-
- News
- Books
Featured Books
- pcb007 Magazine
Latest Issues
Current IssueSales: From Pitch to PO
From the first cold call to finally receiving that first purchase order, the July PCB007 Magazine breaks down some critical parts of the sales stack. To up your sales game, read on!
The Hole Truth: Via Integrity in an HDI World
From the drilled hole to registration across multiple sequential lamination cycles, to the quality of your copper plating, via reliability in an HDI world is becoming an ever-greater challenge. This month we look at “The Hole Truth,” from creating the “perfect” via to how you can assure via quality and reliability, the first time, every time.
In Pursuit of Perfection: Defect Reduction
For bare PCB board fabrication, defect reduction is a critical aspect of a company's bottom line profitability. In this issue, we examine how imaging, etching, and plating processes can provide information and insight into reducing defects and increasing yields.
- Articles
- Columns
- Links
- Media kit
||| MENU - pcb007 Magazine
Estimated reading time: 3 minutes
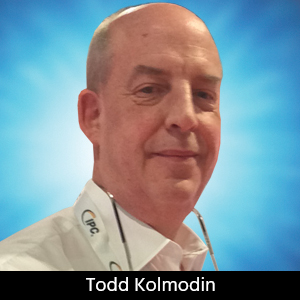
Testing Todd: ET and the DoD
Building printed circuits can be a tricky business. There are many attributes that go into the production process. Initially, there is the sales interface with the customer, the receipt of the data for the initial quotation. Then there is the procurement process for raw materials, which must be done to the customer specifications. It could be the base materials, plating, mask, or screen, and that is just for the physical build part of the process. They may have special requirements for acceptance, dimensional tolerances, hole tolerances, and the like. That is all just the customer documentation. They may stipulate the industry standard(s) that are to be used for the general manufacturing process—IPC 6012, 6013, etc., and the electrical acceptance standards, for instance, IPC 9252. Now, if that isn’t enough, throw in Department of Defense (DoD) or aerospace specifications.
This month let’s dive into the DoD and how this affects electrical test (ET). The current build specification for the Department of Defense for rigid product is MIL-PRF-31032. However, we still see specification calls for MIL-PRF-55110 and MIL-PRF-50884 (flex). We periodically see IPC-ET-652 called out, but new builds should use IPC-9252.
For the ET arena, the call to the older specifications, 55110 and 50884, are not usually an issue if the revision level is specified. It isn’t safe to assume “latest rev” when you see this called out. The Defense Logistics Agency (DLA) requires these specifics to be called out for traceability. So, make sure when these specifications are called (55110 and 50884) that the appropriate revision and amendment (if applicable) are specified. The reason for this is that older revisions did not allow certain types of test methodology available today to be used as they were not available when the older revision was created. For example, the use of indirect test by signature comparison, sometimes stated as discharge test on a flying probe, was not allowed in earlier revisions of the specifications. It has only been in recent years that this practice is allowed and only in certain revisions of the specifications.
Now, when talking about MIL-PRF-31032 and electrical test, it’s a new ballgame. Just stating, “Test to MIL-PRF-31032,” will not work. You see, with MIL-PRF-31032, you also have the build supplements, usually referred to as “slash sheets.” There are slash sheets one to eight. They specifically address the type of product manufactured and requirements above the standard 31032 specification. If that isn’t enough, the slash sheets all have a revision level and likely an amendment. So, when your customers request builds compliant to MIL-PRF-31032 you need to push for the slash sheet, revision, and amendment to be used. As of June 2022, the specification sheet is MIL-PRF-31032/1D with Amendment 3.
If this is documented on the production traveler or document, it will remove all confusion at the time of electrical test. This document contains all relevant information as to what test methodologies are allowed and what documentation is required for traceability. If the “slash,” revision, and amendment are not given, there is a chance that the product could be tested outside the requirements the customer intended.
Working with the DLA over the years, this is one of the most common audit nonconformances I’ve found regarding electrical test service centers and in-house ET departments. These specifics need to be on the Certificate of Compliance (CoC) for all military products.
If you receive product calling out MIL-PRF-31032 that does not specify the specific revision, slash sheet/revision, and amendment, the appropriate action is to stop and query your customer or sales team to gather this information before proceeding. Failure to do so may result in an audit nonconformance and incorrect traceability of the product tested.
We all know it is taxing enough to go through these periodic audits so having these ducks in a row will stop an almost sure nonconformance and corrective action. Plus, it will make the electrical test department or service center confident they are providing the service(s) the customer intended.
This column originally appeared in the June 2022 issue of PCB007 Magazine.
More Columns from Testing Todd
Testing Todd: Why 4-wire Kelvin?Testing Todd: Why TDR?
Testing Todd: Positivity Boosts Employee Morale
Testing Todd: Preparing Employees for the Long Haul
Testing Todd: Where Can We Improve?
Testing Todd: Turning Into the Wind
Testing Todd: Coming Back to Life—Design Recovery
Testing Todd: Decision Time—Invest or Delegate?