-
- News
- Books
Featured Books
- pcb007 Magazine
Latest Issues
Current IssueSales: From Pitch to PO
From the first cold call to finally receiving that first purchase order, the July PCB007 Magazine breaks down some critical parts of the sales stack. To up your sales game, read on!
The Hole Truth: Via Integrity in an HDI World
From the drilled hole to registration across multiple sequential lamination cycles, to the quality of your copper plating, via reliability in an HDI world is becoming an ever-greater challenge. This month we look at “The Hole Truth,” from creating the “perfect” via to how you can assure via quality and reliability, the first time, every time.
In Pursuit of Perfection: Defect Reduction
For bare PCB board fabrication, defect reduction is a critical aspect of a company's bottom line profitability. In this issue, we examine how imaging, etching, and plating processes can provide information and insight into reducing defects and increasing yields.
- Articles
- Columns
- Links
- Media kit
||| MENU - pcb007 Magazine
Estimated reading time: 3 minutes
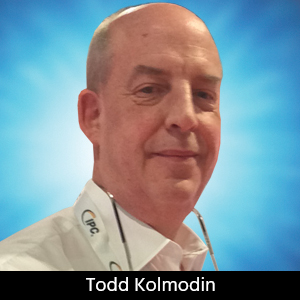
The New Electrical Test—Riding the Wave
Many years ago, when electrical test (ET) was necessary on a bare printed circuit board (PCB) you would build a dedicated fixture with spring pins and mount the box fixture to a machine interface and perform the test. However, back then there were no preconfigured netlists, and the machines were only capable of “learning” the board. This was known as the “self-learn” or “learn comparison” test. At the time, all you could do is prove that all the boards of the test lot were the same. The risk was that if there was a film defect and all boards had the same fault, the test would still pass even though all boards were defective.
As ET evolved, test machines gained the capability to save learned programs. Although still a “learn,” we gained the ability to compare lot to lot for consistency. It wasn’t the best solution but for the day, we worked with what we had.
As evolution progressed, the front-end systems began development of ET-related modules that could provide CNC drill files and programs that would support a handful of the test machines available. This was monumental as the self-learn was replaced by predetermined intelligence of the PCB. This raised the confidence level of electrical test significantly and unintentional scrap of product due to undetectable defects was greatly reduced.
Fast forward to today and electrical test, or test and measurement, has made significant advances. No longer self-learning (in most cases), ET now includes a battery of test options. It is not just “opens and shorts” but TDR, IR, buried passives, 4-wire Kelvin, and even buried inductance.
An advanced test floor may resemble an ICU with all the equipment around for these test options. You have machines for basic opens and shorts, TDR, inductance, HiPot, and IR. This can become costly to operate and maintain. Many OEMs are now requiring these tests as basic criteria for acceptance. All this equipment requires space and, of course, money.
The key to success is to do more with less. This is the 5S discipline at work. Today, the larger test facilities and equipment manufacturers are working to combine the requirements to single points of service. To streamline and provide cost effectiveness, these tests are being combined into single machines. Imagine a machine that can provide standard opens and shorts testing but can also provide buried passive testing, HiPot, 4-wire Kelvin, IR, and inductance testing from one platform. It is available right now. No more need for multiple test stations, machines, and extra operators. In the July 2021 issue of PCB007 Magazine, my column, “The PCB Limbo—How Low Can You Go,” we discussed that price pressure is common and we must progress to maintain margins that keep us in business. The solution is machine combination testing which reduces operation and labor cost. We must make what we have do more.
The next progression is AI and automation. Systems are now available that communicate with internal databases that validate machine abilities, maintenance status, calibration status, and historic test data for any given part. If a machine is overdue for maintenance or calibration, the system disallows operation of that machine until remediation is completed for the point of error. Further, competence and training can be incorporated so that any operator who is not trained in a particular test method or type will be disallowed to continue.
These are just some of the newer competencies available with production systems of today. Speak with your service provider to see if they are doing more with what they have. It is the wave of the future and the best way to save money while enjoying the total benefits of what is now available to you.
This column originally appeared in the November 2021 issue of PCB007 Magazine.
More Columns from Testing Todd
Testing Todd: Why 4-wire Kelvin?Testing Todd: Why TDR?
Testing Todd: Positivity Boosts Employee Morale
Testing Todd: Preparing Employees for the Long Haul
Testing Todd: Where Can We Improve?
Testing Todd: Turning Into the Wind
Testing Todd: Coming Back to Life—Design Recovery
Testing Todd: Decision Time—Invest or Delegate?