-
- News
- Books
Featured Books
- pcb007 Magazine
Latest Issues
Current IssueSales: From Pitch to PO
From the first cold call to finally receiving that first purchase order, the July PCB007 Magazine breaks down some critical parts of the sales stack. To up your sales game, read on!
The Hole Truth: Via Integrity in an HDI World
From the drilled hole to registration across multiple sequential lamination cycles, to the quality of your copper plating, via reliability in an HDI world is becoming an ever-greater challenge. This month we look at “The Hole Truth,” from creating the “perfect” via to how you can assure via quality and reliability, the first time, every time.
In Pursuit of Perfection: Defect Reduction
For bare PCB board fabrication, defect reduction is a critical aspect of a company's bottom line profitability. In this issue, we examine how imaging, etching, and plating processes can provide information and insight into reducing defects and increasing yields.
- Articles
- Columns
- Links
- Media kit
||| MENU - pcb007 Magazine
Estimated reading time: 4 minutes
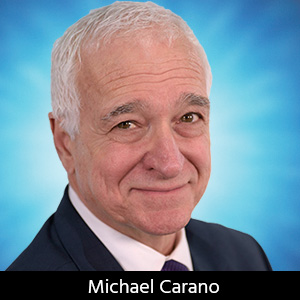
Contact Columnist Form
Trouble in Your Tank: Case Study—Interconnect Defects and a Few Other Problems
Introduction
Over the past 18 years or so, my columns have focused on presenting a specific defect or defects, drilling down to the root causation of the defect, and quickly and efficiently identifying and subsequently eliminating the cause. For this month’s edition, we are taking a slightly different approach—that of presenting an actual case study. However, the basic principles of these columns continue.
The Issue
The situation involves a large and well-equipped printed circuit board fabricator. The company had received returns for what was viewed as Type 1 ICDs; the electroless copper was pulling away from the interconnect. As is so often the case with defects, the non-conformance was only detected on a few panels. There was no correlation to the part design. All panels exhibiting the problem were multilayers, either 10 or 12 layers, with standard FR-4 construction. Microsectional analysis showed the problem (Figure 1).
The desmear/etchback was deemed sufficient. With such a degree of etchback, no smear should have remained.
So, what was the cause of this issue? Again, the defect was only seen on a few isolated occasions. Further examination of sections after plating showed some interesting anomalies.
Figure 2 shows a closer view of the interconnect. Looking closely at the section, one can see debris on the face of the interconnect. Clearly, the debris is the major reason why the electroless is not making contact with the innerlayer. Looking at sections of these panels under SEM yields additional information (Figure 3). Here, one can see the debris in the hole and detrimental effects.
Initially, the team considered that the electroless copper itself (plating rates, overall stability, etc.) was the primary cause. And with the detection of some sort of debris, there was a high probability that the source of the debris may have originated with the electroless copper solution itself. The question is: Where did the debris originate? Certainly, there are several potential sources for insoluble material to lodge onto the hole wall or interconnect.
Insoluble materials and particulate matter accumulate over time from various sources. This includes drag-in of chemicals from previous process steps that lead to formation of insoluable particles. Solutions—including the catalyst or the electroless copper solution itself—are a main source of insoluble matter. One should maintain filtration on the catalyst and electroless copper solutions at the very least. Palladium drag-in to the electroless copper tank will destabilize the process solution. The palladium (part of the electroless copper catalyst) drag-in will lead to copper dusting. This dusting, or literally the formation of copper metallic particles, will cause deposit roughness. Figure 4 shows a simple overflow weir. This set-up helps greatly to remove particulates and other materials that can cause rapid plate-out or roughness/blisters.
Another source of debris is introduced from the drilling process. Drill debris entrapment is a major source of particulate matter. One of the causes of the debris is from drilling too deep into the back-up material. One only needs less than one drill bit diameter turn into the back-up material. Over-penetration into the back-up material leads to additional debris introduced into the vias and the potential for drill bit breakage. Poor quality back-up material will contaminate the via as well. Most fabricators have opted for aluminum-clad back-up materials. Although more expensive than the phenolic materials, the aluminum clad will not contaminate the holes.
The vacuum system on the drilling machine is a very important facet in drilling vias. The vacuum cleans the drill bit flutes of chips and glass debris on each stroke. Low vacuum power will result in the chips and debris remaining in the via, thus adversely affecting the quality of the plating operation. Follow the drill equipment supplier’s guidelines on proper vacuum operation.
In addition, inspect the drill area for dust. This could indicate there is static electricity in the room, allowing drill debris to settle on the equipment.
A Few Caveats
Debris issues aside, blistering or flaking of the electroless copper from the surface or in the holes can be attributed to the following:
- Electroless copper process chemistry is out of balance. Adjust the components into the proper operating ranges and ensure that the controllers are maintaining the solution components at the proper feed rate.
- Depending on solution loading (square feet of board per gallon of electroless copper solution), the reducing agent level (formaldehyde) may increase in concentration. This can cause the solution to become overactive and result in the flaking or blistering problem.
- Primary stabilizer in the electroless copper solution is low, leading to an overactive solution; deposition rate is higher than normal leading to blisters or flaking.
- Plating racks with loosely adherent copper deposits can cause these defects. Regularly strip the plating rack to remove these deposits; the rack should be clean of copper before each plating cycle (Figure 5). Copper flaking from racks can destabilize the solution, causing rapid plate-out and rough copper deposits.
- Monitor the specific gravity of the operating electroless copper process. Maintain the specific gravity at or below the supplier’s stated recommendation; high specific gravity is an indication that the process may be overactive.
- Process control: Regular replenishment additions based on square footage processes is ideal. A simple single-channel controller to monitor the copper content of the solution works efficiently. Other components are metered in according to pre-set pump settings. Do not wait to make large manual additions on an irregular basis.
Remember that the genesis of a defect or anomaly is not readily evident within a particular process or operation. The root cause may have multiple contributors. Be sure to look closely at the processes that may contribute to the defect.
This column originally appeared in the September 2021 issue of PCB007 Magazine.
More Columns from Trouble in Your Tank
Trouble in Your Tank: Can You Drill the Perfect Hole?Trouble in Your Tank: Yield Improvement and Reliability
Trouble in Your Tank: Causes of Plating Voids, Pre-electroless Copper
Trouble in Your Tank: Organic Addition Agents in Electrolytic Copper Plating
Trouble in Your Tank: Interconnect Defect—The Three Degrees of Separation
Trouble in Your Tank: Things You Can Do for Better Wet Process Control
Trouble in Your Tank: Processes to Support IC Substrates and Advanced Packaging, Part 5
Trouble in Your Tank: Materials for PWB Fabrication—Drillability and Metallization