-
- News
- Books
Featured Books
- smt007 Magazine
Latest Issues
Current IssueWhat's Your Sweet Spot?
Are you in a niche that’s growing or shrinking? Is it time to reassess and refocus? We spotlight companies thriving by redefining or reinforcing their niche. What are their insights?
Moving Forward With Confidence
In this issue, we focus on sales and quoting, workforce training, new IPC leadership in the U.S. and Canada, the effects of tariffs, CFX standards, and much more—all designed to provide perspective as you move through the cloud bank of today's shifting economic market.
Intelligent Test and Inspection
Are you ready to explore the cutting-edge advancements shaping the electronics manufacturing industry? The May 2025 issue of SMT007 Magazine is packed with insights, innovations, and expert perspectives that you won’t want to miss.
- Articles
- Columns
- Links
- Media kit
||| MENU - smt007 Magazine
Test and Inspection: Competitive Advantage and Cost of Doing Business
December 8, 2021 | Nolan Johnson, I-Connect007Estimated reading time: 3 minutes
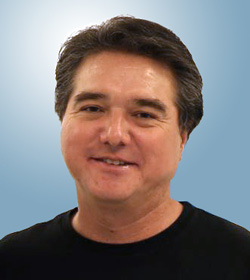
In this interview, Charlie Capers of Zentech breaks down the changing requirements he’s seeing in test and inspection in the industry, and the growing importance of investing in testing for the future growth and success of your company.
Nolan Johnson: Charlie, test strategies seem to be all over the place.
Charlie Capers: Everybody does everything a little differently. It depends on your shop, your processes, the size of your shop, and the volume of the stuff you’re doing.
Johnson: What seems to be emerging is increased activity with the IPC J-standard; the shifts in how you approach ROSE testing, in addition to the customer-driven and OEM-driven demands that are changing for testing inspection regarding finished product. This is especially true for military and medical, which are starting to demand them.
Capers: Yes. Those are the top ones.
Johnson: As you move toward automation, isn’t there an increased need for test and inspection as a part of process control?
Capers: Yes. Maybe in larger shops, I would believe that. They go hand in hand. When you collect statistics on defects, you will start to see a trend that says, for example, we’ve got a lot of shorts and opens, meaning that our solder paste process is not tight. If you’re collecting statistics and really studying them, you will see trends in your processes. It’s part of the AS9100 too; you must collect your statistical data and review it every year.
Johnson: The trick is how to make it meaningful. Turning that not just into data but into intelligence and analysis seems to be where the gap is right now.
Capers: Yes. I would agree with that. You can collect data all day long. You can look at it and see you’re having issues, but unless you dig deep and ask why the issues in this particular area or with this particular defect are there, then all the data collection is kind of useless—but we do it anyway.
Johnson: From where you sit, have you seen any interesting work to turn that into usable intelligence?
Capers: We are currently using it for our internal records, and for our requirement of AS9100. If you dig deep, you could probably say something like, “Operator number 13 is screwing up left and right.” But is it a personnel issue? Is it a process issue? Is it a machine issue? What is it? At our size, we probably have the capability, but not the resources, to dig deep into that type of stuff.
Johnson: How do you get software tools to the smaller firms, which make up the bulk of the active companies in the U.S.?
Capers: The tools are not only the software; it’s capital equipment that helps ensures your processes are good. You could have every certification in the world: plaques, trophies, and all of this, for all the good work you do. But at the end of the day, it comes down to price, and everything else is expected. After putting money into AXI, ICT, AOI, flying probe and all those good things, it would be nice to be able to recoup that money. These days, though, it’s assumed that you will be doing all these processes.
Twenty years ago, maybe you could buy an AOI machine and be able to charge for that service. For ICT and flying probe test, we must charge because there’s a development cost involved with it. For flying probe testing, you must program the machine and debug the program to make sure it runs correctly. For ICT, of course, you must program the machine, but you also must procure a test fixture to put on that machine, a bed-of-nails test fixture. There are costs involved in that. In our little world, we must pass those through. For big production, I’m sure it’s just built into the price of “we’re going to build you a million boards and this is what it’s going to cost, and we’re going to guarantee everything.” It’s a different world.
To read this entire conversation, which appeared in the November 2021 issue of PCB007 Magazine, click here.
Testimonial
"Advertising in PCB007 Magazine has been a great way to showcase our bare board testers to the right audience. The I-Connect007 team makes the process smooth and professional. We’re proud to be featured in such a trusted publication."
Klaus Koziol - atgSuggested Items
Weller Tools Supports Future Talent with Exclusive Donation to SMTA Michigan Student Soldering Competition
07/23/2025 | Weller ToolsWeller Tools, the industry leader in hand soldering solutions, is proud to announce its support of the upcoming SMTA Michigan Expo & Tech Forum by donating a limited-edition 80th Anniversary Black Soldering Set to the event’s student soldering competition.
Koh Young Appoints Tom Hattori as President of Koh Young Japan
07/21/2025 | Koh YoungKoh Young Technology, the global leader in True 3D measurement-based inspection solutions, announced the appointment of Tom Hattori as President of Koh Young Japan (JKY).
Silicon Mountain Contract Services Enhances SMT Capabilities with New HELLER Reflow Oven
07/17/2025 | Silicon Mountain Contract ServicesSilicon Mountain Contract Services, a leading provider of custom electronics manufacturing solutions, is proud to announce a significant upgrade to its SMT production capability with the addition of a HELLER 2043 MK5 10‑zone reflow oven to its Nampa facility.
Knocking Down the Bone Pile: Addressing End-of-life Component Solderability Issues, Part 4
07/16/2025 | Nash Bell -- Column: Knocking Down the Bone PileIn 1983, the Department of Defense identified that over 40% of military electronic system failures in the field were electrical, with approximately 50% attributed to poor solder connections. Investigations revealed that plated finishes, typically nickel or tin, were porous and non-intermetallic.
SHENMAO Strengthens Semiconductor Capabilities with Acquisition of PMTC
07/10/2025 | SHENMAOSHENMAO America, Inc. has announced the acquisition of Profound Material Technology Co., Ltd. (PMTC), a premier Taiwan-based manufacturer of high-performance solder balls for semiconductor packaging.