-
- News
- Books
Featured Books
- pcb007 Magazine
Latest Issues
Current IssueSales: From Pitch to PO
From the first cold call to finally receiving that first purchase order, the July PCB007 Magazine breaks down some critical parts of the sales stack. To up your sales game, read on!
The Hole Truth: Via Integrity in an HDI World
From the drilled hole to registration across multiple sequential lamination cycles, to the quality of your copper plating, via reliability in an HDI world is becoming an ever-greater challenge. This month we look at “The Hole Truth,” from creating the “perfect” via to how you can assure via quality and reliability, the first time, every time.
In Pursuit of Perfection: Defect Reduction
For bare PCB board fabrication, defect reduction is a critical aspect of a company's bottom line profitability. In this issue, we examine how imaging, etching, and plating processes can provide information and insight into reducing defects and increasing yields.
- Articles
- Columns
- Links
- Media kit
||| MENU - pcb007 Magazine
Estimated reading time: 4 minutes
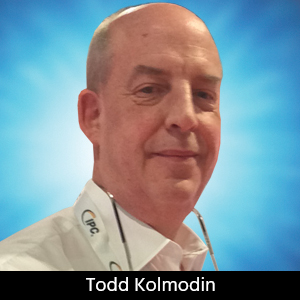
Testing Todd: Has Universal Fixture Testing Gone the Way of the Dodo?
Although flying probe testers have become commonplace in today’s manufacturing theatre, one must wonder if the fixture tester, specifically the universal grid or “pin in hole” fixture, has any valuable use in the electrical test arena. The advancements in flying probe technology are undisputed with the new abilities to do many of the tests that benchtop testing historically required. Flying probe testers can provide standard continuity tests, Hi-Pot, buried passives, inductance, impedance, and even IR testing. Many of these tests historically required hardware mock-ups to provide the footprint to administer these tests effectively.
Of course, the main advantage regarding flying probe testers is the cost. They provide lower capital investment while providing a large solution platform to many of today’s requirements. There are some who make the argument that flying probe testers remove the necessity of fixture testing altogether.
While this may be true to some extent, it is not altogether accurate. It can be argued that some of the earlier universal fixture solutions may be obsolete. For example, the earlier 1-inch and 2-inch pin-in-hole fixture solutions cannot provide test solutions for today’s complex designs. Density issues of modern designs don’t allow the use of headed pins. Historically, headed chisel pins were optimal for plated through-hole (PTH) probing, but were a hazard when direct-probing surface mount (SMT) pads. Over-compression of the fixture tester to the test fixture could cause damage to the SMT pad, ultimately scrapping the PCB. So, in that example some of the older fixture solutions may be obsolete.
However, we had to evolve. Headed chisel pins gave way to featureless music wire technology. These pins, either crimped or non-crimped, still allowed probing of PTH features while allowing a safer direct probe to SMT pads. These new pins also allowed direct probing of more complex designs while keeping the fixture to a single pass solution. This was a hindrance in the earlier headed pin designs, as complex designs required multiple passes (multiple fixtures) to accomplish the same result. This required extra drilling time and increased cost. Further, the headed chisel pins had a limitation to the size available. The newer featureless pins did not have such a limitation. Unfortunately, the caveat is that more guide plates are required to translate the pin successfully from the probe plate to the universal grid electronics. However, it can be argued that in the end the overall drilling time is insignificant, as you may still be using the same fixture drilling time to build the multi-pass headed pin fixture as you would to build the music wire single pass fixture. The hardware cost ultimately will be less as no redundancy testing is required with the single pass vs. the multi-pass fixture.
Now, with the fixture testers themselves, there are some challenges with the legacy universal grid machines. These machines typically presented a 0.100-inch grid configuration and had only one active test matrix. This only allowed single-side fixtures or wired clamshell combinations. Although still viable equipment, they present challenges when testing today’s PCBs. Double-sided universal grid machines with the 0.100-inch grid configurations are also still available through various aftermarket venues. These provide less costly alternatives but still can present challenges. Most universal grid testers used today are of the double-density or tighter grid configurations. These are better suitable for music wire fixtures and allow higher success rates for maintaining single-pass test solutions.
Now with that said, let’s get back to the question as to whether the universal fixture is dead. We know that flying probes can provide many solutions to today’s requirements. They can even provide automated tests that historically required fixtures, either universal or hard-wired. However, one very important aspect of the fixture tester vs. flying probe that will never be successfully met by the flying probe is providing “simultaneous test” of the PCB. What I mean here is the ability to stimulate or interrogate all nodes of the PCB at the same time. Flying probes use an “adjacency window” where isolation or shorts testing is done node-to-node based on the adjacency of one node or network to another. Other nodes or nets outside the adjacency window are not tested for shorts to that primary node. With fixture testers this isolation or shorts test is provided simultaneously to all nets to one another. Further, the continuity test on a flying probe, regardless of how many arms are available is only testing a finite number of nets at a time. The fixture tester will test them all at the same time. Yes, it’s still just the continuity test and both machines do the same thing, but the fixture tester does this all at once, giving it a major speed advantage.
The other significant item to note is that many aerospace, medical, and high reliability products have requirements that state, “Simultaneous test required.” This statement alone in a customer specification or procurement document negates the use of flying probe, period. There is no viable argument that a flying probe can provide a simultaneous test of all nets to one another in one single pass. Only the fixture tester with its full parametric test can provide this solution. Therefore, the fixture tester will live on. Whether it be a universal grid or wired dedicated, the simultaneous test will aways require a fixture tester of some flavor. Also, the fixture tester will always have the advantage in high volume applications. Although the flying probe has made electrical test costs significantly lower, it will never be able to compete in high volume theatres against tight deadlines. Long live the fixture.
This column originally appeared in the March 2022 issue of PCB007 Magazine.
More Columns from Testing Todd
Testing Todd: Why 4-wire Kelvin?Testing Todd: Why TDR?
Testing Todd: Positivity Boosts Employee Morale
Testing Todd: Preparing Employees for the Long Haul
Testing Todd: Where Can We Improve?
Testing Todd: Turning Into the Wind
Testing Todd: Coming Back to Life—Design Recovery
Testing Todd: Decision Time—Invest or Delegate?