-
- News
- Books
Featured Books
- pcb007 Magazine
Latest Issues
Current IssueInventing the Future with SEL
Two years after launching its state-of-the-art PCB facility, SEL shares lessons in vision, execution, and innovation, plus insights from industry icons and technology leaders shaping the future of PCB fabrication.
Sales: From Pitch to PO
From the first cold call to finally receiving that first purchase order, the July PCB007 Magazine breaks down some critical parts of the sales stack. To up your sales game, read on!
The Hole Truth: Via Integrity in an HDI World
From the drilled hole to registration across multiple sequential lamination cycles, to the quality of your copper plating, via reliability in an HDI world is becoming an ever-greater challenge. This month we look at “The Hole Truth,” from creating the “perfect” via to how you can assure via quality and reliability, the first time, every time.
- Articles
- Columns
- Links
- Media kit
||| MENU - pcb007 Magazine
Estimated reading time: 5 minutes
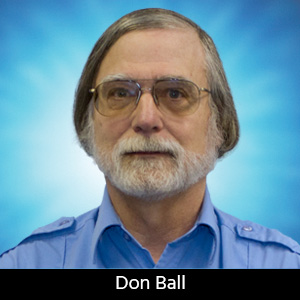
The Chemical Connection: Etch Uniformity and the Puddle Problem
Printed circuit board manufacturers who utilize wet processes have always strived to obtain a uniform etch across their panels. Although it is one of the most common matters these manufacturers tackle, it is perhaps the least understood. There are a few reasons for this, one of them being that there doesn’t seem to be an agreed-upon terminology within PCB manufacturing.
The term that I have been using to describe the consistency of etch across a single panel is “etch uniformity.” Sometimes this term can be equated to the consistency of etch across several panels, but perhaps a more suitable term is batch uniformity, which is directly related to how you maintain the chemical properties of your etchant. When it comes to etch uniformity, however, the factors that affect it can become complicated.
What are the obstacles to etch uniformity? There are two primary things that limit your ability to get a uniform etch: conveyor density and the “puddle effect.” Overall, the issues of etch uniformity stem from the idea that the etching reaction is drastically affected by diffusion and how quickly fresh etchant can contact the surface.
Conveyor Density
Conveyor density, in relation to wet processing equipment, can refer to how much space the wheels inside the processing chambers take up. To perform a conveyorized wet process, there needs to be enough open space to spray your panels. If you have too many conveyor wheels to move your panel, you are going to have a tougher time getting the etch rate you want. When it comes to etch uniformity on a single side of a panel, it is less about general conveyor density and more about the consistency of the wheel pattern. If you are trying to improve etch uniformity, this is not likely to be a concern unless someone running your machine decides to mess with the wheel placement, or if your wheels begin to deteriorate or warp from prolonged exposure to harsh chemicals. No matter what material your conveyor wheels are made of, they will eventually need to be replaced; how soon will depend on the material, the etchant used, and how often the machine is used.
If you are performing an etching process on both the top and bottom sides of a panel, conveyor density can also affect the overall uniformity. Since the bottom side of the conveyor will have more wheels than the topside, you will get different etch rates on both sides. This is because of the differing exposure and the pressure reduction caused by the wheels getting in the way.
Conveyor density is the primary limiting factor to etch uniformity and etch rate on the bottom side. The top side’s primary limiting factor is a completely different challenge of its own.
The Puddle Effect
The puddle effect is a phenomenon that occurs on the top side of a PCB during the etch process. This effect is caused by the accumulation of etchant on top of a panel while it is being sprayed in the etch chamber. This puddle becomes an obstacle to etch uniformity because it makes the center of the panel harder to etch than the sides. As you spray a panel, the moment the etchant contacts the copper, it becomes less effective since it has already reacted. In the middle of the panel, this accumulation can happen quickly because it is hard for the etchant to run off the sides (Figure 1). Even with oscillation sprays, it takes a lot of work to push etchant in the middle of the panel out to the sides where it can flow off. Thus, if you ever just etch a panel without anything to assist the etch uniformity, you will see the middle of the panel obtaining less etching compared to the edges. If you are trying to process large panels, this variation can become quite noticeable. This has become such an obstacle that often in discussions about etch uniformity, the focus is on ways to get around this puddle.
Figure 1: The puddle effect observed on the topside of a circuit board panel.
What makes this puddle challenging to get around is that this would be like trying to solve a complex fluid boundary layer problem. When you are spraying into a puddle, it may take a lot of pressure to break through and give enough push and turbulence to the surrounding fluid. What happens at this fluid-surface interface is what makes etch uniformity the least understood topic. Developing a mental model of this can get very complicated because of a variety of factors such as the nozzles used, oscillation rate, changing surface structure, spray tube flow rates, and many more. Often, changes in what seems to be the most intuitive solution do not provide much different results.
Although this puddle can be a significant obstacle, there is technology available for getting around it. In a future column, we will discuss the different technologies available, how they compare, and in what direction these etch uniformity solutions are heading.
How Can Changes in Etch Uniformity Affect PCB Manufacturing?
Improvements in etch uniformity technology could be a great boost to the PCB industry by allowing greater output from conveyorized systems and reduced error in manufacturing. If matters like the puddle effect could be negated, producers of printed circuit boards could make panels as large as they wish. Since it is a common practice to produce multiple smaller circuits from one panel, this change would greatly boost production and effectively make producing circuit boards at lesser cost.
Right now, the main hurdle to overcome is the puddle effect, but in the future, I foresee that the puddle effect will become less significant. With constant efforts to get around the puddle effect and improve the topside etch uniformity, we may get to a point where the topside uniformity becomes better than that on the bottom side. That is when new questions will arise. If top side etch uniformity becomes the new standard, how can we improve bottom side etch uniformity? Will changes in conveyor density be enough? If it is not, what will be the new limiting factors and how can we get overcome them?
This first column from Christopher Bonsell appears in the March 2022 issue of PCB007 Magazine.
More Columns from The Chemical Connection
The Chemical Connection: Sales Organization from a Capital Equipment PerspectiveThe Chemical Connection: Through-glass Vias in Glass Substrates
The Chemical Connection: Reducing Defects in Circuit Board Production
The Chemical Connection: Common Misconceptions in Wet Processing
The Chemical Connection: Surface Finishes for PCBs
The Chemical Connection: Earthquakes, Astronauts, and Aquatics—A Lighter Look at the Past
The Chemical Connection: Better Fabs Attract a Better Workforce
The Chemical Connection: Can Changing Spray Nozzles Improve My Etch Quality?