-
- News
- Books
Featured Books
- smt007 Magazine
Latest Issues
Current IssueWhat's Your Sweet Spot?
Are you in a niche that’s growing or shrinking? Is it time to reassess and refocus? We spotlight companies thriving by redefining or reinforcing their niche. What are their insights?
Moving Forward With Confidence
In this issue, we focus on sales and quoting, workforce training, new IPC leadership in the U.S. and Canada, the effects of tariffs, CFX standards, and much more—all designed to provide perspective as you move through the cloud bank of today's shifting economic market.
Intelligent Test and Inspection
Are you ready to explore the cutting-edge advancements shaping the electronics manufacturing industry? The May 2025 issue of SMT007 Magazine is packed with insights, innovations, and expert perspectives that you won’t want to miss.
- Articles
- Columns
- Links
- Media kit
||| MENU - smt007 Magazine
Perfecting the Application of Conformal Coatings Without a Capital Investment
November 1, 2021 | Zsolt Pulai, HZO, Inc.Estimated reading time: 3 minutes
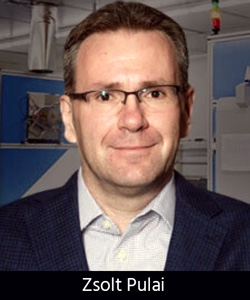
Printed circuit boards (PCBs) are marvels of science and one of the most disruptive innovations of the last 100 years. Since inception, they have undergone numerous alterations, improvements, and transformations with the most profound being driven by the miniaturization of electronics. PCB manufacturers are being pushed to create smaller and more densely packed boards with increased electronic capabilities. As amazing as they are, their Achilles heel is contamination. In this article, we will review the history and applications for thin-film conformal coatings, and introduce a new service for conformal coating application, potentially adding coating capability without adding capital investment.
Background
Sensitive circuitry is affected by harsh environments. Extreme temperatures, dust, dirt, chemical vapors, and moisture from humidity, rain, and snow can have a detrimental effect on PCB health, thereby putting their end products at risk of seizing and performance breakdowns.
Thin-film conformal coatings have a solid position as the protective coating of choice for protecting PCBs from external factors in operating environments. They provide a protective barrier or film, layered over the critical substrates. When applied accurately, conformal coatings prevent sources of moisture, vapors, and other contaminants from damaging or corroding interior circuitry.
There are five types of conformal coating available on the market today: parylene, acrylic, silicone, polyurethane, and epoxy. They each possess a unique set of characteristics and properties. Of these, parylene is often considered the protective coating of choice for a PCB’s challenging applications.
Research chemist Michael Szwarc isolated the parylene polymer series in the late 1940s at the University of Manchester, England. He discovered the polymer as one of the thermal decomposition products of a common solvent, p-xylene, at a temperature between 700 and 900°C. Union Carbide scientist William Gorham later developed a deposition process to apply the film. He deposited parylene films by the thermal decomposition of di-p-xylylene at 550°C and in vacuum below 1 Torr, a process that did not require a solvent and resulted in chemically resistant films free from pinholes. In 1965, Union Carbide commercialized the material and the chemical vapor deposition (CVD) process that is unique among conformal coatings.
While the barrier properties of parylene are unmatched, it adds minimal mass to coated surfaces and contributes no cure or thermal expansion forces to threaten delicate components. Parylene has exceptional tensile and yield strength, is dielectric, and can cover the entire board to protect component leads, solder joints, exposed traces, and other metalized areas. It provides protection from corrosion, and shields the whole PCB from spray, moisture, fungus, dust, and other contaminations from harsh environments. Parylene even helps prevent damage to circuitry and sensitive components from thermal and mechanical stress as well as rough handling, or in the case of AMRs, bumps, and jarring during deployment.
Parylene conformal coatings consist of a protective polymer layer 12–25 µm thick (<20 µm typical) that conforms to a PCB’s shape and components. They provide resistance to solvents and chemicals, are heat resistant, and help prevent light component leakage and corrosion. They are the best protective strategy for PCBs that will be exposed to unfavorable environments.
The impediments to parylene's wide adoption have been cost and scalability. The raw materials have been historically high-priced, and scalability with manufacturing integration is complex. HZO has broadened the scale of usage for this robust, organic material by making it available to companies and manufacturers that could not previously consider it an option. At the foundation of its offerings are engineers and scientists with deep domain and industry expertise in conformal coatings, and its in-house proprietary equipment.
Although there are different ways to apply coatings—brushing, spraying, dispensing, and dipping—HZO uses the chemical vapor deposition (CVD) process to create truly uniform conformal coatings. CVD is a coating method that flows reactive gases into a vacuum chamber containing the target substrates, where the chemistries combine or react to form a conformal coating. In HZO's case, these reactive constituents are formed thermally, but the reactions on the product happen at room temperature.
HZO’s optimized chamber size and shape ensures uniform parylene deposition and a proprietary state-of-the-art controller that can remotely monitor and control real-time critical factors, like temperature, pressure, and other essential operating parameters.
The precision and control of its systems extend the use of parylene to more consumer electronics, medical devices, IoT, industrial, and automotive applications by meeting tighter tolerance, thinner film depositions, and higher quality standards. HZO’s equipment employs a proven application method for both small batch and high-throughput environments. Semiconductors, printed circuit board assemblies, subassemblies, and devices are placed inside the equipment's chamber where a protective coating is applied as a vapor, forming the protective conformal coating, measuring thinner than a human hair.
To read this entire article, which appeared in the October 2021 issue of SMT007 Magazine, click here.