-
- News
- Books
Featured Books
- smt007 Magazine
Latest Issues
Current IssueWhat's Your Sweet Spot?
Are you in a niche that’s growing or shrinking? Is it time to reassess and refocus? We spotlight companies thriving by redefining or reinforcing their niche. What are their insights?
Moving Forward With Confidence
In this issue, we focus on sales and quoting, workforce training, new IPC leadership in the U.S. and Canada, the effects of tariffs, CFX standards, and much more—all designed to provide perspective as you move through the cloud bank of today's shifting economic market.
Intelligent Test and Inspection
Are you ready to explore the cutting-edge advancements shaping the electronics manufacturing industry? The May 2025 issue of SMT007 Magazine is packed with insights, innovations, and expert perspectives that you won’t want to miss.
- Articles
- Columns
- Links
- Media kit
||| MENU - smt007 Magazine
Real Time with… productronica: Electrolube is Going Green
December 14, 2021 | Pete Starkey, I-Connect007Estimated reading time: 9 minutes
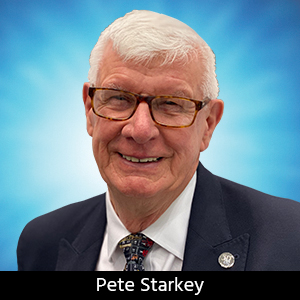
Pete Starkey visits with conformal coatings expert Phil Kinner from Electrolube of MacDermid Alpha Electronics Solutions, about the company’s involvement in productronica, its new bio-friendly conformal coatings, and how the acquisition by MacDermid Alpha is opening new doors for Electrolube in the automotive industry.
Pete Starkey: I’m speaking with Phil Kinner, the global head of R&D at Electrolube of MacDermid Alpha Electronics Solutions. Phil, it’s great to talk with you again. You’ve been a regular columnist with SMT007 and you’re acknowledged as the expert on conformal coatings. Your series of “Coatings Uncoated” webinars gave us a lot of detailed information on conformal coating chemistries and properties, applications, and processing guidelines.
The productronica event has just finished and Electrolube has launched a new conformal coating that’s been recognized as a real innovation for the electronics community. Your UVCLX is described as a pioneering new bio-coating with 75% of its organic content obtained from renewable sources. Yet it’s capable of protecting electronic circuitry against the harshest of environments, particularly those typical of automotive applications. Could you expand a little? What do you mean by bio-coating?
Phil Kinner: Let’s start by saying thanks for the introduction; you’re far too kind. In terms of our bio-coating, most of the carbon-based materials we’ve used have been derived from plant-based sources. Not only are they capturing carbon dioxide from the atmosphere during their growth, but they’re also preventing release in the form that we use them. The carbon is renewable and it’s a win in both directions.
Starkey: What was the inspiration for moving in that direction? Was there some specific objective?
Kinner: In the news, there had been a lot of focus during the pandemic about changing extreme weather events in America, in Italy, in Europe, Australia with the wildfires, and so forth. There was a lot of emphasis during the lockdown on reductions in CO2 emissions because no one was going anywhere or doing anything. So, this started off as a Friday afternoon project and very quickly we realized that we could not only make a product that was better for the environment, but we could make a product that protected against environments better than traditional materials from fully petrochemical-based processes.
I’d love to say it was because of an insightful conversation with a customer, but during the development process, we got a couple of RFQs from some automotive companies, from some OEMs and tier-ones that, for the first time ever, banned the use of solvents and talked about sustainability as part of the RFQ process. That felt like a vindication of our Friday afternoon experiment and it led to where we are now. You know how these things work: You have a stage gate, and we have to clear stages to keep the project moving. Having interest from the large automotive customers definitely helped.
Starkey: Certainly a great motivator.
Kinner: It helps get through the gate when you say, “Customer X has just asked for exactly this product in their latest RFQ.” It was pretty interesting.
Starkey: So, it’s a solvent-free formulation?
Kinner: Yes, it’s solvent-free two-component polyurethane material. Predominantly it’s UV curing, so the material cures instantaneously with radiation of the correct wavelength. It works particularly well with LED 365 nm, which is much more energy efficient than traditional Arc or Micro-wave sources and therefore much better for the environment.
Starkey: What about the shadow areas, those that the UV can’t reach or can’t penetrate?
Kinner: That’s where the real benefit of the two-component formulation comes in. Once the two components are mixed, they react within six to 12 hours. Without any additional steps, once those materials are mixed, you know they’re going to cure. You know that you’re going to have a fully cured material within 12 hours, which is a significant improvement on the traditional one-component materials, which use moisture to initiate their secondary cure mechanism. My favorite question from customers is always, “How long is that going to take?” and all you’ve got is every engineer’s least favorite answer, “Well, that depends…”
Starkey: So, effectively, this material would cure without any UV at all?
Kinner: That’s correct.
Starkey: But UV sets it instantaneously and cures it more quickly?
Kinner: Yes, exactly. No one wants a material that’s going to take six to 12 hours to cure. Well, maybe someone would, but from an automotive point of view, they’re very interested in single-piece flow. Having the material cure with UV instantaneously is a big plus from a productivity point of view, but also from a staging and work-in-progress point of view. Because the secondary cure is done so quickly, it’s probably going to be complete by the time it’s put in its final housing and finished its journey around the factory floor. That’s one less thing to worry about.
Starkey: How do you apply it? What sort of equipment do you use?
Kinner: It’s designed for selective coating. Selective coating has become the dominant application method, particularly in the automotive industry. It’s the same as all the two-component materials that we’ve been working on from an application point of view. You can spray it, you can dispense it, or you can do both, depending on the complexity of the assembly that you’re coating. The material is green in color and green in nature.
Starkey: Oh, that’s nice.
Kinner: This facilitates inspection. People say the solder mask is green; it is, but it’s a different green. And this green contrasts very well with the solder masks, so it’s easy to inspect with the naked eye. It’s easy to inspect with automated inspection equipment. In fact, with most systems, traditionally they’ve relied on fluorescence and the coatings to glow blue, or to fluoresce blue under black light. But metals also fluoresce under black light, and one of the big issues with coating is getting coverage on the metal solder joints, particularly the knees of gull-wing components.
Starkey: What sort of thickness do you recommend? Is the formulation such, or the flow characteristics such, that it maintains its thickness on edges and corners?
Kinner: Yes, much of the focus of my team’s efforts over the last five or six years has been about improving coverage over edges. This material is no different; it’s formulated to be applied more thickly and still pass the various tests. But the key focus is making sure it stays at an adequate thickness on those vertical edges that traditionally are very difficult to coat with existing solvent-based UV or UV-curable materials. We have a lot of cross-sections that show the typical thickness profiles and typical coverage characteristics for this material.
Starkey: What level of protection does this material provide? And what testing would you use to demonstrate it? What typical results would you expect?
Kinner: For anyone who has followed what we’ve been doing for the last few years, condensation testing or condensation resistance testing, and immersion testing are traditionally two of the most challenging areas for conformal coating. We’ve put these materials through immersion tests and condensation tests, and they’ve passed very well. They’ve passed perfectly through the BMW test or the NPL test, which is my preferred test method. The other issue that we see as a significant problem with existing UV materials, the single component materials, is they tend to crack during thermal shock testing.
Often that’s a combination of the inherent material properties, but also the interaction between the coating and various paste residues that tend to get left behind. That’s a pretty broad area, and I won’t go into that, but suffice to say, the material characteristics are something that can and have been improved. The interaction with flux residue still remains, unfortunately, a case-by-case scenario that always needs testing.
Starkey: No, it certainly sounds like this is as described, a game-changing material. How was it received at the show? Was it received very enthusiastically?
Kinner: I spoke to a couple of automotive tier-ones that were interested in evaluating the material. For us, one of the biggest wins is the acquisition by MacDermid Alpha, which is an approved supplier at most of the tier-one OEM automotive guys, so we are covered under that umbrella too. People who wouldn’t necessarily have spoken to us as their first-choice supplier are now talking to us.
Starkey: I’ve seen that Electrolube is now part of the MacDermid Alpha Electronics Solutions group. That would appear to be a very natural strategic fit in terms of complimentary products, material-science capability, and technical expertise. As you’ve just mentioned, there’s the customer relationship. I’m sure this partnership will be enormously successful.
Kinner: Yes, it’s very exciting. I flippantly said it’s a nightmare for me, because I always used to blame the paste guys, or the solder mask guys or the plating guys for something earlier in the process that was leading to failures. So, less flippantly, it’s a brilliant opportunity to understand and expand my knowledge. And productronica was a good opportunity to speak to some of my new colleagues in the paste and other parts of the assembly business. For me, I sat with a customer talking about paste and he listened patiently while the paste guys were explaining all the solder benefits, less voiding this, and stuff. But he said, “Well, that’s all very interesting, but what’s left behind afterward that is going to mess with my adhesives, my coatings, or my encapsulation resins?”
Traditionally, that’s been an interface that’s been somewhat problematic. But we’ve already started having conversations about doing more compatibility testing and developing products for the future that have each other’s characteristics in mind. It’s already kind of proving fruitful. For the first time, productronica has been more use to me from an internal networking and meeting people point of view, than it has for meeting customers. I never ever thought I’d find myself saying that, but in this case, it’s absolutely true. The future looks really exciting and it will be interesting to see what transpires over the next couple of years as we start getting into these projects.
Starkey: I’m sure it’ll work out fine, and it’s nice to see. We will stay closely in touch and review as time goes on. I see no reason at all why it shouldn’t work really, really well.
Kinner: That’s the scary bit when you don’t see any potential downside; it sets your skin on edge a bit. What are you missing? What’s going to come back and bite you? But in this case, it’s just a natural fit. Like I say, it opens up some terrific opportunities to make better products.
Starkey: Sure. It’s always interesting to talk to you and a great pleasure. Thanks for all the information you’ve shared. I hope to see you again soon, and hopefully in person.
Kinner: I look forward to it Pete. Always a pleasure, and thanks for all the kind words and all the support. Much appreciated.
Starkey: You’re very welcome.
Check out this additional content from Electrolube:
- The Printed Circuit Assembler's Guide to… Conformal Coatings for Harsh Environments by Phil Kinner (a free eBook available for download)
- “Coatings Uncoated!”?a free micro webinar series
- You can also view other titles in our full I-007e Book library here.
Testimonial
"Advertising in PCB007 Magazine has been a great way to showcase our bare board testers to the right audience. The I-Connect007 team makes the process smooth and professional. We’re proud to be featured in such a trusted publication."
Klaus Koziol - atgSuggested Items
Weller Tools Supports Future Talent with Exclusive Donation to SMTA Michigan Student Soldering Competition
07/23/2025 | Weller ToolsWeller Tools, the industry leader in hand soldering solutions, is proud to announce its support of the upcoming SMTA Michigan Expo & Tech Forum by donating a limited-edition 80th Anniversary Black Soldering Set to the event’s student soldering competition.
Koh Young Appoints Tom Hattori as President of Koh Young Japan
07/21/2025 | Koh YoungKoh Young Technology, the global leader in True 3D measurement-based inspection solutions, announced the appointment of Tom Hattori as President of Koh Young Japan (JKY).
Silicon Mountain Contract Services Enhances SMT Capabilities with New HELLER Reflow Oven
07/17/2025 | Silicon Mountain Contract ServicesSilicon Mountain Contract Services, a leading provider of custom electronics manufacturing solutions, is proud to announce a significant upgrade to its SMT production capability with the addition of a HELLER 2043 MK5 10‑zone reflow oven to its Nampa facility.
Knocking Down the Bone Pile: Addressing End-of-life Component Solderability Issues, Part 4
07/16/2025 | Nash Bell -- Column: Knocking Down the Bone PileIn 1983, the Department of Defense identified that over 40% of military electronic system failures in the field were electrical, with approximately 50% attributed to poor solder connections. Investigations revealed that plated finishes, typically nickel or tin, were porous and non-intermetallic.
SHENMAO Strengthens Semiconductor Capabilities with Acquisition of PMTC
07/10/2025 | SHENMAOSHENMAO America, Inc. has announced the acquisition of Profound Material Technology Co., Ltd. (PMTC), a premier Taiwan-based manufacturer of high-performance solder balls for semiconductor packaging.