-
- News
- Books
Featured Books
- pcb007 Magazine
Latest Issues
Current IssueInventing the Future with SEL
Two years after launching its state-of-the-art PCB facility, SEL shares lessons in vision, execution, and innovation, plus insights from industry icons and technology leaders shaping the future of PCB fabrication.
Sales: From Pitch to PO
From the first cold call to finally receiving that first purchase order, the July PCB007 Magazine breaks down some critical parts of the sales stack. To up your sales game, read on!
The Hole Truth: Via Integrity in an HDI World
From the drilled hole to registration across multiple sequential lamination cycles, to the quality of your copper plating, via reliability in an HDI world is becoming an ever-greater challenge. This month we look at “The Hole Truth,” from creating the “perfect” via to how you can assure via quality and reliability, the first time, every time.
- Articles
- Columns
- Links
- Media kit
||| MENU - pcb007 Magazine
Estimated reading time: 5 minutes
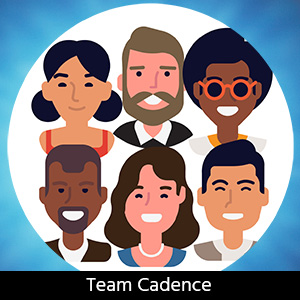
All Systems Go! Find and Fix Thermal PCB Problems Sooner Than Later
In an earlier column, Bridging the Gap Between Design and Analysis with In-Design Analysis, Brad Griffin discussed how the “shift left” that’s happening with electronic design means it is no longer sufficient for signal integrity (SI) and power integrity (PI) analysis to be performed in isolation. Designing, analyzing, and verifying the design in its entirety is key. Another facet of this shift left is the need to address thermal integrity (TI) sooner rather than later. In other words, finding and fixing thermal PCB design issues early in the design process is necessary to save costs, reduce design spins, and maintain your own sanity.
Electrothermal co-simulation—understanding the implications (intended or otherwise) of thermal interactions on electrical performance for high-speed (or high-frequency) PCB designs—is now essential for successful end-product development.
Let’s start by looking at things from the highest level, which is that we want to design a PCB. At some stage, this PCB (possibly accompanied by one or more additional PCBs) will be mounted in an enclosure. Eventually, this system will be deployed into the field. The designers of the PCB(s) and the system as a whole want to know how well the system will perform and how long it will survive.
A key factor that dramatically affects the life of electronic components and systems is temperature. Every aspect of a PCB generates some amount of heat. In addition to the components themselves, the combination of the currents flowing through the tracks and vias and the resistance of those tracks and vias results in voltage drops—what we call IR drops—and heat being generated. The reason why things get complicated is that resistance is a function of temperature. The higher the temperature, the higher the resistance and the greater the IR drop. Of course, the greater the IR drop, the greater the heat that’s generated and the higher the temperature. In the case of ICs, this feedback can lead to an uncontrollable increase in temperature called thermal runaway, which can result in a non-functioning IC.
All this explains why we perform thermal analysis in the first place. We can perform a simple 2D thermal analysis based on IR drops that assume a constant ambient temperature across the board. However, a full-blown 3D thermal analysis requires modeling the board in the context of the system—any other boards and the enclosure—which means it’s necessary to model the conduction, convention, and radiation of heat throughout the system. In turn, this means it’s necessary to account for things like heat sinks and fans, along with external heat sources (like the sun in the case of products intended for outside deployment, for example), and to model air flow inside and outside the system while understanding that the dynamics of this flow, and its capacity to remove heat, will be modified by the thermal environments it encounters.
Achieving all this requires a thermal analysis tool that can combine the finite element analysis (FEA) of solid structures with computational fluid dynamics (CFD) analysis for the air flowing around and through the system.
The trouble with a lot of PCB design environments is that their 3D thermal analysis is performed using tools designed for use by mechanical engineers. As a result, these tools don’t understand electrical structures like tracks and vias on the PCB as being electrical structures—the tools just see them as structures. Another aspect of this is that when the PCB design is brought over into the thermal verification environment, it is simplified in the process. Consequently, the thermal analysis tool isn’t provided with a 100% accurate view of things, and all it can do is report along the lines of, “This board is hot in this area,” without being able to provide specific context.
One result of this approach is that, even though many thermal issues originate as design problems, they aren’t discovered until it’s too late to modify the design. Unless you are prepared to push out your tapeout and delay time to market (TTM), the only option at this point is to implement some sort of thermal patch, such as adding a fan or a heatsink, which adds to the cost of the system. In some cases, like a radio unit (RU) on a 5G cellular network tower, adding a fan isn’t an option because it will generate electrical noise that will negatively impact the reception and transmission of radio signals.
What is required is for the PCB design environment to be supported by a 3D thermal analysis tool that’s designed with electrical and electronic engineers and systems in mind (not their mechanical cousins). This type of tool should inherently understand electrical structures like tracks, vias, and wirebonds. Furthermore, the tool should allow the PCB design to be dragged and dropped into the thermal analysis realm as-is without any simplifications or loss of data.
This type of environment also allows electrical engineers to create the initial version of the design while having a limited thermal vision, and to then pass the design to the thermal verification team to determine its detailed thermal performance. In turn, based on the tool’s knowledge of electrical structures, and in addition to spotting ICs that are running hot, the thermal verification team can identify thermal problems associated with specific vias and tracks and wirebonds. Identifying any thermal problems early in the design enables electrical engineers to perform early what-if analysis to determine how they can optimize the design while they are still in a position to do so, thereby avoiding costly and time-consuming design iterations or thermal patches.
Another significant advantage of having a 3D thermal analysis tool that’s designed from the ground up to support electrical and electronic designs is that it supports electrothermal co-simulation. This allows for the transient analysis of how things like temperatures and IR drops vary over time. In turn, this enables the verification of power and thermal mitigation strategies, such as using frequency scaling and voltage scaling to control the power being consumed—and the heat being generated—by a microprocessor or a microcontroller, for example. As the thermal analysis tool determines that the processor has reached a certain (high or low) temperature, it can cause the simulation tool to modify the processor’s frequency and/or voltage.
Having access to a PCB design and verification environment that includes a 3D thermal analysis tool designed from the ground up to support electrical and electronic designs—including the ability to perform electrothermal co-simulation—allows potential problems to be detected and fixed early in the development flow. This, in turn, reduces the number of design iterations and speeds robust, risk-free products to the market.
Melika Roshandell is a product management director for the Multiphysics System Analysis Group at Cadence.
Download The System Designer’s Guide to… System Analysis by Brad Griffin and the companion The Cadence System Design Solutions Guide. You can also view other titles in our full I-007e Book library here.
More Columns from All Systems Go
All Systems Go: Auto-Detecting Over- and Under-Derated PartsAll Systems Go: Time Traveling to 2030 for ML-Augmented PCB Design
All Systems Go: Accelerate Your PCB Designs with Machine Learning
All Systems Go: Can You Design Without Electronic Data Management?
All Systems Go! Supply Chain Woes—Which Comes First, the Design or the BOM?
All Systems Go! Ensuring Power Integrity—Explore, Design, and Verify
All Systems Go! Bridging the Gap Between Design and Analysis
All Systems Go! Meet Power Delivery Requirements Upfront with Power-First PCB Implementation