-
-
News
News Highlights
- Books
Featured Books
- pcb007 Magazine
Latest Issues
Current IssueThe Hole Truth: Via Integrity in an HDI World
From the drilled hole to registration across multiple sequential lamination cycles, to the quality of your copper plating, via reliability in an HDI world is becoming an ever-greater challenge. This month we look at “The Hole Truth,” from creating the “perfect” via to how you can assure via quality and reliability, the first time, every time.
In Pursuit of Perfection: Defect Reduction
For bare PCB board fabrication, defect reduction is a critical aspect of a company's bottom line profitability. In this issue, we examine how imaging, etching, and plating processes can provide information and insight into reducing defects and increasing yields.
Voices of the Industry
We take the pulse of the PCB industry by sharing insights from leading fabricators and suppliers in this month's issue. We've gathered their thoughts on the new U.S. administration, spending, the war in Ukraine, and their most pressing needs. It’s an eye-opening and enlightening look behind the curtain.
- Articles
- Columns
- Links
- Media kit
||| MENU - pcb007 Magazine
Chemcut’s Robotic Solution
May 24, 2022 | I-Connect007 Editorial TeamEstimated reading time: 3 minutes
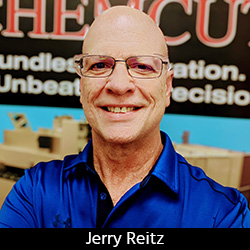
The I-Connect007 Editorial Staff spoke with Chemcut’s Jerry Reitz, and Atlantic Microtool’s Bruce Siemering and Neil Robinson about recent robotic automation advances, a specific robotic solution from Automata, and the changing factors tipping toward robotic automation in the current market.
Nolan Johnson: While robotics in the PCB fab area have been on the cusp for quite some time, it seems they haven’t taken off. Chemcut has been working with Atlantic Microtool and Automata on a possible solution. What motivated you to partner on robotic handlers now?
Jerry Reitz: By no means is this a large, industrialized robot. We believe that it is a fit for most of our customer’s applications, from small shops with smaller budgets and limited space to large facilities looking for a plug and play solution for large volume production.
Andy Shaughnessy: Who’s the manufacturer?
Bruce Siemering: The robot arm is manufactured for Chemcut by a robotics company out of the United Kingdom. Atlantic Microtool, which is owned by me and Neil Robinson made the initial contact and introduction to Chemcut.
We wanted to solve this problem where somebody is running a conveyorized line, and they’re loading a metal panel or a circuit board every 30 seconds, and they’re just standing there, or they’re running around to the other side to unload. It’s a mundane job that would be a perfect fit for this robot.
As we were looking for a robot, we noticed the ones we found were a little more difficult to program because the software was intimidating. One of the attractive features of this robotic handler we offer is that the software works on top of Python, which is a common software that runs automation.
It’s very easy to use and it’s not intimidating. When we first sent a robot to Chemcut one of their engineers, Dan Dietz, had it up and running in an hour or two. You can pull it out of the box, follow the instructions, and program it pretty rapidly to pick something up and move it to a conveyor. There’s not a very complex tool path with it.
Neil Robinson: When we’ve done demonstrations in the field, we show up at a customer site and within 45 minutes, we are actively loading product onto any conveyorized line. Not only is the setup simple, but it’s very simple to operate. Anybody who works in a manufacturing facility could be taught to program this robot within a couple of hours, unlike other industrial robots that have equally sophisticated software that require certain expertise to program. As Bruce pointed out, the software used to program this robot is a very user-friendly shell that sits on top of Python. Through graphics on the screen, two buttons that reside on the robot, and a mouse, you can create pretty sophisticated programs to load and unload equipment. The robot also has several digital inputs and outputs for sending and receiving commands from other equipment and devices.
Johnson: Is the handler so specialized that it only works well in a board fab application, or can it be used for other purposes?
Robinson: This robot wasn’t originally designed for the chemical milling or PCB industries. Actually, most of the early applications were in laboratory automation. We’ve taken that robot and adapted it to chemical milling and the printed circuit board industries with the use of specialized suction grippers. The robot can also be equipped with other tooling to handle many different applications, but primarily we are focused on the conveyorized equipment that Chemcut offers.
Johnson: With such an easy setup and operation, are your customers buying into the idea?
Robinson: Yes, overall, there are 300 to 400 units in the field with the first chemical milling installation in the United Kingdom. That unit has been in operation for a couple of years and the robot is holding up very well to that chemical environment.
To read this entire conversation, which appeared in the May 2022 issue of PCB007 Magazine, click here.
Suggested Items
Nolan’s Notes: Moving Forward With Confidence
06/03/2025 | Nolan Johnson -- Column: Nolan's NotesWe’re currently enjoying a revitalized and dynamic EMS provider market with significant growth potential. Since December 2024, the book-to-bill has been extremely strong and growing. Starting with a ratio of 1.24 in December, book-to-bill has continued to accelerate to a 1.41 in April. Yet, there is a global economic restructuring taking place. To say that the back-and-forth with tariffs and trade deals makes for an uncertain market is an understatement. While we may be in a 90-day tariff pause among leading economic nations, the deadline is quickly approaching and that leaves many of you feeling unsettled about what to expect.
Mycronic High Flex Changes Division Name to PCB Assembly Solutions
05/20/2025 | MycronicMycronic AB, the leading Sweden-based electronics assembly solutions provider, announced that its division formerly known as High Flex will now operate under the name PCB Assembly Solutions.
SolderKing Achieves the Prestigious King’s Award for Enterprise in International Trade
05/06/2025 | SolderKingSolderKing Assembly Materials Ltd, a leading British manufacturer of high-performance soldering materials and consumables, has been honoured with a King’s Award for Enterprise, one of the UK’s most respected business honours.
Foxconn's Tiger Leap Combining Nature and Technology in Ecological Roof Garden
04/23/2025 | FoxconnHon Hai Technology Group, the world's largest technology manufacturing and service provider, has actively responded to the United Nations Sustainable Development Goals (SDGs).
IDTechEx Highlights Recyclable Materials for PCBs
04/10/2025 | IDTechExConventional printed circuit board (PCB) manufacturing is wasteful, harmful to the environment and energy intensive. This can be mitigated by the implementation of new recyclable materials and technologies, which have the potential to revolutionize electronics manufacturing.