-
-
News
News Highlights
- Books
Featured Books
- pcb007 Magazine
Latest Issues
Current IssueThe Hole Truth: Via Integrity in an HDI World
From the drilled hole to registration across multiple sequential lamination cycles, to the quality of your copper plating, via reliability in an HDI world is becoming an ever-greater challenge. This month we look at “The Hole Truth,” from creating the “perfect” via to how you can assure via quality and reliability, the first time, every time.
In Pursuit of Perfection: Defect Reduction
For bare PCB board fabrication, defect reduction is a critical aspect of a company's bottom line profitability. In this issue, we examine how imaging, etching, and plating processes can provide information and insight into reducing defects and increasing yields.
Voices of the Industry
We take the pulse of the PCB industry by sharing insights from leading fabricators and suppliers in this month's issue. We've gathered their thoughts on the new U.S. administration, spending, the war in Ukraine, and their most pressing needs. It’s an eye-opening and enlightening look behind the curtain.
- Articles
- Columns
- Links
- Media kit
||| MENU - pcb007 Magazine
Breaking Down the Current Materials Market
June 8, 2022 | Nolan Johnson, I-Connect007Estimated reading time: 5 minutes
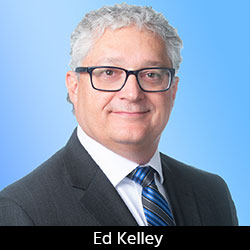
Nolan Johnson meets with Isola’s Ed Kelley at DesignCon and takes a tour of the dynamics in play in the materials market. As Isola prepares to roll out an extremely low-loss, halogen-free product, Kelley says the company continues to work on how to make the product reproducible and available to customers around the world.
Nolan Johnson: What’s front of mind for you and Isola in the materials market?
Ed Kelley: There are so many areas I could cover, but I’ll start with 5G as something critical. It’s been talked about for a long time, and even with the 5G rollout, there’s still more to do. If you break 5G down into low-, mid-, and high-band, most of the rollout has been low- and mid-band. But the high-band applications get interesting for base material suppliers and others in the supply chain because, where there are very high operating frequencies, people are looking for extremely low loss materials. Every piece of the base material is critical—the resin system, reinforcement, and the copper foil. There’s a lot to consider.
We do a lot of work developing extremely low loss resin systems because a lot goes into them, not just polymers, but fillers and flame retardants as well. Low Dk fiberglass cloth has become common as a reinforcement. The next-generation low-Dk glasses are more available now than a year ago, though still not at full commercial scale, and we’re looking at alternative types of reinforcements to achieve certain characteristics. Much of the loss at higher frequencies is due to conductor loss, creating a need for copper foils with lower and lower surface profiles.
How do you ensure those low-profile coppers stick to your dielectric material and give you a reliable printed circuit board? It’s one thing to achieve an electrical performance target by itself. It’s not as easy to get the electrical performance and satisfy everything else the material has to do. In addition to meeting signal integrity requirements, the material also needs to meet thermal reliability and CAF resistance requirements in complex, high-layer-count boards. We also focus on PCB manufacturability. We want our products to be as easy to use in PCB manufacturing as possible so that our customers can achieve high yields. So we spend a lot of time up front developing resin systems and integrating them with glass and copper options to meet all these requirements.
Back to electrical performance, we also have to consider how materials are used by the PCB fabricator. It’s important to recognize the nuances of keeping the system as low loss as possible. When the fabricator takes our material, makes an innerlayer circuit, and runs it through oxide-alternative chemistries, that’s another area of attention for 5G signal integrity performance. If you roughen up the copper surface too much, you degrade the loss performance. We’re all working as hard as possible to make sure the end product achieves the goals of the OEMs.
Johnson: That’s a lot to balance those constraints. You’re already working iteratively on known solutions, so how do we develop materials that help open a more reliable high-speed 5G application?
Kelley: We’re about to release a new product called TerraGreen 400G. As the name implies, it’s extremely low loss and halogen-free. We’ve got our UL certification. We’re focused not just on the performance of the material itself, but whether we can manufacture it repeatably day in, day out. As the product grows, is the supply chain stable enough to support demand growth? We are wrapping up some of the final qualification testing, not just to meet internal requirements, but with suppliers; we want to make sure we have a robust supply of the materials that go into it. Our goal with the product, with the combination of resin, glass, and copper, is 25% lower loss than our best performing high-speed digital product currently, which is Tachyon 100G.
With the combination of resin, glass and copper, we’re hitting those signal integrity targets with this product. We’ve done the thermal reliability testing. The CAF resistance we’re seeing is excellent. In fact, with these very smooth copper foils for high frequency applications, we’ve seen cases of copper migration at the bond line between an etched laminate surface and the prepreg that’s bonded to it.
Traditionally with CAF, people think of migration along the resin-to-glass interface, which is the most common failure. With some of these very low-profile copper foils, the copper suppliers are determining how to get a better chemical bond vs. mechanical bond between the copper and dielectric. There are various adhesion promoters that can be used, but some may not be compatible with all the resin systems that companies like us are trying to develop.
If you use the wrong adhesion promoter, when you etch off the copper it may still be on the surface and interfere with the bond of the prepreg to the etched laminate. We’ve spent considerable time making sure we understand what’s driving that and what we need for the right adhesion promoter for our resin system. As we wrap up that work, we are seeing some very good results.
Even as we introduce this new product, we’re looking at what comes next. Our chemists are looking to synthesize some of our own polymers, which would still be used in combination with commercially available resins, but may offer us some unique attributes in our applications.
As we develop resin systems, we recognize there is a range of operating frequencies to consider, and you don’t always need the lowest loss material. When you don’t, you don’t want to pay for the loss performance you don’t need. We are offering a halogen-free resin system which is extremely low loss, but we could put it on E-glass, low Dk glass, next-generation low Dk glass, and different copper combinations. With that one resin system, we can target certain loss properties and combinations that are attractive, both for performance and cost. You don’t always need to use the most costly option.
To read this entire conversation, which appeared in the May 2022 issue of PCB007 Magazine, click here.
Suggested Items
The Evolution of Picosecond Laser Drilling
06/19/2025 | Marcy LaRont, PCB007 MagazineIs it hard to imagine a single laser pulse reduced not only from nanoseconds to picoseconds in its pulse duration, but even to femtoseconds? Well, buckle up because it seems we are there. In this interview, Dr. Stefan Rung, technical director of laser machines at Schmoll Maschinen GmbH, traces the technology trajectory of the laser drill from the CO2 laser to cutting-edge picosecond and hybrid laser drilling systems, highlighting the benefits and limitations of each method, and demonstrating how laser innovations are shaping the future of PCB fabrication.
Day 2: More Cutting-edge Insights at the EIPC Summer Conference
06/18/2025 | Pete Starkey, I-Connect007The European Institute for the PCB Community (EIPC) summer conference took place this year in Edinburgh, Scotland, June 3-4. This is the third of three articles on the conference. The other two cover Day 1’s sessions and the opening keynote speech. Below is a recap of the second day’s sessions.
Day 1: Cutting Edge Insights at the EIPC Summer Conference
06/17/2025 | Pete Starkey, I-Connect007The European Institute for the PCB Community (EIPC) Summer Conference took place this year in Edinburgh, Scotland, June 3-4. This is the second of three articles on the conference. The other two cover the keynote speeches and Day 2 of the technical conference. Below is a recap of the first day’s sessions.
Preventing Surface Prep Defects and Ensuring Reliability
06/10/2025 | Marcy LaRont, PCB007 MagazineIn printed circuit board (PCB) fabrication, surface preparation is a critical process that ensures strong adhesion, reliable plating, and long-term product performance. Without proper surface treatment, manufacturers may encounter defects such as delamination, poor solder mask adhesion, and plating failures. This article examines key surface preparation techniques, common defects resulting from improper processes, and real-world case studies that illustrate best practices.
RF PCB Design Tips and Tricks
05/08/2025 | Cherie Litson, EPTAC MIT CID/CID+There are many great books, videos, and information online about designing PCBs for RF circuits. A few of my favorite RF sources are Hans Rosenberg, Stephen Chavez, and Rick Hartley, but there are many more. These PCB design engineers have a very good perspective on what it takes to take an RF design from schematic concept to PCB layout.