-
- News
- Books
Featured Books
- smt007 Magazine
Latest Issues
Current IssueWhat's Your Sweet Spot?
Are you in a niche that’s growing or shrinking? Is it time to reassess and refocus? We spotlight companies thriving by redefining or reinforcing their niche. What are their insights?
Moving Forward With Confidence
In this issue, we focus on sales and quoting, workforce training, new IPC leadership in the U.S. and Canada, the effects of tariffs, CFX standards, and much more—all designed to provide perspective as you move through the cloud bank of today's shifting economic market.
Intelligent Test and Inspection
Are you ready to explore the cutting-edge advancements shaping the electronics manufacturing industry? The May 2025 issue of SMT007 Magazine is packed with insights, innovations, and expert perspectives that you won’t want to miss.
- Articles
- Columns
- Links
- Media kit
||| MENU - smt007 Magazine
VJ Electronix: Automating the X-ray Inspection Process
May 4, 2022 | Nolan Johnson, I-Connect007Estimated reading time: 2 minutes
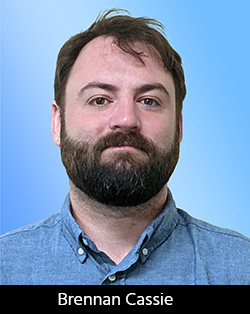
Brennan Caissie shares the benefits of a new inspection tool that can be used on a variety of boards, with an automated system that takes the pressure off the manufacturing floor operators and can provide feedback all the way to the design process.
Nolan Johnson: Brennan, can you explain what you do as an applications engineer?
Brennan Caissie: Yes. I interact with customers, working with them to find their needs, translate that back to our engineering group and come up with solutions for customer applications. VJ Electronix specializes in X-ray inspection, X-ray counting for components, and rework machines.
Johnson: You have some news coming out of VJE about some new products. Could you fill us in?
Caissie: Sure. We have a new product coming out called the Apogee 90, which is a 90-kiloVolt PCB inspection machine. The Apogee 90 is primarily aimed at customers generating consumer electronics, medical components, products with smaller and lighter boards. This machine is going to have some software capabilities that are new for us. There’s BGA analysis, for example. We also have some automated filters and automated inspection routines. We can tilt the detector in the machine to get angled images. There are quite a few new features we are bringing to this machine.
Johnson: Angled images? In that regard, are you starting to rely on more than just 2D contrast for identification? Are you starting to use a little bit of a 3D angle at this?
Caissie: That’s right. It’s not quite 3D, but more than a top-down 2D image. We can tilt the detector in the machine up to 45 degrees so we can get an angled image so you can see the top and bottom of structures like vias, to see exactly where the solder is placed in three dimensions.
Johnson: What’s the advantage to these angled images?
Caissie: In boards where you have multiple layers, it is sometimes helpful to look inside through-holes and vias just to see if the solder is completely filling those areas with no voids in the solder.
Johnson: The additional angles certainly help you get a more complete picture of what’s going on there.
Caissie: That’s right. You can also use that feature to look around some tall components that might be blocking your view. You can angle the detector to see around those types of components as well.
Johnson: You have some capabilities within the Apogee to handle some different types of boards. What makes that challenging? Why does that require you to do something different?
Caissie: We have a 90-kiloVolt system, which is good for smaller, thinner boards. When you get into the larger boards with multiple layers, it does get a little more difficult for that X-ray to penetrate all the way through. We have a 130-kiloVolt version coming that will be more appropriate for those types of applications.
Johnson: Because of the board type, you need to optimize. One system is not going to work for every board thickness.
Caissie: That’s right. We typically use the higher power system for applications like server boards and automotive components. Those thicker boards are going to require more power to penetrate through those boards to see all the different layers.
This interview originally appeared in the May issue of SMT007 Magazine. Click here to continue reading.
Suggested Items
Driving Innovation: Direct Imaging vs. Conventional Exposure
07/01/2025 | Simon Khesin -- Column: Driving InnovationMy first camera used Kodak film. I even experimented with developing photos in the bathroom, though I usually dropped the film off at a Kodak center and received the prints two weeks later, only to discover that some images were out of focus or poorly framed. Today, every smartphone contains a high-quality camera capable of producing stunning images instantly.
Hands-On Demos Now Available for Apollo Seiko’s EF and AF Selective Soldering Lines
06/30/2025 | Apollo SeikoApollo Seiko, a leading innovator in soldering technology, is excited to spotlight its expanded lineup of EF and AF Series Selective Soldering Systems, now available for live demonstrations in its newly dedicated demo room.
Indium Corporation Expert to Present on Automotive and Industrial Solder Bonding Solutions at Global Electronics Association Workshop
06/26/2025 | IndiumIndium Corporation Principal Engineer, Advanced Materials, Andy Mackie, Ph.D., MSc, will deliver a technical presentation on innovative solder bonding solutions for automotive and industrial applications at the Global Electronics A
Fresh PCB Concepts: Assembly Challenges with Micro Components and Standard Solder Mask Practices
06/26/2025 | Team NCAB -- Column: Fresh PCB ConceptsMicro components have redefined what is possible in PCB design. With package sizes like 01005 and 0201 becoming more common in high-density layouts, designers are now expected to pack more performance into smaller spaces than ever before. While these advancements support miniaturization and functionality, they introduce new assembly challenges, particularly with traditional solder mask and legend application processes.
Knocking Down the Bone Pile: Tin Whisker Mitigation in Aerospace Applications, Part 3
06/25/2025 | Nash Bell -- Column: Knocking Down the Bone PileTin whiskers are slender, hair-like metallic growths that can develop on the surface of tin-plated electronic components. Typically measuring a few micrometers in diameter and growing several millimeters in length, they form through an electrochemical process influenced by environmental factors such as temperature variations, mechanical or compressive stress, and the aging of solder alloys.