-
- News
- Books
Featured Books
- pcb007 Magazine
Latest Issues
Current IssueThe Hole Truth: Via Integrity in an HDI World
From the drilled hole to registration across multiple sequential lamination cycles, to the quality of your copper plating, via reliability in an HDI world is becoming an ever-greater challenge. This month we look at “The Hole Truth,” from creating the “perfect” via to how you can assure via quality and reliability, the first time, every time.
In Pursuit of Perfection: Defect Reduction
For bare PCB board fabrication, defect reduction is a critical aspect of a company's bottom line profitability. In this issue, we examine how imaging, etching, and plating processes can provide information and insight into reducing defects and increasing yields.
Voices of the Industry
We take the pulse of the PCB industry by sharing insights from leading fabricators and suppliers in this month's issue. We've gathered their thoughts on the new U.S. administration, spending, the war in Ukraine, and their most pressing needs. It’s an eye-opening and enlightening look behind the curtain.
- Articles
- Columns
- Links
- Media kit
||| MENU - pcb007 Magazine
Developments in Low-Loss Substrates for High-Frequency Applications
March 29, 2022 | Alun Morgan, Ventec International GroupEstimated reading time: 2 minutes
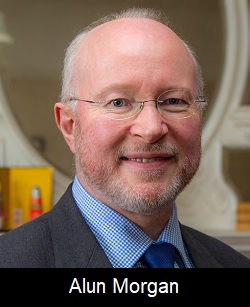
The electronics industry as we know it today can trace its birth to the creation of the first integrated circuit in 1958, although conception occurred 10 years earlier with the invention of the transistor. That first IC contained a single transistor and four passive components. To say things have come a long way since then is a huge understatement.
Only one thing may have matched the meteoric pace of progress in our industry—market expectation. Exponential advancement has become the norm, and this is now achieved through an aggregation of improvements, rather than a large leap in one aspect such as chip lithography (Moore’s Law), or processor frequency scaling (Dennard).
It’s a small step from acknowledging this reality to adopting a holistic view that acknowledges the contribution each aspect of the system can make toward the overall performance and that seeks to optimize the interactions between them. Accordingly, in cutting-edge applications, we no longer have the luxury of treating the PCB as merely a medium for mounting and connecting components. At high signal speeds in particular, the properties of the substrate, copper foil, and trace geometries govern whether the system can deliver the required performance.
Many within the industry already understand that the PCB has become a high-tech component in itself, particularly those departments working on applications in automotive radar, 5G, and satellite communications at multi-gigahertz frequencies.
Low-Loss Substrates
These applications are operating close to the limits of the capabilities typical materials can offer. Resistive loss mechanisms, including the skin effect in copper conductors and dielectric losses due to the molecular dipole moment in the insulating substrate need to be understood and carefully managed. The cumulative effect of the tiny losses in signal energy and associated thermal dissipation incurred with every signaling transition becomes appreciable. If not properly addressed, these losses demand more powerful transmitters, more sensitive receivers, and extra thermal management than are practicable within the typical constraints on power, as well as size, weight, and cost that usually prevail.
There are growing demands for low-loss substrates to address high-performance systems, spanning applications from high-end servers and telecom infrastructure all the way to mmWave 5G, satellite, and radar applications.
By enhancing aspects of PCB laminates, it has been possible to produce low-loss substrates that can handle demanding applications in data centers and telecom switches, for example. Optimizing the fiber weave effectively minimizes micro-variabilities in signal-path characteristics that cause distortions such as signal skew, which ultimately give rise to excessive noise and signaling errors. Attributes such as drilling performance and resistance to CAF (conductive anodic filament) formation are also improved.
For applications operating at the highest frequencies in use today, ceramic-filled and PTFE-based materials are achieving the lowest loss factors in the industry. The molecular structure of PTFE (polytetrafluoroethylene) arranges fluorine atoms as spirals around the carbon backbone to create a rod-like stiff cylindrical shape that has no dipole moment. This absence of any dipole moment negates the oscillations set up in conventional substrate dielectrics due to repeated polarization caused by signal current. This is manifested as an extremely low dissipation factor (Df) that helps to reduce signal losses.
To read this entire article, which appeared in the March 2022 issue of PCB007 Magazine, click here.
Suggested Items
I-Connect007 Editor’s Choice: Five Must-Reads for the Week
07/11/2025 | Andy Shaughnessy, Design007 MagazineThis week, we have quite a variety of news items and articles for you. News continues to stream out of Washington, D.C., with tariffs rearing their controversial head again. Because these tariffs are targeted at overseas copper manufacturers, this news has a direct effect on our industry.I-Connect007 Editor’s Choice: Five Must-Reads for the Week
Digital Twin Concept in Copper Electroplating Process Performance
07/11/2025 | Aga Franczak, Robrecht Belis, Elsyca N.V.PCB manufacturing involves transforming a design into a physical board while meeting specific requirements. Understanding these design specifications is crucial, as they directly impact the PCB's fabrication process, performance, and yield rate. One key design specification is copper thieving—the addition of “dummy” pads across the surface that are plated along with the features designed on the outer layers. The purpose of the process is to provide a uniform distribution of copper across the outer layers to make the plating current density and plating in the holes more uniform.
Trump Copper Tariffs Spark Concern
07/10/2025 | I-Connect007 Editorial TeamPresident Donald Trump stated on July 8 that he plans to impose a 50% tariff on copper imports, sparking concern in a global industry whose output is critical to electric vehicles, military hardware, semiconductors, and a wide range of consumer goods. According to Yahoo Finance, copper futures climbed over 2% following tariff confirmation.
Happy’s Tech Talk #40: Factors in PTH Reliability—Hole Voids
07/09/2025 | Happy Holden -- Column: Happy’s Tech TalkWhen we consider via reliability, the major contributing factors are typically processing deviations. These can be subtle and not always visible. One particularly insightful column was by Mike Carano, “Causes of Plating Voids, Pre-electroless Copper,” where he outlined some of the possible causes of hole defects for both plated through-hole (PTH) and blind vias.
Trouble in Your Tank: Can You Drill the Perfect Hole?
07/07/2025 | Michael Carano -- Column: Trouble in Your TankIn the movie “Friday Night Lights,” the head football coach (played by Billy Bob Thornton) addresses his high school football team on a hot day in August in West Texas. He asks his players one question: “Can you be perfect?” That is an interesting question, in football and the printed circuit board fabrication world, where being perfect is somewhat elusive. When it comes to mechanical drilling and via formation, can you drill the perfect hole time after time?