-
- News
- Books
Featured Books
- pcb007 Magazine
Latest Issues
Current IssueSales: From Pitch to PO
From the first cold call to finally receiving that first purchase order, the July PCB007 Magazine breaks down some critical parts of the sales stack. To up your sales game, read on!
The Hole Truth: Via Integrity in an HDI World
From the drilled hole to registration across multiple sequential lamination cycles, to the quality of your copper plating, via reliability in an HDI world is becoming an ever-greater challenge. This month we look at “The Hole Truth,” from creating the “perfect” via to how you can assure via quality and reliability, the first time, every time.
In Pursuit of Perfection: Defect Reduction
For bare PCB board fabrication, defect reduction is a critical aspect of a company's bottom line profitability. In this issue, we examine how imaging, etching, and plating processes can provide information and insight into reducing defects and increasing yields.
- Articles
- Columns
- Links
- Media kit
||| MENU - pcb007 Magazine
Estimated reading time: 3 minutes
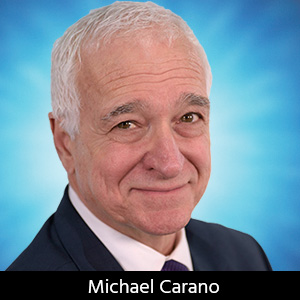
Contact Columnist Form
Trouble in Your Tank: Basic Fundamentals of Acid Copper Electroplating
Introduction
Electroplating a printed circuit board is by no means a trivial task. Higher layer counts, smaller diameter vias (through-hole and blind), as well as higher performance material sets contribute to the greater degree of difficulty with today’s technology. So, process engineers pay close attention to the “softer” issues such as cathode current density, solution chemistry (copper sulfate and sulfuric acid concentration), and—sometimes—addition agent control.
The concern here is that acid copper pattern plating of a printed circuit board has many critical aspects that must be diligently controlled for optimum performance. These include solution agitation and filtration, anode length and placement, current distribution effects, reducing electrical resistance in the plating cell, photoresist development, and controlled organic contamination in the plating solutions. More on these issues in a future column.
Yes, electroplating or electrodeposition, as some prefer, is a complex process. A review of the fundamentals is warranted.
In this month’s column, the intricacies of electrodeposition technology and its function of building up the thickness of copper in the holes and on the surface will be presented in detail. In this next series of columns, the function of the active ingredients in the copper plating solutions will be presented. Process control limits for the various plating solution components and the effects on deposit integrity will be discussed.
Understanding Plating Cell Resistances
While most engineers work diligently to control the chemical aspects of the electroplating process to ensure optimum throwing power (surface-to-hole ratio), they often overlook other critical parameters of the process. These include resistance through the cabling leading from the power supply to the plating cell, plating rack current-carrying capacity, and additional resistances within the cell. As it stands, electroplating is governed by Ohm’s Law: The greater the resistances within the plating cell, the more difficult it will be to achieve uniform plating thickness distribution. I like this analogy:
- Current flow (analogy) is likened to a flow of water through a hose
- Flow of water:
GPM = pressure divided by resistance
- In other words, the longer the hose or the smaller the diameter of the hose opening, the less water you will get
The same then can be said about current flow to the plating cell. Current is dependent on resistance and voltage. If resistances increase, the flow of current to the plating cell is reduced.
Thus, based on this analogy, I prefer to design the cell with minimal distance of the cables from the power to supply to the plating cell. In addition, the current carrying capacity of the cables is critical to achieve uniform current flow and to minimize current loss. If the cabling from the power supply (rectifier) to the cell feels “hot” to the touch, this is an indication that there is a loss of current reaching the cathode (circuit board). Figure 1 depicts the connections and solution resistances in the electroplating cell.
Understanding where these resistances are and finding opportunities to mitigate them will help improve plating distribution and throwing power especially in high aspect ratio through-holes.
The key takeaway from Figure 1 is that in addition to these various resistances in the cell, there is a voltage drop (IR drop) down the through-hole. The greater the resistance through the via, the less uniform the plating in the through-hole will be. Copper plating thickness does matter in terms of long-term reliability.
- IPC-6012 specification requires a minimum of 0.8 mils of plating in holes for Class 3 products. On thicker PCBs, this plating thickness may produce occasional problems with plated through-hole reliability.
- If the thickness is insufficient (especially in the center of the barrel of the through-hole), long term reliability with respect to lead-free assembly and harsh use environment (HUE) is compromised.
An example of lower copper thickness is shown in Figure 2.
The depiction in Figure 2 is somewhat common, particularly as boards become thicker and via diameters become smaller. However, that is no reason to throw up one’s hands and accept such a condition. There are ways to mitigate this issue and improve the throwing power even in complex high aspect ratio board designs. Ensuring sufficient copper plating thickness is critical to meet and exceed long-term reliability requirements.
More on this subject in my next column.
This column originally appeared in the March 2022 issue of PCB007 Magazine.
More Columns from Trouble in Your Tank
Trouble in Your Tank: Can You Drill the Perfect Hole?Trouble in Your Tank: Yield Improvement and Reliability
Trouble in Your Tank: Causes of Plating Voids, Pre-electroless Copper
Trouble in Your Tank: Organic Addition Agents in Electrolytic Copper Plating
Trouble in Your Tank: Interconnect Defect—The Three Degrees of Separation
Trouble in Your Tank: Things You Can Do for Better Wet Process Control
Trouble in Your Tank: Processes to Support IC Substrates and Advanced Packaging, Part 5
Trouble in Your Tank: Materials for PWB Fabrication—Drillability and Metallization