-
- News
- Books
Featured Books
- pcb007 Magazine
Latest Issues
Current IssueInventing the Future with SEL
Two years after launching its state-of-the-art PCB facility, SEL shares lessons in vision, execution, and innovation, plus insights from industry icons and technology leaders shaping the future of PCB fabrication.
Sales: From Pitch to PO
From the first cold call to finally receiving that first purchase order, the July PCB007 Magazine breaks down some critical parts of the sales stack. To up your sales game, read on!
The Hole Truth: Via Integrity in an HDI World
From the drilled hole to registration across multiple sequential lamination cycles, to the quality of your copper plating, via reliability in an HDI world is becoming an ever-greater challenge. This month we look at “The Hole Truth,” from creating the “perfect” via to how you can assure via quality and reliability, the first time, every time.
- Articles
- Columns
- Links
- Media kit
||| MENU - pcb007 Magazine
Estimated reading time: 4 minutes
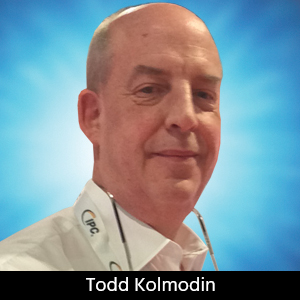
Testing Todd: Optimize Your Training Time
Today’s training has become an essential part of any operation, especially because most quality management systems (QMS) require this. To be compliant with ISO 9001 you must maintain a competence and training system. However, there are a few things to keep in mind when taking on the competence and training mission.
Too many times you just hire the new employee, give them some work instructions and practical training, document their completion, and that’s it. Unfortunately, this can lead to many problems, and here is why.
Assigning Employee Instruction
First, you must make sure the process or work instruction is robust. Too many times a process or work instruction is assigned to a person, usually a quality engineer or technician, or possibly the manager of the department, cell, or manufacturing unit. This is a problem, as that person may quit, move to another department, or otherwise become unavailable; the process is now orphaned. So, a process or work instruction should be assigned to a department and not a person. Therefore, it is always a task for the department.
Next, the building of the work instruction based on a documented process should not be a solo activity. Many times, the document is written by a third party or technical writer that has no real familiarity with the task being documented. This leads to process anomalies. Of course, a new machine or process may be assigned to a technical team to get the machine online and document the operation of said machine. But it cannot stop there. Line operators should be involved in the documentation process. They are the ones who will be performing the task daily. The overall operation of the machine or process is to provide a goal, which may be a product, part, or combination thereof. Just documenting how to run the machine is not sufficient. For the work instruction and process to work cohesively, we must combine the task with the surrounding environment, tools, and space. This requires looking at it from a higher level.
To begin with, we must evaluate the space. Is the machine or tool placed efficiently? Are there any hazards due to the installation? These could be:
- Tripping hazards
- Crush or pinch hazards
- Ergonomic hazards
One thing that is overlooked when installing new processes and/or equipment is the impact the work area has on the success of the process. If we don’t look at these things, we are creating waste. In this context I do not mean waste or scrap of the product but the waste of time due to poor planning of the space.
We need to look at items such as:
- Tools required for the task
- Movements the operator must make
- Travel if the operator must move the product to and from the machine
- Health and safety such as lifting and twisting, if so applicable
This is where the importance of combining the process or work instruction with efficient development of the workspace or cell comes in. Another important aspect is to optimize the workspace so that it only contains the tools and supplies needed for the task. Get rid of everything else which serves no purpose and just creates clutter.
Time to Test
Here is where involving an operator-level employee benefits the overall success. Once the process or work instruction is documented, it must be tested. Go through the steps one by one to validate the necessity. You will find that some of your requirements may be dumb. During this evaluation you will be able to optimize the steps, validate the ergonomics of the area, and streamline movements to achieve the best possible outcome.
It is only after this is complete that you can effectively train your workforce. They will learn the task based on optimal efficiency and the repeatability will be higher than that of a loose or messy process. The thing is, if you leave holes or gaps in a process, your operators will find the shortcuts or ways to deviate from the intended task. Having a robust and tested process, as well as work instruction, will keep this behavior to a minimum.
Now that we have our employees trained, we need to document this to be compliant to the QMS. Many times, we train the employees, document their file as trained, cut them loose, and they disappear into the abyss. Well, that doesn’t work either. Once the employee is trained and documented, they need to be reviewed on a regular basis. Most common is an annual review. This ensures they are still performing the task correctly and/or have improved or degraded since last review. Because the QMS needs to be reviewed at least yearly, it gives the department an opportunity to review the process as well. Perhaps the machine was upgraded. Perhaps there is an obsolete step or a new one required. This is all part of the overall continuity between the process, work instruction, and employees performing the tasks.
Conclusion
The process must be designed optimally, including workspace, tools, and ergonomics. In today’s times, efficiency, repeatability, and the minimization of waste is crucial. When processes and work instructions are “in tune” the ability to efficiently increase productivity and quality will quickly become apparent.
This column originally appeared in the April 2022 issue of PCB007 Magazine.
More Columns from Testing Todd
Testing Todd: Why 4-wire Kelvin?Testing Todd: Why TDR?
Testing Todd: Positivity Boosts Employee Morale
Testing Todd: Preparing Employees for the Long Haul
Testing Todd: Where Can We Improve?
Testing Todd: Turning Into the Wind
Testing Todd: Coming Back to Life—Design Recovery
Testing Todd: Decision Time—Invest or Delegate?