-
- News
- Books
Featured Books
- pcb007 Magazine
Latest Issues
Current IssueThe Hole Truth: Via Integrity in an HDI World
From the drilled hole to registration across multiple sequential lamination cycles, to the quality of your copper plating, via reliability in an HDI world is becoming an ever-greater challenge. This month we look at “The Hole Truth,” from creating the “perfect” via to how you can assure via quality and reliability, the first time, every time.
In Pursuit of Perfection: Defect Reduction
For bare PCB board fabrication, defect reduction is a critical aspect of a company's bottom line profitability. In this issue, we examine how imaging, etching, and plating processes can provide information and insight into reducing defects and increasing yields.
Voices of the Industry
We take the pulse of the PCB industry by sharing insights from leading fabricators and suppliers in this month's issue. We've gathered their thoughts on the new U.S. administration, spending, the war in Ukraine, and their most pressing needs. It’s an eye-opening and enlightening look behind the curtain.
- Articles
- Columns
- Links
- Media kit
||| MENU - pcb007 Magazine
Rogers: Mergers, Automotive, and a Bright Future
December 16, 2021 | Pete Starkey, I-Connect007Estimated reading time: 9 minutes
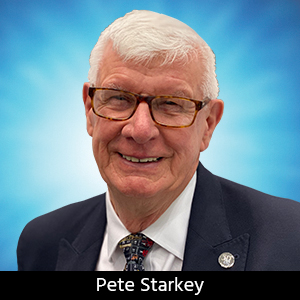
Pete Starkey visits with Ingmar van der Linden, market segment manager at Rogers Corporation in the Netherlands, about the products his company was demonstrating during productronica. Pete asks Ingmar about the automotive industry, particularly Rogers’ involvement in producing materials for sensors that create a safer driving experience. They also discuss the merger with DuPont, the trend toward material technologies and how to enable them.
Pete Starkey: I’m here with Ingmar van der Linden, market segment manager at Rogers Corporation in the Netherlands. Ingmar, it’s good to meet you and thank you for joining us.
Ingmar van der Linden: Thank you, Pete. I have been working at Rogers for six years, focused on the commercial radar market segment. Within Rogers, that’s very much focused on the trends in automotive radar and industrial radar sensors.
Starkey: Ingmar, for as long as I can remember, Rogers has been acknowledged as a global leader and innovator in advanced electronic materials. I have fond memories of processing RT/duroid® PTFE laminates many years ago in my days as a specialist PCB fabricator. Rogers is still recognized as a leading solution provider, especially in automotive and Industry 4.0 radar applications.
Rogers Corporation has been in the news lately, with DuPont announcing their plan to integrate the company with DuPont’s Electronics & Industrial business unit. I see it as a natural strategic fit in terms of complimentary products, material science capabilities, technical expertise, and customer service. I’m confident that the relationship will be enormously successful.
Van der Linden: Yes, that’s correct, Pete. We are very excited about the announcement. Rogers forms a strong strategic fit with Dupont, and it proliferates on the success of Rogers’ more than 180 years as a global leader in engineered materials solutions. In the automotive industry, we have been growing fast in EV/HEV and ADAS with PCB material technologies in the last few years, and we have been successful even beyond that in the wireless industry and aerospace and defense markets. From that perspective, we can see that this has been a successful ride for Rogers. Our combination with DuPont, a proven leader in technology-based materials, provides resources and support to allow Rogers to scale for success. The combination will create an exciting next chapter for Rogers’ customers, employees, and partners.
Starkey: I think it’s going to turn out well; I get all the right feelings about it. Now, the productronica event has just finished. Tell us something about the products you’ve been exhibiting and how they relate to the trends in the European market.
Van der Linden: Yes, of course. First, let’s start with the key trends and relate them to productronica. At productronica, the key focus was on smart maintenance, smart factory, autonomous driving, and electromobility. At productronica, we have seen companies that present mostly materials, machines, and services. Like us, those are materials to enable those trends. Quickly moving back to those key market trends and then focusing, as the next step, more on the products we have been exhibiting there. In the automotive industry, the key trend is on active safety, comfort by autonomous driving functions, and electrification.
Around the year 2010, most cars were equipped with airbag systems. In the last five years there has been an emerging trend to include active safety systems, so-called advanced driver assistance systems in cars. Instead of “passive” safety, this is really “active” safety. This safety trend is driven by governments and the global New Car Assessment Programmes that want to increase vehicle safety requirements.
As you know, Pete, to increase that active safety in cars you have different types of sensor systems supporting that, such as cameras, ultrasonic sensors, and radar sensors. With the radar sensors, an important thing is that these operate at millimeter-wave frequencies. If we look into those sensors, and into the job we do with our materials within these millimeter-wave sensors, our materials are providing antenna performance. They play an important role in the antenna, radiating energy out of the radar. On the other hand, they are an important enabler of the interconnection between the chip and the antenna.
If we take that a step further, these materials provide excellent electrical properties, such as tightly controlled dielectric constant and low insertion loss. But if we talk about the chip to the printed circuit board connection, it provides reliable and electrical mechanical performance over time and temperature. So, this is connected to the market trend of automotive radar and is growing fast within automotive radar.
We also have advanced mobility. This is a different trend, talking about autonomous driving cars basically providing mobility as a service for people, such as, for example, in driverless robot taxi services like Cruise and Waymo. Again, the requirements are a little different than on the safety side. Performance of the radar needs to be much higher.
You also will see more radars around the car and Rogers’ materials play an important role. For example, our RO3003G2™ laminate provides the best-in-class performance for insertion loss and stable dielectric constant in rough environmental conditions.
We just talked about automotive, but taking it a step further, Industry 4.0 is the next big trend in manufacturing automation where we see the same as what has happened in automotive in the last five years. It’s about gathering data from factories and providing factory automation for IoT type of applications. Again, Rogers’ products play an important role by providing different performances for radar sensors, which are used to get data and to enable system automation.
Starkey: Thanks for that, Ingmar. Rogers is a global company, so how do trends in Europe compare with those in North America and in Asia? Where are the technology leaders based and what challenges are they presenting to your development people?
Van der Linden: If we take a closer look, particularly in the automotive industry, we see the trends from Europe and United States translating to Asia. In the United States, the trend is more focused on higher levels 4-5 of autonomous driving, whereas in Europe, we see the focus is more on providing safety, and Level 2- 3 automated cars.
Coming back to the challenges these manufacturers of cars and radar sensor suppliers see, it is all about providing more performance and miniaturizing the electronics. For example, the number of sensors in the car is increasing and the number of computers in cars is increasing. But at the same time, weight needs to be reduced, and we need to take into consideration the environmental footprint. Therefore, electronics needs to be miniaturized and at the same time performance needs to increase. These are the global trends we see now.
Starkey: From your perspective, what will the European market look like in five years?
Van der Linden: We see that the European market, from an automotive perspective, will continue to maintain. The number of cars produced per year will not necessarily grow, but the way the cars are equipped will be different. It also ties into the trend of electrification, and this is where Rogers plays an important role with curamik® Metallized Ceramic substrates enabling power electronic circuits. More cars will be electrified and will contain more sensors and more computers to provide new functions, for example, autonomous driving or new or additional safety functions.
Starkey: So, you will continue to be an integral part of those developments and your relationship with that market will obviously lead the development priorities from your R&D side.
Van der Linden: Yes, indeed. We have our PCB direct customer base, but we also have close partnerships along the supply chains with car manufacturers, Tier-1’s and semiconductor industry. Rogers is providing services to all our partners along the supply chain. For example, material characterization, and lately we also have started RF and thermal simulations services. There’s also a very strong technical engineering service support, for example, for our PCB customers, to help them to manufacture our products, accelerating our customer’s success.
Starkey: I’m an old PCB fabricator. And I already mentioned the fun we used to have processing RT/duroid laminates. Recently, I read an interesting article by John Coonrod entitled “Some Exotic PCB Processes Could Become Commonplace.” He talked about using PCB technologies for very high frequency applications, above 77 gigahertz, which effectively go beyond established manufacturing capabilities regarding imaging and etching tolerances. Presently, it seems that the use of semiconductor techniques on glass is the only solution for 140 gigahertz devices.
But it’s really a question of how PCB technology can be developed to achieve these objectives. Techniques like laser machining for generating high-precision circuit geometry may be developed into production processing over time, but regarding materials, he talked about fusion bonding technology for PTFE based materials. He mentioned specifically your XtremeSpeed RO1200™ family of products for very high-speed digital, for example, 56 gigabits per second and 112 gigabits per second applications, and using XtremeSpeed RO1200 bondply and a fusion bonding process for the best possible results. However, he mentioned that very good high-speed digital results could be achieved using the XtremeSpeed RO1200 core with your SpeedWave® 300P prepreg. From the PCB fabricator’s point of view, the benefits of the SpeedWave 300P prepreg are that it does not need fusion bonding and it will have lamination process parameters more in line with high volume PCB production. Do you have any comments?
Van der Linden: Pete, that’s a very good summary of these things but I think what John was saying is the trend indeed is going in that direction on longer term. In automotive radar, the main frequency allocation is at 77 GHz. Longer term, we will see more radar applications at higher frequencies which go beyond 140 GHz and these require circuit features with extreme precision.
At Rogers, the key is material technologies and, looking forward, how to enable these things.
Starkey: I think it’s going to be very challenging for the PCB fabrication industry to adapt and develop its manufacturing processes to cope with the new generation of designs to suit the applications that we know are coming and the materials that you have formulated in anticipation of these requirements. But I say from a PCB fabricator’s point of view, I’m quite pleased that I can reflect upon, 30 years ago, my enjoyment of some of the manufacturing challenges using the early RT/duroid materials.
Ingmar, is there anything else you’d like to mention?
Van der Linden: Coming back to productronica, it was a great success to meet our clients in this leading European event again, and have one-on-one conversations, even with the special restrictions. Like you mentioned, these conversations with our customer base about PCB manufacturing are so important to understand what customers need for their next-generation systems. And we will continue to do that as we did for the last 180 years.
We are looking forward to a successful year in 2022. Thank you for our conversation.
Starkey: Ingmar, it’s been great talking with you. Thanks for the information and the opinions that you’ve shared with us. We wish you every success.
Van der Linden: Thanks.
Suggested Items
Meet the Author Podcast: Martyn Gaudion Unpacks the Secrets of High-Speed PCB Design
07/10/2025 | I-Connect007In this special Meet the Author episode of the On the Line with… podcast, Nolan Johnson sits down with Martyn Gaudion, signal integrity expert, managing director of Polar Instruments, and three-time author in I-Connect007’s popular The Printed Circuit Designer’s Guide to... series.
Intervala Hosts Employee Car and Motorcycle Show, Benefit Nonprofits
08/27/2024 | IntervalaIntervala hosted an employee car and motorcycle show, aptly named the Vala-Cruise and it was a roaring success! Employees had the chance to show off their prized wheels, and it was incredible to see the variety and passion on display.
KIC Honored with IPC Recognition for 25 Years of Membership and Contributions to Electronics Manufacturing Industry
06/24/2024 | KICKIC, a renowned pioneer in thermal process and temperature measurement solutions for electronics manufacturing, is proud to announce that it has been recognized by IPC for 25 years of membership and significant contributions to electronics manufacturing.
Boeing Starliner Spacecraft Completes Successful Crewed Docking with International Space Station
06/07/2024 | BoeingNASA astronauts Barry "Butch" Wilmore and Sunita "Suni" Williams successfully docked Boeing's Starliner spacecraft to the International Space Station (ISS), about 26 hours after launching from Cape Canaveral Space Force Station.
KIC’s Miles Moreau to Present Profiling Basics and Best Practices at SMTA Wisconsin Chapter PCBA Profile Workshop
01/25/2024 | KICKIC, a renowned pioneer in thermal process and temperature measurement solutions for electronics manufacturing, announces that Miles Moreau, General Manager, will be a featured speaker at the SMTA Wisconsin Chapter In-Person PCBA Profile Workshop.