-
- News
- Books
Featured Books
- pcb007 Magazine
Latest Issues
Current IssueInventing the Future with SEL
Two years after launching its state-of-the-art PCB facility, SEL shares lessons in vision, execution, and innovation, plus insights from industry icons and technology leaders shaping the future of PCB fabrication.
Sales: From Pitch to PO
From the first cold call to finally receiving that first purchase order, the July PCB007 Magazine breaks down some critical parts of the sales stack. To up your sales game, read on!
The Hole Truth: Via Integrity in an HDI World
From the drilled hole to registration across multiple sequential lamination cycles, to the quality of your copper plating, via reliability in an HDI world is becoming an ever-greater challenge. This month we look at “The Hole Truth,” from creating the “perfect” via to how you can assure via quality and reliability, the first time, every time.
- Articles
- Columns
- Links
- Media kit
||| MENU - pcb007 Magazine
Estimated reading time: 4 minutes
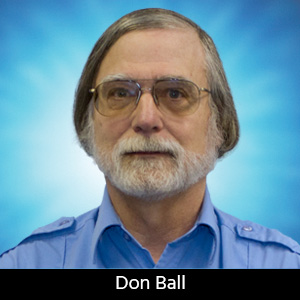
The Chemical Connection: How Industry 4.0 Shapes PCB Wet Processes
Earlier this year, I had the opportunity to attend IPC APEX EXPO 2022 where I was able to network with many great people in the electronics industry and see how other businesses are connected to the work we do at Chemcut. Although that might have been my main takeaway, there was another trend that I couldn’t ignore: the fourth generation of the industrial revolution is alive and well in the industry. After witnessing the many technologies that can be leveraged to boost automation, I couldn’t help but consider how they may impact the wet processing side of PCB manufacturing. I also wonder about other forms of automation we may soon see and what those developments could mean for the industry.
Material Handling
One of the main areas where we see an impact is material handling. The newest development is the implementation of robotics alongside PCB equipment to load or unload material into/from processing machines (Figure 1). PCB manufacturers have long-awaited this technology due to its many benefits.
Certainly, with the introduction of robotics to wet processing equipment, a boost in production rate is to be expected, but there are other benefits. With a loader like the one shown in Figure 1, panels are also less likely to become damaged. Although loading a panel into a machine may sound like a simple task, it is highly susceptible to error. If the person loading the panel is not careful enough, the corners and edges of the panel can easily be damaged. Even if the operator only slightly damages the edges of the panel, it could result in a much larger problem down the line. The initial damage can become exaggerated and effectively ruin the product even more. It could even cause the panel to create a jam inside the machine and halt production.
It should also be noted that this problem becomes an even greater concern as you try to obtain thinner PCB layers. Since the thin materials are more easily damaged, they often need to be handled with extra care. For some PCB manufacturers, the layers being manufactured are so thin that people loading the material must be specially trained on how to handle panels without causing damage. By introducing robotics into this section of the PCB manufacturing process, so many variables are removed, thus keeping production consistent in a simple and effortless process—even for ultra-thin materials.
Smart Connections
Another development in automation is the ability to operate them from our smart devices. Loaders like the one shown in Figure 1 can be conveniently operated from a laptop or any touch screen device. Smart connections are not limited just to loading robotics either. Recently, we have started to see implementations of smart device interaction with your wet processing equipment, effectively allowing you to make process changes anywhere.
Having this new freedom to effectively run your entire process from a smart device creates some new opportunities. Without requiring someone to continuously monitor and operate the machine now, these workers can then shift their focus to specialized tasks such as checking etchant conditions, calibrating probes, or performing maintenance checks. This will grant PCB manufacturers more time and resources to take care of matters that are important yet often overlooked. For instance, the person who would typically load panels all day could implement a cohesive preventive maintenance program like I discussed in my previous column, “The Case for Preventive Maintenance.” Reallocating time and resources to matters like this would be a great way to keep your PCB manufacturing process moving at a steady pace with a reduced number of sudden complications.
Where It All Comes Together
With this further push for automation, there will be plenty more extraordinary developments ahead. Now that robotics and smart devices are becoming more integrated into PCB processing equipment, I think the future certainly holds promise in making these seamlessly interconnected. I think it is likely that this technology will become fully integrated with wet processing equipment. Perhaps it may even get to the point where processing lines can become autonomous. To achieve this, however, there seems to be one more area that will need further development: where data science meets wet processing.
If you look at the technology available today, you can see that the infrastructure for creating autonomous wet process lines is nearly complete. Let’s look at the technology we have at our disposal in wet processing equipment:
- Robotics: To take care of loading and material handling typically required by manual labor
- Smart connections: To control your equipment or receive updates anytime and anywhere
- Real time data logging: To observe the dynamics of each system in relation to the final product (data collected from equipment controls and quality checks)
To obtain an autonomous process, it seems that all these items just need to be brought together to form one united system that follows the PCB from start to finish. The only thing left to do is to utilize data logging to provide feedback into the system, perhaps with the smart connects as a universal controller. From there, it is possible that some form of machine learning could be implemented to dynamically interact with the system and make necessary process changes or decisions without requiring someone’s input. With autonomous wet processing lines, we would certainly see major growth in the PCB industry as they became more accessible. If technology continues its current trend, we may see this become a reality sooner than we would expect.
This column originally appeared in the May 2022 issue of PCB007 Magazine.
More Columns from The Chemical Connection
The Chemical Connection: Sales Organization from a Capital Equipment PerspectiveThe Chemical Connection: Through-glass Vias in Glass Substrates
The Chemical Connection: Reducing Defects in Circuit Board Production
The Chemical Connection: Common Misconceptions in Wet Processing
The Chemical Connection: Surface Finishes for PCBs
The Chemical Connection: Earthquakes, Astronauts, and Aquatics—A Lighter Look at the Past
The Chemical Connection: Better Fabs Attract a Better Workforce
The Chemical Connection: Can Changing Spray Nozzles Improve My Etch Quality?