Dave Hillman on Living Your Passion
March 29, 2022 | Barry Matties, I-Connect007Estimated reading time: 3 minutes
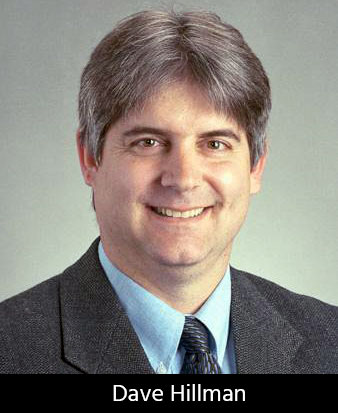
Barry Matties leads this engaging retrospective conversation with Dave Hillman, a Fellow, Materials and Process engineer at Collins Aerospace, who talks about mentorship, pandemic changes, and solder. “Soldering is soldering,” Dave says. “But how we do that keeps evolving in response to the new technologies and smaller packages.” What’s the key to his success and longevity? “Find your passion.” Here’s how he’s done it.
Barry Matties: Dave, you have been in the same position with the same company for nearly 40 years. That type of thing doesn’t even exist anymore.
Dave Hillman: I’ve been really privileged to be able to do so. We have a co-op program at Collins, and I’ve been able to mentor. We get four co-ops a year, two for spring/summer, and then two for summer/fall. About 150 kids to date. A lot of them now are industry colleagues, both in and outside Collins. It’s been fun to watch that transition, to watch them grow, to see the technology changing.
I think it’s interesting how my mentors have always talked about how big a shift it was from plated through-hole to surface mount and how that was revolutionary for the industry. Well, lead-free is doing the same thing. It’s challenging our material sets. What do you do? How do you get there? Collins is one of the few defense contractors that has been building lead-free for 10 years and it’s been very successful. I think the real trick is that we’re engineers. It’s a problem; go solve it.
Matties: Your expertise was in soldering, correct?
Hillman: Correct. I attended Iowa State University for my bachelor’s, then went back 10 or 15 years later for my master’s. I function as the soldering subject matter expert in terms of metallurgy, alloys and processes, troubleshooting, that sort of thing. It’s been a lot of fun. Our industry seems to like to replay the lessons of the past; gold embrittlement is probably this sexiest topic ever on the planet because we just keep talking about it.
Matties: One of the things that we hear constantly is that field defects primarily come down to the solder and solder joints. As an expert, would you validate that statement?
Hillman: I do. If you don’t want defects, it comes down to making sure a design is producible. For instance, why would you have three different product design teams that are using the same part with three different footprints? You don’t need three footprints. You need one footprint because for the manufacturing guys that will be efficiency on their end and uniformity in the solder joints.
As my friend Doug Pauls would say, you can design the most beautiful thing on the planet, but if you can’t build it, what good is it? This industry no longer designs something, then throws it over the wall. Nowadays, the design teams and the manufacturing teams are very much connected.
Matties: With the soldering process, there are a lot of ways it can go wrong.
Hillman: I think it’s interesting that we had this huge drive for “just in time,” “no WIP,” and “keep your inventory low.” Then COVID hits and suddenly we don’t have anything in stock. We have no security backup. That “just in time” philosophy works when things are coming together as planned. I think we all underrated how critical it is to a process.
Matties: We’re seeing a new trend in how we’re melting solder as opposed to the traditional reflow processes. How do you view these new technologies in terms of market acceptability and performance?
Hillman: I remember my mentors telling me early in my career, “Here’s the wave solder machine, but don’t pay much attention to it. It’ll be gone in about five, six years. We’re not using it very much.” Yet, we still have wave solder. Our soldering processes have evolved to deliver what’s needed.
To read this entire conversation, which appeared in the March 2022 issue of SMT007 Magazine, click here.
Suggested Items
BEST Inc. Introduces StikNPeel Rework Stencil for Fast, Simple and Reliable Solder Paste Printing
06/02/2025 | BEST Inc.BEST Inc., a leader in electronic component rework services, training, and products is pleased to introduce StikNPeel™ rework stencils. This innovative product is designed for printing solder paste for placement of gull wing devices such as quad flat packs (QFPs) or bottom terminated components.
See TopLine’s Next Gen Braided Solder Column Technology at SPACE TECH EXPO 2025
05/28/2025 | TopLineAerospace and Defense applications in demanding environments have a solution now in TopLine’s Braided Solder Columns, which can withstand the rigors of deep space cold and cryogenic environments.
INEMI Interim Report: Interconnection Modeling and Simulation Results for Low-Temp Materials in First-Level Interconnect
05/30/2025 | iNEMIOne of the greatest challenges of integrating different types of silicon, memory, and other extended processing units (XPUs) in a single package is in attaching these various types of chips in a reliable way.
E-tronix Announces Upcoming Webinar with ELMOTEC: Optimizing Soldering Quality and Efficiency with Robotic Automation
05/30/2025 | E-tronixE-tronix, a Stromberg Company, is excited to host an informative webinar presented by Raphael Luchs, CEO of ELMOTEC, titled "Optimize Soldering Quality and Efficiency with Robotic Automation," taking place on Wednesday, June 4, 2025 at 12:00 PM CDT.
CE3S Launches EcoClaim Solutions to Simplify Recycling and Promote Sustainable Manufacturing
05/29/2025 | CE3SCumberland Electronics Strategic Supply Solutions (CE3S), your strategic sourcing, professional solutions and distribution partner, is proud to announce the official launch of EcoClaim™ Solutions, a comprehensive recycling program designed to make responsible disposal of materials easier, more efficient, and more accessible for manufacturers.