-
-
News
News Highlights
- Books
Featured Books
- pcb007 Magazine
Latest Issues
Current IssueSales: From Pitch to PO
From the first cold call to finally receiving that first purchase order, the July PCB007 Magazine breaks down some critical parts of the sales stack. To up your sales game, read on!
The Hole Truth: Via Integrity in an HDI World
From the drilled hole to registration across multiple sequential lamination cycles, to the quality of your copper plating, via reliability in an HDI world is becoming an ever-greater challenge. This month we look at “The Hole Truth,” from creating the “perfect” via to how you can assure via quality and reliability, the first time, every time.
In Pursuit of Perfection: Defect Reduction
For bare PCB board fabrication, defect reduction is a critical aspect of a company's bottom line profitability. In this issue, we examine how imaging, etching, and plating processes can provide information and insight into reducing defects and increasing yields.
- Articles
- Columns
- Links
- Media kit
||| MENU - pcb007 Magazine
Additive Design: Same Steps, Different Order
April 12, 2022 | I-Connect007 Editorial TeamEstimated reading time: 2 minutes
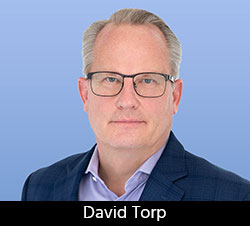
We recently spoke with Dave Torp, CEO of Winonics, about the company’s additive and semi-additive processes and what PCB designers need to know if they’re considering designing boards with these new technologies. As Dave explains, additive design is not much different from traditional design, but the steps in the design cycle are out of order, and additive designers must communicate with their fabricators because so much of the new processes are still proprietary.
Andy Shaughnessy: Dave, give us some background on Winonics and your focus on additive and semi-additive processes.
Dave Torp: Additive Circuits Technologies is the parent company, which owns two companies. One is Winonics, a rigid circuit board company. The other is a flexible circuit board company called Bench 2 Bench. Winonics is ISO-9001, AS 9100, and ITAR-registered. We have a 52,000 square-foot facility in Brea, California. Bench 2 Bench has a 25,000 square-foot facility, located about 10 minutes away in Fullerton.
From the holistic view, our focus is in the high-reliability electronics market. We focus on the aerospace, defense, and the medical device electronics. Our competitive anchor is providing great service. We don’t really put too many boundaries on what we do. Simply put, we’re a technology realization company.
We have process patents for applying circuitry and metallization in an additive technology. We also have some trade secrets that we keep behind the vest with respect to our manufacturing operations. What the additive technology enables is ultra-fine features and ultra-high definition. The enabling technology provides metallization in very high-density configurations to make high-density interconnects. We have demonstrated the technology down to 15-micron lines and spaces, which was, at the time, the limit of the laser technology that we had.
As the LDI technology becomes more precise, we’ll have the ability to go further down that pathway. So, we look to being capable of doing 8-micron lines and spaces and below by 2023.
The real drivers for the technology are miniaturization and the need for greater speed. If you look at some of the frequencies that are required to enable a communication, you are getting up into the 5G-plus mindset. The layer counts within the circuit boards aren’t increasing, but the number of interconnects between those layers is increasing. You can have a lot of fun with respect to the layers that are being interconnected and how the microvias are being stacked and racked upon each other. Sometimes you stack them right on top of each other. Other times, you stagger them out a little bit, depending on the signal integrity that you want.
With respect to the additive processes, first we have semi-additive technology, which is a fairly new process. In a lot of cases, you take the ultra-thin copper foils, or the plating applied to the substrate. You hit it with photo-sensitive materials, etch away that ultra-thin part of the copper, and then start to plate back up. That’s the semi-additive process.
The fully additive process is the newest technology, where you print the pattern that you want on the substrate without copper foil, using a palladium or platinum-based chemistry, and expose it with a laser or a UV source of radiation. Then you allow the electroless copper plating to be deposited, followed by electrolytic plating
This allows us to create ultra-fine traces down to sub-15-micron type technology. We’re excited about the opportunities, especially in the in-betweens, where you’re using hybrid interposer layers to try to connect this heterogeneous integrated package together.
To read this entire conversation, which appeared in the April 2022 issue of Design007 Magazine, click here.
Testimonial
"The I-Connect007 team is outstanding—kind, responsive, and a true marketing partner. Their design team created fresh, eye-catching ads, and their editorial support polished our content to let our brand shine. Thank you all! "
Sweeney Ng - CEE PCBSuggested Items
Statement from the Global Electronics Association on the July 2025 Tariff on Copper Foil and Electronics-Grade Copper Inputs
07/31/2025 | Global Electronics AssociationWe are disappointed by today’s decision to impose a 50% tariff on imported copper foil and other essential materials critical to electronics manufacturing in the United States.
Considering the Future of Impending Copper Tariffs
07/30/2025 | I-Connect007 Editorial TeamThe Global Electronics Association is alerting industry members that a potential 50% tariff on copper could hit U.S. electronics manufacturers where it hurts.
Connect the Dots: Sequential Lamination in HDI PCB Manufacturing
07/31/2025 | Matt Stevenson -- Column: Connect the DotsAs HDI technology becomes mainstream in high-speed and miniaturized electronics, understanding the PCB manufacturing process can help PCB design engineers create successful, cost-effective designs using advanced technologies. Designs that incorporate blind and buried vias, boards with space constraints, sensitive signal integrity requirements, or internal heat dissipation concerns are often candidates for HDI technology and usually require sequential lamination to satisfy the requirements.
OKI Launches Rigid-Flex PCBs with Embedded Copper Coins Featuring Improved Heat Dissipation for Space Equipment Applications
07/29/2025 | BUSINESS WIREOKI Circuit Technology, the OKI Group’s printed circuit board (PCB) business company, has developed rigid-flex PCBs with embedded copper coins that offer improved heat dissipation for use in rockets and satellite-mounted equipment operating in vacuum environments.
Designers Notebook: Basic PCB Planning Criteria—Establishing Design Constraints
07/22/2025 | Vern Solberg -- Column: Designer's NotebookPrinted circuit board development flows more smoothly when all critical issues are predefined and understood from the start. As a basic planning strategy, the designer must first consider the product performance criteria, then determine the specific industry standards or specifications that the product must meet. Planning also includes a review of all significant issues that may affect the product’s manufacture, performance, reliability, overall quality, and safety.