Rogers Corporation to Present & Exhibit at 2022 IMS in Denver, Colorado
June 14, 2022 | Rogers CorporationEstimated reading time: 2 minutes
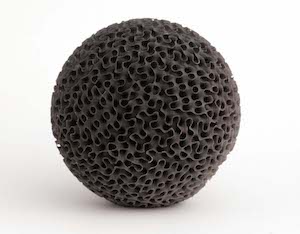
Rogers Corporation has announced that Technical Marketing Manager John Coonrod will give three presentations on June 21 in the MicroApps Theater at the International Microwave Symposium (IMS) in Denver. His topics will include “Radix 3D Printable Dielectrics & Lens Demonstrator,” “An Overview of Copper Foil: How It's Made, Roughness Effects & RF/ HSD Influences,” and “How to Get Consistent Millimeter-Wave Performance Using Grounded Coplanar Waveguide.”
In addition, Rogers will be showcasing its most recently released products in Booth #2030 during IMS, the world’s largest RF and Microwave show, which takes place from Tuesday, June 21 to Thursday, June 23. These products include Radix™ 3D Printable Dielectrics and RO4835IND™ LoPro® Laminates.
Radix™ 3D Printable Dielectric, is the first 3D material featuring a dielectric constant of 2.8 and low loss characteristics at microwave frequencies. These printable dielectric materials give radio frequency (RF) designers unprecedented design freedom in creating new components, eliminating the need to consider typical manufacturing design constraints.
Rogers Corporation’s Radix3D Printable Dielectric is a proprietary composite material designed for Digital Light Processing (DLP) 3D printing, enabling a scalable, high-resolution printing process for end-use RF dielectric component manufacturing. This printable dielectric material has a targeted dielectric constant of 2.8 and a dissipation factor of 0.0043 at 10 GHz when cured.
The new material is intended for use as RF material in applications where new geometric freedom can enhance the figure of merits of an RF system, such as gradient dielectric constant (GRIN) structures and other complex three-dimensional parts. The Radix 3D Printable Dielectric offers the industry a way to manufacture systems and components at scale that could not be made with traditional fabrication methods. Radix materials are available directly from Rogers Corporation and our 3D printing partners.
RO4835IND LoPro thermoset laminates are specially designed for 60-81 GHz short-range industrial radar applications, where excellent electrical performance and cost-efficiency are equally important. These laminates also provide environmental reliability and interconnection stability, which are critical criteria for PCB material selection.
With a low insertion loss of 2.13dB/inch at 60 GHz, these laminates meet customers’ critical radar coverage requirements. The expanded weave fiber provides excellent Dk uniformity, and Rogers’ tight quality control provides low Dk variation from lot to lot. RO4835IND LoPro laminates are compatible with standard epoxy/glass (FR-4) processes and have a higher fabrication yield rate compared to conventional PTFE-based laminates. Low material and fabrication costs make RO4835IND LoPro laminates a cost-effective solution for industrial radar.
To learn more about Radix 3D Printable Dielectrics, visit Rogers' youtube channel, https://www.youtube.com/c/RogersCorpACS
About Rogers Corporation
Rogers Corporation (NYSE:ROG) is a global leader in engineered materials to power, protect and connect our world. Rogers delivers innovative solutions to help our customers solve their toughest material challenges. Rogers’ advanced electronic and elastomeric materials are used in applications for EV/HEV, automotive safety and radar systems, mobile devices, renewable energy, wireless infrastructure, energy-efficient motor drives, industrial equipment and more. Headquartered in Chandler, Arizona, Rogers operates manufacturing facilities in the United States, Asia and Europe, with sales offices worldwide.
Testimonial
"The I-Connect007 team is outstanding—kind, responsive, and a true marketing partner. Their design team created fresh, eye-catching ads, and their editorial support polished our content to let our brand shine. Thank you all! "
Sweeney Ng - CEE PCBSuggested Items
The Government Circuit: Navigating New Trade Headwinds and New Partnerships
08/25/2025 | Chris Mitchell -- Column: The Government CircuitAs global trade winds continue to howl, the electronics manufacturing industry finds itself at a critical juncture. After months of warnings, the U.S. Government has implemented a broad array of tariff increases, with fresh duties hitting copper-based products, semiconductors, and imports from many nations. On the positive side, tentative trade agreements with Europe, China, Japan, and other nations are providing at least some clarity and counterbalance.
How Good Design Enables Sustainable PCBs
08/21/2025 | Gerry Partida, Summit InterconnectSustainability has become a key focus for PCB companies seeking to reduce waste, conserve energy, and optimize resources. While many discussions on sustainability center around materials or energy-efficient processes, PCB design is an often overlooked factor that lies at the heart of manufacturing. Good design practices, especially those based on established IPC standards, play a central role in enabling sustainable PCB production. By ensuring designs are manufacturable and reliable, engineers can significantly reduce the environmental impact of their products.
50% Copper Tariffs, 100% Chip Uncertainty, and a Truce
08/19/2025 | Andy Shaughnessy, I-Connect007If you’re like me, tariffs were not on your radar screen until a few months ago, but now political rhetoric has turned to presidential action. Tariffs are front-page news with major developments coming directly from the Oval Office. These are not typical times. President Donald Trump campaigned on tariff reform, and he’s now busy revamping America’s tariff policy.
Global PCB Connections: Understanding the General Fabrication Process—A Designer’s Hidden Advantage
08/14/2025 | Markus Voeltz -- Column: Global PCB ConnectionsDesigners don’t need to become fabricators, but understanding the basics of PCB fabrication can save you time, money, and frustration. The more you understand what’s happening on the shop floor, the better you’ll be able to prevent downstream issues. As you move into more advanced designs like HDI, flex circuits, stacked vias, and embedded components, this foundational knowledge becomes even more critical. Remember: the fabricator is your partner.
MKS’ Atotech to Participate in IPCA Electronics Expo 2025
08/11/2025 | AtotechMKS Inc., a global provider of enabling technologies that transform our world, announced that its strategic brands ESI® (laser systems) and Atotech® (process chemicals, equipment, software, and services) will showcase their latest range of leading manufacturing solutions for printed circuit board (PCB) and package substrate manufacturing at the upcoming 17th IPCA Show to be held at Pragati Maidan, New Delhi from August 21-23, 2025.