magazine
Latest Issues
Current IssueIn Pursuit of Perfection: Defect Reduction
For bare PCB board fabrication, defect reduction is a critical aspect of a company's bottom line profitability. In this issue, we examine how imaging, etching, and plating processes can provide information and insight into reducing defects and increasing yields.
Voices of the Industry
We take the pulse of the PCB industry by sharing insights from leading fabricators and suppliers in this month's issue. We've gathered their thoughts on the new U.S. administration, spending, the war in Ukraine, and their most pressing needs. It’s an eye-opening and enlightening look behind the curtain.
The Essential Guide to Surface Finishes
We go back to basics this month with a recount of a little history, and look forward to addressing the many challenges that high density, high frequency, adhesion, SI, and corrosion concerns for harsh environments bring to the fore. We compare and contrast surface finishes by type and application, take a hard look at the many iterations of gold plating, and address palladium as a surface finish.
- Articles
- Columns
Search Console
- Links
- Media kit
||| MENU - pcb007 Magazine
Estimated reading time: 3 minutes
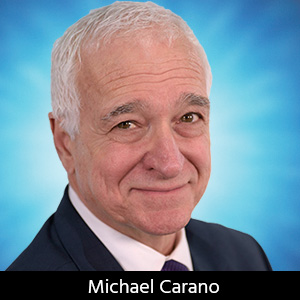
Contact Columnist Form
Trouble in Your Tank: A Series of Questions on Price Increases
Editor’s note: This special installment of Michael Carano’s long-running column is excerpted from a Q and A session held by the I-Connect007 staff.
Q: Happy Holden points out that direct metalization (DM) is more efficient, and more cost-effective than electroless. Is this the time to migrate?
Carano: DM has been around for 25 years. It is more efficient, easy to provide in a continuous horizontal fashion, and is environmentally friendly. Asia is way ahead of North America. We are starting to convince companies that DM is ideal for flex and HDI fabrication. Asia already understands this.
Q: What are the challenges right now?
Carano: There are several—supply chain disruptions, price increases, low yields from the fabricator’s standpoint, and an inadequately trained workforce, as well as aging or inadequate equipment needed to build high yield/higher technology product. The money will be made in higher yields and more complex circuit boards.
Q: What’s new about those challenges?
Carano: Mainly, the environment post-COVID is more challenging due to lack of ability to onboard workers; many line workers, so to speak, are poorly trained, and offered $12-$13 per hour. Really? My neighborhood McDonald’s is offering $15-$16 per hour plus other enticements. Amazon is offering $22-$25 per hour plus benefits. No wonder the PWB fabricators can’t find reliable employees. There’s also a lack of government support for the PWB industry. They only see semiconductors as sexy, not recognizing that without a reliable board, the chips have nowhere to go.
Q: What do you anticipate for the next two years?
Carano: Without an awakening of our elected officials, the PWB footprint in North America will erode. The bigger firms (TTM, FTG, Summit Interconnect, Advanced Circuits) will find distressed fabs and acquire them as they have been doing.
Q: What are your thoughts on recent comments from Dan Feinberg that price increases for the seller are cost increases for the buyer? Is this a good time to optimize processes to minimize your price increases?
Carano: I am a firm believer in process optimization, enhanced troubleshooting skills, use of statistical tools, training, and engineering. One should not wait to “optimize” processes. Optimization requires focus, commitment, and investment. Things as simple as automating the analytical procedures for the processes, training and certifications through IPC Training Programs (much of the training modules can be taken online and on demand through the IPC Edge portal). Yes, most of the fabricators and assembly firms are not taking advantage of these offerings. Why? So much can be learned. Knowledge is power.
Q: How do folks down the chain from you mitigate the risk?
Carano: If possible, strike deals for material/chemistry supply with contracts. Also, lock in technical service from the supplier; however, that means paying a premium. The fabricators, instead of trying to beat down your price, should select the chemical material supplier on several other criteria:
- Innovation track record
- On-site tech support
- Being a partner with the supplier—to ensure steady flow of new ideas, best practices, analytical services
Q: Is this situation driving new product? Or is this situation causing a scaling back of product development?
Carano: We don’t scale back product development; most of our competitors don’t either. We continue to invest. That is the only way to help fabricators jump the technology curve. However, the fabricators need to change their way of thinking. We need to push the envelope a bit and invest in new technology and training/certifications. Process control, in many instances, is lacking or sub-standard.
This column originally appeared in the July 2021 issues of PCB007 Magazine.
More Columns from Trouble in Your Tank
Trouble in Your Tank: Yield Improvement and ReliabilityTrouble in Your Tank: Causes of Plating Voids, Pre-electroless Copper
Trouble in Your Tank: Organic Addition Agents in Electrolytic Copper Plating
Trouble in Your Tank: Interconnect Defect—The Three Degrees of Separation
Trouble in Your Tank: Things You Can Do for Better Wet Process Control
Trouble in Your Tank: Processes to Support IC Substrates and Advanced Packaging, Part 5
Trouble in Your Tank: Materials for PWB Fabrication—Drillability and Metallization
Trouble in Your Tank: Supporting IC Substrates and Advanced Packaging, Part 5