-
- News
- Books
Featured Books
- design007 Magazine
Latest Issues
Current IssueDesigning Through the Noise
Our experts discuss the constantly evolving world of RF design, including the many tradeoffs, material considerations, and design tips and techniques that designers and design engineers need to know to succeed in this high-frequency realm.
Learning to Speak ‘Fab’
Our expert contributors clear up many of the miscommunication problems between PCB designers and their fab and assembly stakeholders. As you will see, a little extra planning early in the design cycle can go a long way toward maintaining open lines of communication with the fab and assembly folks.
Training New Designers
Where will we find the next generation of PCB designers and design engineers? Once we locate them, how will we train and educate them? What will PCB designers of the future need to master to deal with tomorrow’s technology?
- Articles
- Columns
Search Console
- Links
- Media kit
||| MENU - design007 Magazine
Polar Instruments: Pandemic and Parts Shortage Lead to More R&D Time
November 2, 2021 | Nolan Johnson, I-Connect007Estimated reading time: 4 minutes
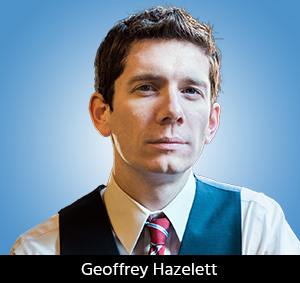
During PCB West, I met with Geoffrey Hazelett, VP of sales for Polar Instruments. He explained how the pandemic actually helped Polar’s R&D in the long run, and why the current parts shortages may offer a similar benefit for OEMs, who can now spend more time in what he calls “forced R&D.”
Nolan Johnson: Geoffrey, thanks for meeting with us.
Geoffrey Hazelett: Thank you. Good to see you, Nolan.
Johnson: What’s new?
Hazelett: Well, a lot of things have changed in the last year and a half. COVID has actually provided us an opportunity and for our engineers to really buckle down, and due to some efforts that they’d already put in place, we’ve been able to release a lot more iterations of our software. So instead of once a year, we’re getting three or four, and sometimes five releases of the software a year. And these aren’t just bug fixes and whatnot. We’re talking feature updates, adding new things, and enabling new capabilities.
Tomorrow, I’ll be speaking at the PCB West Lunch-N-Learn, sponsored by Polar Instruments, about how to perform more advanced what-if analysis. Let’s take an environment where you’re looking at a 100-ohm differential pair, and you say, “As I change the dimensions of these traces, make them narrower, closer together, very tightly coupled, and all the way to extremely wide, really far apart, what does the insertion loss look like on that?”
Well, just by going through all of the steps within the tool, I can very quickly and easily figure out what I want my common-mode impedance to be. And this is especially useful if you want a specific insertion loss target, because now you’ll know the dimensions that you need to save for the layout of the traces in order to get that without needing to change all of the laminates and cores.
Being able to do that, as a fabricator, you can then tell the designer, “You can do this, but these will be the dimensions we need to do to make that happen.” We’ve also added goal-seeking for copper roughness values. So if the fabricator might not know what copper roughness values to put into the field solver, they can back-calculate it, goal-seeking for that value. Regardless of what the physical measurement might say it is, then you have the practical electrical measurement. Then the next time when they’re making a board in that same design configuration, they can really hammer that right in and say, “This is what the insertion loss is going to be.” And our customers who’ve used that so far have been extremely satisfied.
Johnson: That’s great.
Hazelett: I’m excited about that stuff because our customers have asking about it for a while. And because some of those changes were made on the back end, we’re able to put some of these features in much more quickly, than we have in the past.
Johnson: Coming out of all of this, has there been a chance to really get some R&D momentum going? Do you see that carrying on as we slowly start to return to normal?
Hazelett: Well, what’s normal these days in the tech industry? We didn’t slow down. There was no slowdown; there was a ramp up. I remember trying to buy a webcam last year from Logitech or whoever, and the MSRP for it was $100, but it cost $250. And my customers are still going through the silicon shortage. They have the printed circuit boards, but they don’t have the chips to populate them with. So then it’s giving them some additional time, in some cases, to re-engineer and do multiple steps of engineering without actually going through the process of deploying something.
So I’m going to think on the consumer side, for us everyday people, we’re going to see a lot more jumps and leaps in advanced technology for consumers, as well as the industry, because we’re being given that additional kind of forced R&D time. That hasn’t necessarily always been the case when people are grabbing everything off the shelf, ready to go with whatever’s the latest and greatest. But if you force that engineering cycle again, you get better stuff coming out than we could before, both on our side and the consumer side.
Johnson: That’s an interesting insight: You can actually leverage some of these supply chain long lead-time issues to refine your design, to make a better, higher yield, higher performance, and lower cost.
Hazelett: Hopefully.
Johnson: Yeah, hopefully. And that’s an interesting perspective. That’s great. Thanks for sharing the time with us here.
Hazelett: Thank you.
Check out this additional content from Polar:
- The Printed Circuit Designer’s Guide to… Secrets of High-Speed PCBs, Part 1 by Martyn Gaudion (a free eBook available for download)
- The Printed Circuit Designer’s Guide to… Secrets of High-Speed PCBs, Part 2 by Martyn Gaudion (a free eBook available for download)
- You can also view other titles in our full I-007e Book library here