Estimated reading time: 4 minutes
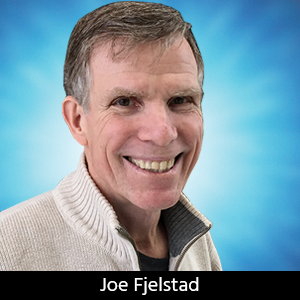
Flexible Thinking: Shaping Flexible Circuits
It is axiomatic that bending and folding are fundamental to flexible circuits. The reality is that most flex circuit applications are ones where the circuit is made to conform to the confines of the package that contains it to meet product design objectives. This matter is often glossed over but it is often very important to get the flex circuit to take on a reasonably permanent shape to facilitate its installation into a housing.
Bending flex circuits for static, form-to-fit applications is common; however, getting the flex circuit to hold shape often requires more attention and, in some cases, more processing. This is because flexible circuits, depending on the material used, have varying amounts of elastic memory; that is, the circuit will often try to return to its planar shape. Thus, there is need in such cases to use some established design and process principles for more accurately and permanently shaping flexible circuits to fit permanently in their application.
The first principle of getting a flex circuit to hold shape is to maximize the metal content of the design. This can be accomplished by increased metal thickness, total metal area in the design, or both. Metals, such as copper, have higher moduli of elasticity and tensile strength than the flexible polymer elements of flex circuit construction but they also are capable of plastic deformation and will permanently deform plastically when bent, provided its elastic limit is not exceeded to the point of fracture.
Many polymers (elastomers are generally excluded, though they can also take a set over time) will also permanently deform if their elastic limit is exceeded. In the case of flex circuit laminates, however, the elastic limit of the flexible carrier film is normally many times greater than the elastic limit of metal. Thus, when the composite structure we call a flex circuit is bent and holds shape to some degree, the metal has plastically deformed while the polymer is still likely to be in its elastic range.
To prevent the polymer from snapping back after bending the flex circuit, it must overwhelm the elasticity of the polymer. Copper is stronger and higher in elastic modulus, however if the circuit traces are thin and small or few relative to the width of the bend area (i.e., the copper is a low percentage of the surface area through the bend), the remnant elastic strain in the polymer may cause the flex circuit to try and return to its original flat shape.
One solution is to uniformly or selectively widen circuit traces through the bending zone to maximize the copper in the bend area as illustrated in Figure 1. Alternatively, if there are electrical/electronic concerns about the trace widths for controlled impedance reasons, fill the spaces between traces with non-functional metal. However, to complete the thought, if the signals are controlled impedance, this method may alter characteristic impedance of the signals and should be checked or modeled. Also, if the design has a weight budget, the impact of the weight increase due to copper should also be considered.
As alluded to earlier, if widening the traces alone is not sufficient, then one of two analogous methods can be employed. One can either use a thicker metal foil or use a thinner flexible base material. The objectives remain the same as they were in the first case: make certain that the metal can overwhelm the polymer in order the hold the final shape. There are advantages and disadvantages to both paths. Making the copper thicker may make etching a bit more difficult; it will also take longer to etch and use more chemistry. On the other hand, making the polymer thinner could make handling a bit more difficult and the strength of the final assembly will not be as great as the alternative method.
In many cases, slight overdriving of the circuit in the bend area can help to create a stable and more permanent shape but be careful that the guidelines for the minimum bend radius for the flex construction are not violated. Remember that when permanently bent and plastically deformed, the copper is normally thinned in the bend and is thus weakened. If a truly accurate predictive solution is desired, one can use finite element modeling methods.
Another way to get the flex circuit to hold shape for the application is to form it, commonly done by using a mandrel designed to bend the circuit into shape. The manufacturer can then heat the fixture to a temperature near the glass temperature of the adhesive used in the flex circuit and allow the circuit and fixture to cool in place before removing it. This approach works easiest with polymers and/or adhesives that have relatively low melting points.
Another option is to use less common base materials. These would be materials of low strength and having little, if any, elastic strength. UnreinforcedFEPor PTFE (i.e., Teflon), for example, fall into this category. This combination will allow the user to permanently deform the circuit into the desired shape.
To summarize, getting flex circuits to hold shape in an application is not that difficult, but it does take some attention. Several options have been discussed but the method of choice relative to those mentioned here will obviously depend on the demands of the design and its application.
This column originally appeared in the December 2021 issue of Design007 Magazine.
More Columns from Flexible Thinking
Flexible Thinking: The Key to a Successful Flex Circuit Design TransferFlexible Thinking: Flexible Circuit Technology—Looking Back and Forward
Flexible Thinking: Mind-tapping into January
Flexible Thinking: Another PCB Design Paradigm Shift in the Works
Flexible Thinking: Rules of Thumb—A Word to the Wise
Flexible Thinking: Musings on High Density Interconnections
Flexible Thinking: Integrated Passive Devices—Design Solutions With Many Benefits
Flexible Thinking: Mechatronics in a Flex World