-
- News
- Books
Featured Books
- design007 Magazine
Latest Issues
Current IssueRules of Thumb
This month, we delve into rules of thumb—which ones work, which ones should be avoided. Rules of thumb are everywhere, but there may be hundreds of rules of thumb for PCB design. How do we separate the wheat from the chaff, so to speak?
Partial HDI
Our expert contributors provide a complete, detailed view of partial HDI this month. Most experienced PCB designers can start using this approach right away, but you need to know these tips, tricks and techniques first.
Silicon to Systems: From Soup to Nuts
This month, we asked our expert contributors to weigh in on silicon to systems—what it means to PCB designers and design engineers, EDA companies, and the rest of the PCB supply chain... from soup to nuts.
- Articles
- Columns
Search Console
- Links
- Media kit
||| MENU - design007 Magazine
Dan Beeker: Follow the Geometry and Control the EM Fields
November 4, 2021 | Andy Shaughnessy, I-Connect007Estimated reading time: 13 minutes
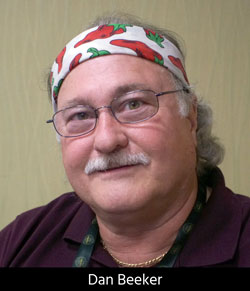
Senior principal engineer Dan Beeker of NXP Semiconductor became something of an industry rock star a few years ago with his remake of the Meghan Trainor song “All About That Bass.” With “All About the Space,” Dan had his class attendees humming a tune that reminded them that signals travel in the spaces around the traces, not the traces themselves.
Now, Dan is on a mission to spread the gospel of the late Ralph Morrison, who spent much of his career writing and teaching about electromagnetic field theory. In this DesignCon interview, Dan explains why the PCB design community needs to embrace Morrison’s teachings, which he believes could save the industry hundreds of millions of dollars in respins.
Andy Shaughnessy: Dan, how are you doing? Long time, no travel.
Dan Beeker: I’m all right. This is my 41st year with Motorola Freescale NXP, by the way.
Shaughnessy: That’s great. Why don’t you tell us about what you’re presenting at the show?
Beeker: I’ve been lucky enough to teach five sessions here. The focus is on what I learned from the teachings of Ralph Morrison about electromagnetic fields, their behavior, and what it takes to control these fields, so they do the work that you need them to do. Ralph always said, “Buildings have walls and halls. People travel in the halls, not the walls. Circuits have traces and spaces. Energy and signals travel in the spaces, not the traces.”
The signals travel in the spaces, not the traces, but the long-time focus for the industry has been on the idea of current flowing in the wires in a loop. When you use that as your design philosophy, as the IC geometries have continued to get smaller and smaller, and the switching speeds are going faster and faster, things don’t work anymore. It’s because the energy is not electrons traveling in the wires. It’s being carried by electromagnetic fields in the space between the wires. Using that perspective is what it takes to change a design from a disaster to success; you focus on the dielectric, the plumbing for the energy.
Shaughnessy: Ken Wyatt told us that most designers were taught that it’s all in the traces. It’s almost counterintuitive to think that it’s not.
Beeker: We were always taught about electron and hole flow. Well, that does occur, but it’s a result of the electromagnetic field moving through the space and interacting with the surface of the crystal lattice of the conductor as it moves through that space. The problem is that the whole thing was set up by a diagram that everybody’s seen: You have a battery on one side, and there’s a line drawn to a switch and from the switch to a light and from the light back to the battery. There are arrows going one way at the top and arrows going the other way at the bottom. So there is some of that happening, but the real energy is moving through the space between the wires from the battery to the light bulb, where it’s then consumed.
The industry slowly changed from very large geometry transistors in the TTL days into smaller and smaller geometries. It wasn’t an instant change: There was an application here, an application there, and we slowly started to see an increasing number of EMC test failures, and nobody seemed to understand it.
I moved to Detroit in 1987 when the conversion was happening from HMOS to HCMOS. At that point, the marketing pitch was, “Use these new parts. They’re faster, smaller, and cheaper.” Every module failed, and trying to fix this problem was a real challenge because it was truly black magic to everybody at that point. I would sit with my customers next to the test chamber, and we would make a cut here and solder a capacitor there and retest it and hope that it would make a difference. We did this until we finally came upon the magic combination that seemed to cause the module to pass EMC now, but with no idea of what the impact of each of these changes was going to be.
We even hired outside consultants who would spend a month evaluating these designs and give recommendations. We’d be adding several ferrites and inductors, adding more costs to the module, with no real guarantee that it’s going to pass when you make these changes. This started happening more and more often with the industry as a whole, instead of looking to see what needed to change in the design philosophy and the root cause of these problems. They would continue to use these Band-Aids, and they became rules of thumb.
We were told to put an inductor in series with the power supply to starve the switch to prevent radiated emissions. Well, that’s exactly the opposite of what the problem is. Most radiated emissions are caused by starving the part. It’s the depletion waves coming from the switch into the power supply that are the source of most radiated emissions failures that I deal with, and understanding the flow of energy was critical to that. So, as the industry gradually absorbed these smaller geometries, the percentage of failures in EMC testing continued to increase.
Even today, I asked the class, “How many of you have passed EMC the first time?” One person raised his hand. “How many spins does it take? Two?” Nobody raised their hands. At three and four, the hands start going up. They typically would run three, four, or five design cycles before they finally pass EMC. With each iteration, there was no more hope that they were going to pass than the first time. I got the same answer from my automotive customers.
Shaughnessy: Did they all budget in multiple respins?
Beeker: No, they never budgeted for that redesign. That’s the worst part of it. They don’t have it in the time schedule for the program. They don’t have the money to do a new redesign for the next spin of the circuit board and the associated expedite charges. They don’t have a plan for paying for, or even getting, parts because, especially nowadays, every piece of silicon is worth its weight in Laudanum, to use a Star Trek reference. So the result is that they lose maybe three to six, or even eight weeks in the schedule trying to do a new design that even then, they’re still not sure is going to pass EMC.
Each design cycle has an unexpected or un-admitted cost of anywhere from $50,000 to $250,000. That comes directly off the profit, and to continue to accept this is just not engineering. Unfortunately, I find my customers are willing to continue to pay these premiums to design boards they’re not sure will work rather than paying for their engineers to get the training or do some research to find out the root cause of the problem. Or hire an expert like Rick Hartley to come and do a design class so that their next effort will be more likely to succeed.
Shaughnessy: I’ve seen those diagrams, and I always assumed the signal traveled down the trace.
Beeker: Absolutely. For the first 25 years of my career, I was a dyed-in-the-wool circuit guy. I hooked the pins up, and they were supposed to work, and it worked. But in the first five minutes of Rick Hartley’s class, I had an epiphany while listening to him talk about the basics of signal integrity. I realized that every design that I had done had worked by accident, because I wasn’t considering the real energy movement. We were doing things wrong, but it wasn’t so wrong that they failed all the time.
In today’s world, where 2-nanometer parts are in production and 70, 60 picoseconds switching signals are common, you can’t ignore the science anymore. Ralph Morrison taught me that it’s actually very simple to control this energy. You have to design the dielectric. It’s the spaces. As long as you use that philosophy and build a solid foundation for your circuit board, the rest is no longer magic. It’s very simple and easy to make it happen.
Shaughnessy: So, where does a designer or engineer start?
Beeker: The stackup is the foundation. That’s where I start with a customer who has an issue with EMC, and they always wait until after they fail a couple of times, not in the beginning where we can make it happen early and save the money. I look at the board stack, and quite often, there’s a real problem right there. It takes five minutes. I know that there’s no way to fix this board without changing the stackup. For example, with a four-layer board, which is very common in automotive, they will try to get away without having at least one solid ground. A good foundation for a four-layer board would be layer one for signals and components, layer two a solid ground, layer three for routing and ground flood, and layer four is now a single-layer board. It has to be routed with co-planar ground traces to create the transmission lines, and then has to have those horizontal dielectrics on layer four connected in the Z-axis to the dielectric sitting in the space between 1, 2, and 3, which is a paired dielectric automatically.
With that foundation, it’s easy to go through and find the places where they miss simple things, which is usually the ground transition via that gives me the Z-axis transmission for the signals. When I go from layer one or three to four, I have to put a ground via. If there’s not a ground plane, then you don’t have a very good way of coupling all the energy in a four-layer board, and that provides the opportunity for any wavefronts to create radiated emissions.
Shaughnessy: What advice would you give somebody who’s just beginning to understand all of this, like you did years ago in Rick’s class? What advice would you give them, or any things to remember?
Beeker: Ralph’s last book was an excellent compilation of his life’s research. When Ralph writes these books, he speaks in English for the most part. However, he backs up each chapter with mathematics and solid science because his basic training was as a physicist. He later got his master’s in electronics. However, his whole focus was on the physics of electromagnetic fields. That would be a good start.
There are also some great classes that Rick Hartley and Ken Wyatt are doing on this topic. I’ve got a few things on the web too. Sierra Circuits sponsored a webinar in tribute to Ralph after he passed away. In that webinar, you get an introduction to Ralph and some of his legacy, and his widow discusses her life with him.
There are only three universities that I’ve been able to identify that connect the dots between electromagnetic field theory and electronic circuits or electrical engineering classes. Those are all absolutely tied to the work that’s been done at the former University of Missouri-Rolla, now the Missouri University of Science and Technology, where Dr. Todd Hubing and Dr. James Drewniak were two of the principal researchers. Dr. Hubing later went to Clemson as the endowed chair of the Michelin Automotive Technology Center. The third is Grand Valley State University in Michigan, again affiliated with graduates of Missouri.
What I see as the main issue is the industry itself. The companies that hire engineers are not going back to the universities and asking for a change in the curriculum. They aren’t recognizing that the skill sets are lacking in that vital connection. So the universities have no reason to change the curriculum because they don’t need to spend money when they already have established courses. They have customers who are buying their engineers. That has to change.
Shaughnessy: It sounds like an Achilles heel of the industry.
Beeker: I don’t want to call it an indictment of the industry, but it is certainly an issue that isn’t being addressed properly. If they really wanted to improve the product quality, reduce their design cycles, and increase profits, they would be a little more aggressive in figuring out why things fail instead of blaming their silicon vendors.
Shaughnessy: And then they’ll just keep creating workarounds to fix the problem.
Beeker: And they’ll use what worked last time. They just put a Band-Aid on a gaping wound.
The other thing that I’m worried about is that the simulation tools do not check for something as fundamental as whether a particular signal trace is one dielectric away from the ground to the source. It doesn’t check for that. If you don’t have a solid foundation where every signal is one dielectric from ground, and ground is the same conductor that goes from the energy source to the load, that has to be a continuous conductor. Next to that has to be a continuous dielectric where the energy flows.
None of the tools check to see if that’s true. As a result, you can do simulations that will tell you that your design is solid, but when you build it and test it, there are things that don’t work the way they’re supposed to. For example, the models are not complex enough to look at the entire three-dimensional structure. The fields always find the continuous conductor path from their location to the power supply source.
Shaughnessy: So, if you don’t provide it a path, the field will find its own path?
Beeker: It has to find it, and it will interact with everything around it as well. It will find that common conductor and the common dielectric from the pin on the connector, or switched conductor, all the way back to where the energy finally comes on. It’s pretty simple when you accept the fact that the geometry of the circuit board and the geometry of the integrated circuits are tightly coupled in their impact on each other. And to be able to do a good design, you need to be able to trust the geometry.
That was the hardest part—trusting the geometry. I knew that RF guys had to believe in this stuff, but I didn’t have to believe in it as the digital guy. It was somebody else’s deal. But that’s not true. You really have to be focused on the geometry of the spaces because now all of the ICs are so fast. Even if they’re switching at four megahertz, the ICs are switching in tens of gigahertz inside.
Shaughnessy: Is there anything else that you’d like to mention?
Beeker: No, just thank you. You’re doing a lot of work to help solve some of these mysteries. The more we can get the word out, the more people can start to go back and review Ralph’s work. I think we will find that the success rate will go from around 20%, maybe to closer to 40 or 50%. I did my first network control board, and it passed EMC the very first time. I trusted the geometry. Was it heart-wrenching when I sent it to be tested? You bet. But I kept telling myself, “Ralph’s rules. Trust the geometry.” And I did.
Shaughnessy: This has been great, Dan. Nice talking with you.
Beeker: Thank you again, and keep getting the word out about Ralph’s work.