-
- News
- Books
Featured Books
- pcb007 Magazine
Latest Issues
Current IssueInventing the Future with SEL
Two years after launching its state-of-the-art PCB facility, SEL shares lessons in vision, execution, and innovation, plus insights from industry icons and technology leaders shaping the future of PCB fabrication.
Sales: From Pitch to PO
From the first cold call to finally receiving that first purchase order, the July PCB007 Magazine breaks down some critical parts of the sales stack. To up your sales game, read on!
The Hole Truth: Via Integrity in an HDI World
From the drilled hole to registration across multiple sequential lamination cycles, to the quality of your copper plating, via reliability in an HDI world is becoming an ever-greater challenge. This month we look at “The Hole Truth,” from creating the “perfect” via to how you can assure via quality and reliability, the first time, every time.
- Articles
- Columns
- Links
- Media kit
||| MENU - pcb007 Magazine
Estimated reading time: 5 minutes
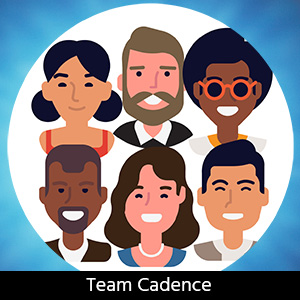
All Systems Go! Supply Chain Woes—Which Comes First, the Design or the BOM?
In an ideal world, when developing a PCB for an electronic product, decisions made during the design process should drive the bill of materials (BOM). We may think of this as an example of “the dog wagging the tail.” In the real world, however, there has always been some small amount of the BOM driving the design, which we may think of as “the tail wagging the dog.” A classic example of this is when an engineer’s calculations indicate the need for a resistor of 123 k?—a 40-cent part—while a 120 k? resistor—available for only 4 cents—will provide an almost identical response.
Current realities have made such BOM-driving-the-design decisions more inescapable to ensure product manufacturability. Everyone around the globe—from small companies to mega-enterprises with trillion-dollar valuations, all the way to the U.S. government—is currently facing unprecedented supply chain challenges. Supply chain optimization has long been under pressure, involving as it does a sophisticated balance of low cost, future availability, and product needs. While it’s true that difficulty obtaining all the components that are perfect for the task at hand is not totally unprecedented, alternative parts used to be plentiful. This meant that, even if you couldn’t get exactly what you wanted, you could get something similar. But with supply chain disruptions around the globe, even next-best parts are hard to find, making it critical to ensure component availability for the design.
Figure 1: A design with a rigid BOM requirement may result in an incomplete product.
One part of the solution is for everyone in the organization to have visibility with respect to stock levels. It’s important for this visibility to commence at the earliest stages of the design while the engineers are working on the initial high-level block diagram, thereby allowing for the design architecture to accommodate parts that can actually be sourced. You shouldn’t be relying on a spreadsheet that resides on the engineer’s desktop and is only updated and distributed by email “every now and then.” Stale information is no good to anyone. It shouldn’t be necessary for anyone to need to dig around to uncover the data they need. However, if given this information at the appropriate time, design solutions and workarounds are possible.
For example, you may be considering a certain component, only to discover this component is not currently available. There may be alternatives that are equivalent, or not as good, or better (some may say “overkill”). Take DDR4 memory, for example. It might be that you really require only an 8Gb DRAM for this version of the device. However, early in the design, you discover that it has a 30-week lead time, but 32Gb DRAMs are available in quantity. You could decide to add a few extra control signals to your design to enable this part, thereby allowing you to manufacture your product within an acceptable timeframe.
A similar approach may be employed with connectors. There may be a specific connector you wish to use that’s in short supply. You think you’re going to be all right... you’re sure you’re going to be all right… you know you’re going to be all right… but, there’s always the off-chance things will go pear-shaped. If you have the board real estate available, it may be a good idea to include footprints for both your preferred connector and an alternative that’s more easily sourced. Using this approach, in a worst-case scenario, you can ship the board populated with your backup connector and a conversion cable. Even if you never end up using it in production, you can at least bring the board up using the backup connector for the purposes of test and verification.
Adding no-load parts as a backup can be used in other situations too. Consider a function like an on-board power supply. Your options are to construct this function out of discrete parts or to purchase a pre-built module. If you have sufficient board real estate, you may decide to design both options in, thereby allowing you to change tack in the future if needed.
Figure 2: Allowing the BOM to drive the design helps mitigate supply chain woes.
Shortages and supply chain issues are not confined to components—they are also prevalent with respect to the materials used to fabricate the boards themselves. You may be okay with standard FR-4, but what is the situation with respect to something like FR408HR or even more specialized substrates? To determine the current state of play, it’s important to engage with your contract manufacturer (CM) or circuit board fab as early as possible in the design process so that they can guide you in your material selections. The board’s interfaces to the outside world are “set in stone,” but it may be possible to modify the internal implementation of the board. If the material you want won’t be available for 16 months, you might have to shorten the trace lengths to support an alternate dielectric, which may have higher dielectric losses at the rates you need to run at.
And, of course, it’s not just the board substrate itself. Other factors that could drive design changes may also need to be considered, such as the availability of the desired solder paste and finishes like immersion silver (IAg), immersion tin (ISn), electroless nickel immersion (ENIG), and organic solderability preservative (OSP).
Many of these changes may end up with a small incremental cost for the board, but it’s important to contrast this against the potential opportunity cost of millions of dollars in lost sales caused by the fact that you don’t have all the parts you need to complete the assembly.
The bottom line is that your design methodology should include a powerful and highly integrated product lifecycle management (PLM) capability. What is required is a tool that makes fresh data immediately available to everyone in the organization, so whenever buyers, engineers, and designers make changes, the others get to see those changes in real time, thereby allowing them to make decisions accordingly.
When it comes to allowing the BOM to drive your own designs, have you used any of the approaches presented here? More importantly, do you have any additional tips and techniques that you would care to share with the rest of us?
Nitin Bhagwath is director of product management, PCB front end at Cadence Design Systems.
Download The System Designer’s Guide to… System Analysis by Brad Griffin along with its companion book The Cadence System Design Solutions Guide. You can also view other titles in our full I-007e Book library here.
More Columns from All Systems Go
All Systems Go: Auto-Detecting Over- and Under-Derated PartsAll Systems Go: Time Traveling to 2030 for ML-Augmented PCB Design
All Systems Go: Accelerate Your PCB Designs with Machine Learning
All Systems Go: Can You Design Without Electronic Data Management?
All Systems Go! Find and Fix Thermal PCB Problems Sooner Than Later
All Systems Go! Ensuring Power Integrity—Explore, Design, and Verify
All Systems Go! Bridging the Gap Between Design and Analysis
All Systems Go! Meet Power Delivery Requirements Upfront with Power-First PCB Implementation