-
- News
- Books
Featured Books
- pcb007 Magazine
Latest Issues
Current IssueInventing the Future with SEL
Two years after launching its state-of-the-art PCB facility, SEL shares lessons in vision, execution, and innovation, plus insights from industry icons and technology leaders shaping the future of PCB fabrication.
Sales: From Pitch to PO
From the first cold call to finally receiving that first purchase order, the July PCB007 Magazine breaks down some critical parts of the sales stack. To up your sales game, read on!
The Hole Truth: Via Integrity in an HDI World
From the drilled hole to registration across multiple sequential lamination cycles, to the quality of your copper plating, via reliability in an HDI world is becoming an ever-greater challenge. This month we look at “The Hole Truth,” from creating the “perfect” via to how you can assure via quality and reliability, the first time, every time.
- Articles
- Columns
- Links
- Media kit
||| MENU - pcb007 Magazine
Estimated reading time: 6 minutes
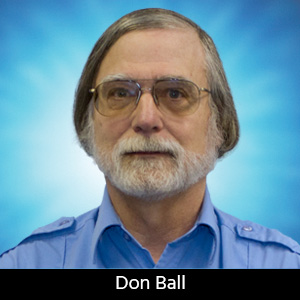
The Chemical Connection: Etchants of the Industry—Cupric vs. Alkaline
Chemical etching is a vital process for manufacturing PCBs. It is one of the most complex chemical processes next to plating. This is because there are many different variables that can affect your product and how efficiently it is produced. Although it is complex, etching of copper can be narrowed down to a handful of etchants that PCB manufacturers widely use. By far, the most common etchants are cupric chloride and alkaline cupric chloride, commonly referred to as “ammoniacal alkaline etchant.” There are other etchants for copper, such as ferric chloride, sodium persulfate, and alkaline ammonia sulfate, but they are not commonly used for PCB manufacturing and are often only used in “special cases.” I may touch on those other etchants a bit more in a future column, but this one will focus on cupric and alkaline.
About Cupric and Alkaline
Together, these etchants are used in the majority of PCB etch shops, with alkaline being the most popular. To provide a baseline of how they work, their etch reactions along with their corresponding regeneration reactions, can be found in Table 1.
One of the main reasons these two etchants are the most used is because of their regeneration capabilities. With regeneration, you increase the capacity of copper you can etch. It also helps keep the etch rate at a consistent value. To maintain mass production of PCBs, it is important to keep the etch rate steady but also high enough to maximize output. Since etch rate can greatly influence production rates, it is a major factor when comparing etchants.
Etch Rate
Between the two etchants, alkaline etchant dominates in etch rate. Alkaline normally has an etch rate of 2–2.5 mils/min, whereas cupric chloride typically has an etch rate of 1–1.6 mils/min.1, 2 This is one of the reasons why alkaline is favored more than cupric chloride. Since etching usually takes a large portion of time in the making of a PCB, having this reduction in etch time can nearly double your production. For you to get the same production level with cupric chloride, you would need to invest in a longer etch section of your processing line, which would mean increasing the number of sequential etch chambers.
Regeneration
As seen in Table 1, both etchants can undergo a regeneration reaction to restore the etchant’s quality. Although they both have the capability, cupric chloride has an upper hand because the regeneration reaction is simple. Regeneration for cupric etchant, in most cases, involves simply feeding your reagents into the etcher.
For alkaline etchant, it is more complicated because the regeneration reaction is dependent on oxygen, which it gets from air flowing through the machine. This can be tricky because you need an optimal flow of air through your machine. For alkaline etchants, it is important to have a sustainable amount of ammonia in your solution (see “chemistry control” below). If air flow through the etching machine is excessive, there will be a rapid loss of ammonia. On the other hand, if you do not have a high enough airflow, your etch rate will drop faster as you etch more panels. There is another form of regeneration for alkaline etchant that is done through liquid-liquid extraction.3 It is an efficient way to regenerate alkaline etchant, but it is not common. This is because of the additional capital cost and the required know-how to make it work properly. Often it is considered easier to send the used alkaline etchant to a company that will regenerate it, with liquid-liquid extraction, for resale.
Etch Factor
Another matter where alkaline etchant is highly favored is etch factor, the ratio of downward etch to sideways etch. Alkaline etchant offers the benefit of a 4-to-1 etch factor (meaning it etches downward four times as much as it etches sideways). Cupric provides a standard 3-to-1 etch factor (Figure 1).
Alkaline etchant’s better etch factor opens the opportunity to maintain finer spaces and line widths when you are etching panels with thicker copper layers. Although alkaline can provide a great etch factor, a 4-to-1 ratio can only be obtained if the etchant is kept at its optimal condition, which is easier said than done.
Chemistry Control
Although alkaline etchant has some qualities that can prove to be great for PCB production, it is a challenging etchant to maintain. There are many extra precautions that need to be taken with alkaline etchant that wouldn’t be necessary for etching chemistries like cupric or ferric chloride. This is because the chemistry is based on ammonia, a very volatile gas. Once the ammonia content in solution drops too much, there is an irreversible precipitation reaction, known as “sludge-out,” that renders your etchant unusable. To avoid this, you must ensure that the etchant is constantly in use and not allowed to sit idly for more than two days. While it is in use, you must maintain a strong handle on your etchant’s conditions. The parameters alkaline needs to be within are often narrow and not so easily controlled.
Cupric chloride provides a stark contrast to this because it is quite easy to handle. It is perhaps the most forgiving of all metal etchants because the parameters you need to keep a consistent etch rate have a relatively large window. If there is some deviation from the parameters, your etch quality will not change much. Additionally, unlike alkaline etchant, intermittent use is allowable; therefore, if you are not etching panels on a daily basis, this is a suitable etchant for your process.
Resist Compatibility
Resist compatibility is important in any chemical etch process. This is because if your resist and etchant are incompatible, the resist will lift or disintegrate off the surface during etching, thus preventing you from obtaining your desired features. Between alkaline and cupric, resist compatibility varies greatly. One matter that is a deal breaker for some PCB fabricators is that cupric chloride is incompatible with most metallic resists. For this reason, cupric chloride etching is often dedicated to the manufacturing of inner layer PCBs. Alkaline is on the opposite end of the spectrum because it can be used with most metallic resists, but it has a drawback of being incompatible with many alkali strippable photoresists (dry film). Since these etchants cover two completely different ends of this spectrum, most PCB manufacturers will adopt both etchants into their etch shop so they can make both inner and outer layers.
Summary
Each etchant clearly has their own strengths and weaknesses. Table 2 shows a side-by-side comparison of the differences between the two etchants.
From Table 2, it can be concluded that cupric chloride may be the better etchant to go with if you are given the choice. With its simplicity in chemistry and required maintenance, it makes up for any of its shortcomings. Using alkaline etchant does not seem necessary unless you are a PCB manufacturer who is running production every day, needs tight lines and spaces on your PCBs, and/or needs to use metallic resists. If that does not describe you as a PCB manufacturer and yet you still desire to use alkaline, it is recommended that you get a chemist or process engineer experienced in maintaining the alkaline etch chemistry.
References
- “Process Guidelines for Alkaline Etching,” Chemcut.net, October 2001.
- “Process Guidelines for Cupric Chloride Etching,” Chemcut.net.
- “Happy’s Tech Talk: Regeneration of Copper,” by Happy Holden, PCB007 Magazine, May 2022.
This column originally appeared in the June 2022 issue of PCB007 Magazine.
More Columns from The Chemical Connection
The Chemical Connection: Sales Organization from a Capital Equipment PerspectiveThe Chemical Connection: Through-glass Vias in Glass Substrates
The Chemical Connection: Reducing Defects in Circuit Board Production
The Chemical Connection: Common Misconceptions in Wet Processing
The Chemical Connection: Surface Finishes for PCBs
The Chemical Connection: Earthquakes, Astronauts, and Aquatics—A Lighter Look at the Past
The Chemical Connection: Better Fabs Attract a Better Workforce
The Chemical Connection: Can Changing Spray Nozzles Improve My Etch Quality?