-
-
News
News Highlights
- Books
Featured Books
- pcb007 Magazine
Latest Issues
Current IssueThe Hole Truth: Via Integrity in an HDI World
From the drilled hole to registration across multiple sequential lamination cycles, to the quality of your copper plating, via reliability in an HDI world is becoming an ever-greater challenge. This month we look at “The Hole Truth,” from creating the “perfect” via to how you can assure via quality and reliability, the first time, every time.
In Pursuit of Perfection: Defect Reduction
For bare PCB board fabrication, defect reduction is a critical aspect of a company's bottom line profitability. In this issue, we examine how imaging, etching, and plating processes can provide information and insight into reducing defects and increasing yields.
Voices of the Industry
We take the pulse of the PCB industry by sharing insights from leading fabricators and suppliers in this month's issue. We've gathered their thoughts on the new U.S. administration, spending, the war in Ukraine, and their most pressing needs. It’s an eye-opening and enlightening look behind the curtain.
- Articles
- Columns
- Links
- Media kit
||| MENU - pcb007 Magazine
Estimated reading time: 5 minutes
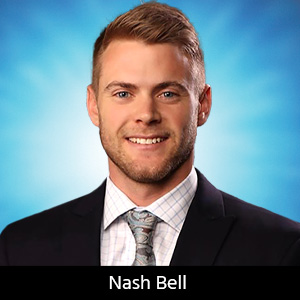
Knocking Down the Bone Pile: Methods for Underfilled Component Rework
Products such as engine control modules, drones, smartphones, and other handheld communication devices, which are designed for high reliability and require high processing power, often have a BGA or CSP package as the processor. Underfill has been a solution at the package level protecting these devices from the coefficient of thermal expansion (CTE) mismatch between the device and PCB or between the die and the component substrate for flip chip packages. Stress caused by CTE mismatch redistributes the stress from the bottom of the solder spheres to the entire component. Underfill also provides for a mechanical bond between these surfaces while providing very good protection for the solder joints against both mechanical and thermal strains as the product experiences vibration, drops, or thermal shocks.
Underfill is typically constructed from either an epoxy-based or other polymeric-based material and is dispensed in a controlled fashion underneath the component. Through capillary action and under increased temperature, the underfill makes its way underneath the component. It is typically cured by either thermal or thermo-sonic energy.
The downside of using underfill is that it causes the rework process to be extremely difficult. While some underfills are categorized as “reworkable” this does not mean that the underfill removal process is not without extreme challenges. There are several problems which arise from removing an underfilled component regardless of whether it is “reworkable” or “non-reworkable.” The problems are fairly numerous when the underfill is heated and moves around, breaking the bond between board and component. Some of the most common problems include:
- Twisting motion to break board/device bond during the component removal process may damage board or neighboring devices
- Using a sharp tool to “cut” the underfill so the component can be removed may damage neighboring components or the PCB
- Mechanically scraping or cutting away the underfill may cause damage to PCB or neighboring components
- The mechanical bond of the underfill to the PCB may cause the lifting of pads (Figure 1), laminate damage, or solder mask damage (Figure 1)
- The time-consuming nature of removing the underfill makes the rework process beyond economic repair
- Heating the solder underneath the BGA/CSP/QFN to a liquidus temperature for removal causes the underfill to begin to reflow, “pushing” solder out from the designated pad areas
- Neighboring underfilled components can be pushed off their pads during the removal process
There are numerous methods which can be used to rework these underfilled devices. Each method has both advantages as well as drawbacks.
The method used most often for reworking underfilled devices involves the use of a heat source to reflow the BGA while simultaneously creating a parting line in the underfill between the component and the PCB. This will release the component from the pads on the PCB, as the softened material still adheres to both the component and the board. Either the BGA rework system has a twisting motion to get the component removed or a bimetallic reflow nozzle “grabs” the suspect component for removal. After component removal, the site is dressed using a hot air source along with a tool such as a solder extractor or a hobby knife, or by utilizing a specific soldering iron chisel tip along with solder braid. If no BGA rework station is available, then a non-controlled heat source such as a heat gun can be used to remove the component from the board followed by clean up. These processes require care and skill by the operator to not damage the board or neighboring components.
Another method which can be used to remove the BGA by breaking the adhesive force of the underfill is via a softening agent. A solvent-based chemical—formulated by the underfill vendor—comes into contact with the underfill and softens it. This allows for easier removal of the underfill, thereby reducing the likelihood of component, mask, or pad damage. One of the drawbacks to this methodology is being able to get the softening agent to all areas of the underfill, as the hardened underfill blocks the liquid from getting to all areas. Furthermore, depending on how aggressive it is, the liquid can damage components and device markings as well as other coatings. Post softening agent application cleaning is also a challenge as analytical testing needs to be part of the process qualification. In many cases, the reliability risks imposed by this method are not worth the process time-saving rewards.
A further removal method of the component relies on laser ablation. In this method a directed laser source is programmed to scan the surface area of the laser back and forth to disintegrate or ablate the component, underfill, and some cases, the solder balls. At low laser flux (low laser energy density, w/cm2), the material is heated by the absorbed laser energy and sublimates. The laser beam is pulsed, electronically controlled, and the beam steered to not destroy neighboring components. This method is useful in applications where either the vibration of the board in precision milling presents too high a reliability risk or when either the component or board warpage is extreme.
A more recent addition to the underfilled BGA/CSP removal process list of alternatives is the use of a precision mill to cut away the device. Typically, “non-reworkable” underfill along with the component and solder is milled off the board. The board is fixtured properly to retain a flat surface, typically with the use of a vacuum fixture. Height sensors make sure the mill does not drive too far down into the board and damage it. Vacuum is also supplied near the cutting area to keep debris off the PCB. As reflow temperatures are not reached, lesser board damage results. The resulting vibration of the milling process and its effect on the board need to be investigated for the end use operating environment.
There are numerous methods for reworking underfilled area array and bottom terminated components. A skilled, experienced rework technician with several methods, including the machinery, available to them will determine the highest yielding method in the fastest amount of time.
This column originally appeared in the November 2021 issue of SMT007 Magazine.
More Columns from Knocking Down the Bone Pile
Knocking Down the Bone Pile: Tin Whisker Mitigation in Aerospace Applications, Part 3Knocking Down the Bone Pile: Gold Mitigation for Class 2 Electronics
Knocking Down the Bone Pile: Basics of Component Lead Tinning
Knocking Down the Bone Pile: Package on Package Rework—Skill Required
Knocking Down the Bone Pile: 2023’s Top Challenges in BGA Rework
Knocking Down the Bone Pile: Eliminating Solder Balls in Hand Soldering
Knocking Down the Bone Pile: Opening a Trace on the Surface of a PCB
Knocking Down the Bone Pile: Soldering for QFPs and Other Gull Wing Leaded Parts