-
- News
- Books
Featured Books
- smt007 Magazine
Latest Issues
Current IssueIntelligent Test and Inspection
Are you ready to explore the cutting-edge advancements shaping the electronics manufacturing industry? The May 2025 issue of SMT007 Magazine is packed with insights, innovations, and expert perspectives that you won’t want to miss.
Do You Have X-ray Vision?
Has X-ray’s time finally come in electronics manufacturing? Join us in this issue of SMT007 Magazine, where we answer this question and others to bring more efficiency to your bottom line.
IPC APEX EXPO 2025: A Preview
It’s that time again. If you’re going to Anaheim for IPC APEX EXPO 2025, we’ll see you there. In the meantime, consider this issue of SMT007 Magazine to be your golden ticket to planning the show.
- Articles
- Columns
Search Console
- Links
- Media kit
||| MENU - smt007 Magazine
How Will Emerging Chiplet Technology Affect PCBs?
June 1, 2022 | I-Connect007 Editorial TeamEstimated reading time: 7 minutes
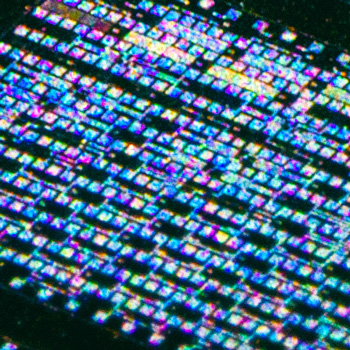
In a recent conversation with Ventec’s Alun Morgan, the I-Connect007 Editorial Team discussed, among several topics, semiconductor packaging developments. Industry insiders will know that, when you get Happy Holden and Alun Morgan talking about emerging technology trends, there will be insights shared.
Happy Holden: I’ve spent several hours this week learning more about the semiconductor industry’s expansion in chiplets which will provide a 30% higher yield from each wafer. To that industry, it’s an enormous increase in productivity.
There’s also talk about the planning or construction of 25 wafer fabs around the world. When those start coming online in three to five years, there will be an enormous scarcity of printed circuit packaging, a fact they’re just beginning to acknowledge.
Intel is investing $100 million in Ohio, and TSMC's expansion is $150 billion. We need to acknowledge there will likely be a coming shortage of materials. We need to hear ideas for conservation of materials because there’s absolutely no reason that a printed circuit board needs to be 62 mils thick, 1.6 millimeter; that stems from 50 years ago. If we took out two or three of those layers or made those layers thinner, then that prepreg could be used to make more boards. Next, if you go to high density, you can take about two to four of the signal layers out, and two to four of the reference layers for those signal layers for the same functioning PC board, just by going down to high density.
If you’re going down to high density and HDI, you can utilize the new generation of resin-coded copper, which means you don’t need prepreg at all. If you go to additive, you don’t need foil at all. There are all kinds of changes in paradigm that allow you to extend the materials you can get to make more finished printed circuit boards, but they must be thinner, denser, and/or smaller in order to fill those orders. You can’t do it the way we did it 40 years ago, which is what everybody likes to do because that’s what designers know. But the conservation of material says, “You either switch or you don’t ship. You get a choice here.”
Since the semiconductor guys will get the chips out there, electric vehicles will explode in terms of the number of boards they will consume. Unfortunately, those kinds of boards must be higher reliability; they don’t necessarily need exotic materials, but they need to be quality. You design those to be 0.8 millimeters or something like that, instead of 1.6 millimeters, then your material goes twice as far. If you choose those to be additive, then you’re less dependent on expensive copper foils. If you put in etchant regeneration, then you could make your own copper, like they did at GreenSource, and put it back into the plating tank because you etch more copper than you plate. Overall, there are a number of areas where we can provide ideas of conservation of materials in the short term and design paradigms in the long term.
Alun Morgan: It’s very topical, Happy. What we’re saying is you should get more from less. Is that not the message we’re all doing now in our environmental footprints? It’s the correct message. Absolutely. It’s also one I’ve been promoting for many decades. The reason we’ve got an 0.62 millimeter because of the edge connectors is because that’s the connectors that they designed 50 years ago. That’s the only reason. There’s no reason at all why it should be 0.62. It could be half that, a third of that. No reason at all.
Holden: Most people never think about that. It’s just always been that way. That’s the way the spec says, but if you made it one-third less thick, you could make three times as many boards with the same materials.
Morgan: Absolutely. We had these kinds of discussions, by the way, in 2000 on copper foil, for example. If you try and buy two-ounce, three-ounce, or four-ounce copper right now, you can’t get any. Why is that? It’s because they’d rather be turning out a half-ounce copper; they get more out of the drum because it runs quicker. The first lesson is not to design on two-, three-, or four-ounce copper, if you can help it. Try to design on thinner materials.
Holden: One of the outcomes is we will see an electronics boom; we’re not going to go into a recession. Maybe everybody else will, but electronics—if they have the chips—will expand. The chip guys are re-examining the way they lay out their wafers. This chiplet is a key element that will expand the application of ICs. It’s going to make it easier to design ICs. Their big problem is the interposed printed circuit board.
Barry Matties: Will that come to fruition, Happy? Are they changing their manufacturing processes now?
Holden: Yes. Intel, AMD, and TSMC are saying this is no longer a theory. Here, the actual number of improvements in the yield of wafers was staggering. Another semiconductor company, looking at those slides said, “Wow, that’s a big bang for the buck because the fixed costs are the same.” Their big problem is we need standards. Intel’s method of chiplets is not the same as AMD’s method of chiplets, which is not the same as TSMC’s method. You can’t have everybody inventing their own chiplet. They’re really focusing on having standards so that we can intermix these. This will really open the market, especially for the electric vehicle people that will design their boards.
Because guess what? There are 1,400 new electric vehicle companies around the world. We talk about the big three in Germany and in the U.S., but suddenly everybody wants to make an electric vehicle. Obviously, there will be some consolidation because I’m guessing most don’t know what the hell they’re doing. It’s not like a mobile phone; you can’t throw it away after two years. You have to design a vehicle that lasts for 15 to 20 years. Vehicles are not disposable like mobile phones because, interesting enough, the mobile phone industry is slowing down. Everybody has their mobile phone now and prices are going up. The features don’t necessarily require that you turn in your mobile phone after a year or two, even though everybody does.
Matties: It really sounds like the core message across all of this is reduced waste at all levels of your business.
Morgan: Well, the thing with the chiplets is very interesting. I have discussed that before and it’s innovation that industry can do. Silicon is different to the other parts of the business. First, to some extent, it’s less mature. It can put in these kinds of innovations. With that kind of change, I wish we could do something like that in the materials industry. I wish we could suddenly find a way to get 30% more productivity. The only way of doing it is if the designers will allow fewer layers as Happy was saying. We could probably double the amount of material available if they just take half the thickness, for example.
That’s a choice that they could make. They haven’t made it and possibly should. It’s about making more from less. Are you familiar with the film, “The Day the Earth Stood Still?” There’s a wonderful quote in that film saying that nobody changes until they’re at the precipice of dying or destruction. When you’re at the point where there’s nothing else you can do, then you change, you evolve. You don’t change beforehand. I think we might be in a position where people are forced to make these kinds of big changes, Happy.
They said that they’re entirely practical. They could have done this 10, 20 years ago—reduce the thickness, even taking a single layer out means you get an eighth more material. You take two layers out, you get a third more. It’s not rocket science to do that, but they may be forced to do so at some stage. I hope that some good may come out of all this, because it makes no sense for the environment and for waste, to carry on producing these really thick circuit boards when there’s no need anymore. They’re just not necessary.
Alun Morgan is technology ambassador at Ventec International Group.
Suggested Items
RF PCB Design Tips and Tricks
05/08/2025 | Cherie Litson, EPTAC MIT CID/CID+There are many great books, videos, and information online about designing PCBs for RF circuits. A few of my favorite RF sources are Hans Rosenberg, Stephen Chavez, and Rick Hartley, but there are many more. These PCB design engineers have a very good perspective on what it takes to take an RF design from schematic concept to PCB layout.
Trouble in Your Tank: Causes of Plating Voids, Pre-electroless Copper
05/09/2025 | Michael Carano -- Column: Trouble in Your TankIn the business of printed circuit fabrication, yield-reducing and costly defects can easily catch even the most seasoned engineers and production personnel off guard. In this month’s column, I’ll investigate copper plating voids with their genesis in the pre-plating process steps.
Elephantech: For a Greener Tomorrow
04/16/2025 | Marcy LaRont, PCB007 MagazineNobuhiko Okamoto is the global sales and marketing manager for Elephantech Inc., a Japanese startup with a vision to make electronics more sustainable. The company is developing a metal inkjet technology that can print directly on the substrate and then give it a copper thickness by plating. In this interview, he discusses this novel technology's environmental advantages, as well as its potential benefits for the PCB manufacturing and semiconductor packaging segments.
Trouble in Your Tank: Organic Addition Agents in Electrolytic Copper Plating
04/15/2025 | Michael Carano -- Column: Trouble in Your TankThere are numerous factors at play in the science of electroplating or, as most often called, electrolytic plating. One critical element is the use of organic addition agents and their role in copper plating. The function and use of these chemical compounds will be explored in more detail.
IDTechEx Highlights Recyclable Materials for PCBs
04/10/2025 | IDTechExConventional printed circuit board (PCB) manufacturing is wasteful, harmful to the environment and energy intensive. This can be mitigated by the implementation of new recyclable materials and technologies, which have the potential to revolutionize electronics manufacturing.