-
-
News
News Highlights
- Books
Featured Books
- pcb007 Magazine
Latest Issues
Current IssueThe Hole Truth: Via Integrity in an HDI World
From the drilled hole to registration across multiple sequential lamination cycles, to the quality of your copper plating, via reliability in an HDI world is becoming an ever-greater challenge. This month we look at “The Hole Truth,” from creating the “perfect” via to how you can assure via quality and reliability, the first time, every time.
In Pursuit of Perfection: Defect Reduction
For bare PCB board fabrication, defect reduction is a critical aspect of a company's bottom line profitability. In this issue, we examine how imaging, etching, and plating processes can provide information and insight into reducing defects and increasing yields.
Voices of the Industry
We take the pulse of the PCB industry by sharing insights from leading fabricators and suppliers in this month's issue. We've gathered their thoughts on the new U.S. administration, spending, the war in Ukraine, and their most pressing needs. It’s an eye-opening and enlightening look behind the curtain.
- Articles
- Columns
- Links
- Media kit
||| MENU - pcb007 Magazine
Do You Really Need to Buy New Equipment?
November 9, 2021 | I-Connect007 Editorial TeamEstimated reading time: 3 minutes
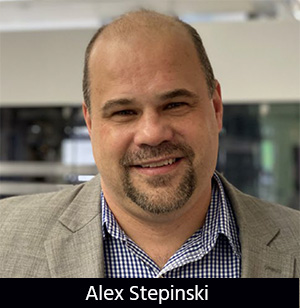
When we began looking into CapEx strategies for PCB manufacturing, we ran into a few company owners who were proud of making their old fabrication equipment last for decades. We recently spoke about CapEx planning with Alex Stepinski, former VP of GreenSource Fabrication, who built a zero-wastewater PCB fabrication facility from the ground up.
As Alex explains, your old equipment might actually last for decades, and if you need new equipment, you might find what you’re looking for in another industry.
Barry Matties: I’ve mentioned this in several interviews, but oftentimes I hear fabricators bragging that they’re building boards on a 20-year-old piece of equipment, as if that’s a win of some sort. What are your thoughts on that?
Alex Stepinski: Well, a 20-year-old piece of equipment is one thing, because you could be using a 20-year-old piece of equipment if it has decent controls. It’s really about the control level of the equipment.
When we talk about age, you could buy new equipment 20 years ago that will still be working today, and some of it works quite well. It’s just a matter of the type of controls that you put on it. Really, the value is in the engineering work that was done on that tool: How much engineering work was done, how was the capability developed, how well-understood is the tool?
If you have a well-understood tool, it could be 50 years old; you just need to be able to adjust controls or not. As long as you understand them, maybe you could adjust other aspects to compensate. It’s really about doing due diligence in process engineering.
Matties: If we’re talking about adding sensors, you have to be able to incorporate them into that aged equipment. You had a thought, Happy?
Happy Holden: Yes, I was really surprised that on our Alcon etching machines, the control system was from ADA Tech. When we delved into it and started making measurements closely, we found out that this thing was really imprecise, which got us to brainstorming about how we could build a better specific gravity controller. We actually came up with a $55 one we built ourselves that has .001 SG units control.
Stepinski: There you go. Exactly right.
Holden: They have them in the chemical industry, but they’re $5,000 to $10,000 each, while the one we devised was $55. The mechanical engineers kept saying it wouldn’t work. We finally dug out the textbooks and showed them, “You don’t remember Archimedes’ principle, the center of displaced mass. If we submerge the specific gravity sensor, then the mass never changes.” They were saying, “The way you guys got it arranged this thing won’t work.” But they had just forgotten that little minor part of Archimedes’ principle.
Stepinski: Yes. Nowadays, they’ll do a standpipe with a pressure transducer on the bottom, and that’s becoming more popular in the market on newer machines.
Holden: We had one of those also. A lot of times, we were taking things out of other segments: automotive, chemical, any place we could find a sensor that could be adept at printed circuits. And, of course, digitization of the automobile was great because then we got low-cost volume sensors that they used to measure gasoline, flow rigged. Rather than spending a lot of money on very precise metering pumps, we just bought precise flow-measuring devices, and not precise metering pumps.
Stepinski: Yes. I agree. I’ve gone to trade shows outside of our industry to learn a lot myself, because just staying in our industry trade shows restricts your vision a bit. Going outside and bringing in equipment from other industries was a big component of what I did at GreenSource.
Matties: Thank you so much, Alex.
Stepinski: It was nice speaking with you, too.
This interview originally appeared in the October 2021 issue of PCB007 Magazine.