-
- News
- Books
Featured Books
- pcb007 Magazine
Latest Issues
Current IssueInventing the Future with SEL
Two years after launching its state-of-the-art PCB facility, SEL shares lessons in vision, execution, and innovation, plus insights from industry icons and technology leaders shaping the future of PCB fabrication.
Sales: From Pitch to PO
From the first cold call to finally receiving that first purchase order, the July PCB007 Magazine breaks down some critical parts of the sales stack. To up your sales game, read on!
The Hole Truth: Via Integrity in an HDI World
From the drilled hole to registration across multiple sequential lamination cycles, to the quality of your copper plating, via reliability in an HDI world is becoming an ever-greater challenge. This month we look at “The Hole Truth,” from creating the “perfect” via to how you can assure via quality and reliability, the first time, every time.
- Articles
- Columns
- Links
- Media kit
||| MENU - pcb007 Magazine
Estimated reading time: 5 minutes
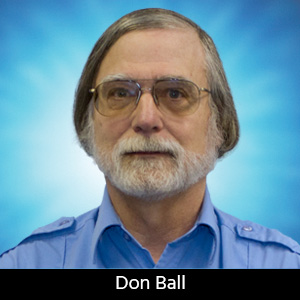
The Chemical Connection: The Case for Preventive Maintenance
Preventive maintenance (PM) is a routine maintenance performed to ensure equipment runs efficiently and won’t experience problems any time soon. This routine maintenance can become highly important when you are running a business that relies heavily on equipment for production. Printed circuit board (PCB) shops are no exception to this because their production is dependent on many different complex machines working together.
Although PM is critical, a large portion of PCB shops don’t have a PM program. Far too often, manufacturers will wait until a machine starts to experience problems before they act. This behavior is likely because PM can sound like a tedious and costly task. The truth is that the benefits of PM heavily outweigh the drawbacks. In fact, having a PM program can even give you an edge over PCB shops that don’t. Here’s how.
Machine Longevity
Starting a PCB shop requires a large investment in many different pieces of equipment, so why not make the most of each machine you have? With a PM program, you can drastically extend the life of your equipment. This is because often there is a domino effect when it comes to wear and tear on machine parts. Once a part becomes damaged, it can cause severe damage to your machine if left unchecked. A PM program prevents this domino effect by finding the damaged part before it goes on to affect others.
A PM program to improve your machine’s lifespan involves checking the conditions of conveyor components, heating and cooling units, and general equipment cleanliness as well as verifying all system components and controls are calibrated. Even keeping your machine clean is a form of PM that can go a long way toward ensuring your equipment stays in shape.
Shop Safety
When it comes to safety in a PCB shop, containment of the corrosive and toxic chemicals from the wet processing end is key. With a PM program, you can reduce the number of unexpected leaks and spills that occur. Containment of the chemistry serves two purposes for safety. First and foremost, it prevents your employees from having direct exposure to the chemistry. Second, it prevents deterioration of equipment. Sometimes equipment can corrode to the point where dangerous components, like electrical and mechanical components, can become exposed and open the opportunity to seriously harm someone.
PM for containment would involve inspections of plumbing, seals, ventilation, and containment trays. A PM program would also involve ensuring that the materials involved in your processes are still chemically compatible. This is a good practice because nearly all materials will eventually experience some form of damage when exposed to the chemicals used for PCB processing. Performing this check will also be useful because sometimes employees will need to swap out parts. If the employee isn’t aware or careful enough, an incompatible material could be introduced to the machine and cause a potential spill or leak. Etching and stripping machines, for example, can have very similar parts. Although the parts seem similar, they are often made of different materials because the chemistry that they need to withstand inside these machines are widely different. Since their parts look alike, they can be easily mixed up if one is not careful. In these kinds of scenarios, you won’t see an immediate change, but after a few days or weeks you may start to notice some impact. If a leak or spill is not caught, it can worsen over time.
Equipment Efficiency
Having a PM program can also help maintain your equipment’s efficiency. Depending on the equipment, whether it’s a wet or dry process, there will be different factors that will affect efficiency.
Wet processing equipment requires you to be wary of the by-products you are creating. Over time, these by-products will build up within your machine and reduce the efficiency of your solution and potentially cause problems with your filtration and nozzles. By-products or contaminants are best removed on a frequent basis. If they are allowed to significantly accumulate, you risk damaging your machine and you will have difficulty removing them. PM to maintain efficiency in wet processing equipment will generally consist of changing out the filters, cleaning spray nozzles, and performing titrations to get a sense of what state your chemistry is in.
In the dry process equipment, the concern mostly comes down to cleanliness. Since the efficiency of the dry processes, laminating, and exposing depend on how effective your cleanroom is; most of the PM is about maintaining the cleanroom’s quality. This can mean cleaning it to ensure no trace particles are brought in and checking the air filtration system.
Production Reliability
If you are running a PCB fabrication facility, you want to consistently manufacture products. By maintaining a PM program, you won’t have to worry about emergency maintenance and unexpected downtime. PM will keep you on the same page with your machines and allow you to diagnose problems before they escalate into bigger problems. Having unexpected downtime can be very costly. When you need to perform emergency maintenance, you first need to take time to diagnose the problem. If you haven’t been carefully keeping track of your machine’s condition, it can take many hours to find the root cause of the problem. Even if you find something that is going wrong, it could be unrelated to what caused you to shut the machine down in the first place. Once you find the root cause, chances are you will need to replace a part. If you don’t already have the part you need, you must order it from your equipment supplier. Depending on your equipment manufacturer and the part you need, the time it takes for you to receive it will vary. This will result in more wasted time that could have been prevented. With PM, you would at least be able to foresee problems like this and order the part earlier or maintain a better inventory of parts.
Without a doubt, a PM program can greatly benefit your PCB shop. As a PCB manufacturer, it is highly recommended that you do the best you can to maintain some form of PM—even if that means just performing routine cleanings. Any amount of PM is better than no PM. Some companies that manufacture PCB equipment do offer PM programs where they will schedule a time for a technician to visit and perform PM; some may even help you develop your own PM program. Therefore, if you are considering a PM program, it is highly recommended that you reach out to your equipment manufacturer(s) and ask about PM options.
This column originally appeared in the April 2022 issue of PCB007 Magazine.
More Columns from The Chemical Connection
The Chemical Connection: Sales Organization from a Capital Equipment PerspectiveThe Chemical Connection: Through-glass Vias in Glass Substrates
The Chemical Connection: Reducing Defects in Circuit Board Production
The Chemical Connection: Common Misconceptions in Wet Processing
The Chemical Connection: Surface Finishes for PCBs
The Chemical Connection: Earthquakes, Astronauts, and Aquatics—A Lighter Look at the Past
The Chemical Connection: Better Fabs Attract a Better Workforce
The Chemical Connection: Can Changing Spray Nozzles Improve My Etch Quality?