Estimated reading time: 6 minutes
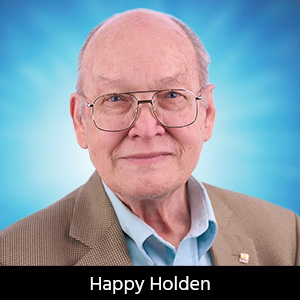
Contact Columnist Form
Happy’s Tech Talk #10: Optical Alignment/Coupon Welding for Stackups
In this month’s column, I will discuss optical alignment for pinless lamination stackup, a topic that complements the induction lamination in my November 2021 column. Examples of this type of equipment are seen in Figure 1.
Pin tooling plates have been used for lamination since it first started sometime in the 1960s. I first encountered multilayer stackup when I was assigned to increase capacity for our multilayer output in 1972. This was to accommodate the growth of our computer business. Unfortunately, the explosive growth of our calculator orders in 1973 required that we look for numerous vendors to produce the six-layer logic board in the HP-35 calculator.
Hewlett-Packard evolved from using four small holes in our pin lamination to using a four-slot center-line pin with post-etch punch in 1974. Registration experiments on this transition were highlighted by a DOE in Chapter 3, Figure 4 of my book, 24 Essential Skills for Engineers1.
Pin Lamination
Although many schemes have been used, the most popular is the four-pin center-line slot approach. Here a high-precision tooling template with mechanical pins is used for the lay-up and registration. The inner layers must first be prepared with the corresponding registration holes. These holes are generally drilled or punched post etch. The prepreg must also have holes for the pins. These holes do not have to be precise, and they can be 1 or 2 mm larger than those of the inner layers. Stainless steel shims and release film are employed between groups of stackups (called books). For the conventional vacuum-heated hydraulic multilayer press, numerous tolerances lead to misregistration of the various inner layers. Figure 2 illustrates six such tolerances from an excellent paper by Anthony Faraci.2
Pinless Stacking
Around 1999, Faraci, who had been working with multilayer tooling for nearly 15 years, started working on optical alignment. He needed a method to hold layers together, so he looked at eyelets (rivets), hot heads, ultrasonic, and induction. After months of development, he settled on induction and came up with a scheme to “weld” the many inner layers together rather than use the common rivets or plate pins. This has evolved to where welds can be located to interior spots on the I/L core. The pinless systems, with innerlayer welding are also available for traditional pin layup.
Process of Operation
The process of using optical alignment is similar to manual layup, only more accurate and faster, with checks to ensure material order and orientation. The process is shown below:
- Place the lower lamination plate in position on the layup table and begin layup as usual up to the first separator plate.
- After placing the first separator plate in location, place the untooled copper foil (this foil will be outside layer n).
- Next place the untooled prepreg (this is all the prepreg between layers n-2 and n-1).
- Place the prepreg along the two perpendicular laser layup lines (Figure 3).
- Continue placing material up to layer (core) 1 and 2 then activate the welding head.
- Place the welded package along the two perpendicular laser lines. The welded package consists of layers 2 to n-1 with all the associated prepreg welded in place between all the layers.
- Place the untooled prepreg (this is all the prepreg between layers 1 and 2).
- Place the untooled copper foil (this foil will be layer 1).
- Place the next separator plate and repeat the process for the entire book.
The inner layers must first be prepared with the corresponding fiducial targets on top and bottom side for the optical alignment (Figure 3). The prepreg has no need for any hole/punch. The inner layers must have weld coupons etched in the reserve zones on both top and bottom sides (Figure 3), and can be placed anywhere along the edges of the lamination plate or inside the image area.
The use of fiducial targets etched in the layers to align through image processing via CCD cameras is the critical alignment step. This process results in lower manufacturing and maintenance cost due to the elimination of the pins, bushings, and tooled separator plates on the lamination process.
In today’s best fit on pin lamination technology guarantees around 75 µm for layer-to-layer registration, while optical registration measures each layer to get the front to back image registration as well the geometry shape of each core and can align inner layers with a tolerance of ±15 µm (using direct digital imaging). This is possible because each core is individually inspected and can be rejected as quality control according to a tolerance specification. This new generation of the induction bonders provides a capability to place multiple numbers of bonding points in any location of the multilayer stack for best registration.
Those bonding spots work as virtual pins to help the scale constrain, similar to multiple tooling pins around a single PCB. The bonding points can be placed anywhere in the CAD design, the machine is capable to read and decode the CAD file jobs, and automatically know the coordinates for each bonding location of the panel.
Four bonding heads with independent movement in X and Y axes allow the movement of each head to any location and provide fast speed for complex panels that require many bonding locations for best registration and multilayer handling. With cores being as thin as 25-50 µm, and sub-laminations common, the welding process can accommodate these variations as well as coppers from one-third to three ounces. Optionally, the registered and bonded multilayer panel could be automatically unloaded at a rear unloading station that could be equipped with a trolley. Also, one plastic protection sheet can be automatically inserted between each panel. The welded coupon bonding process is seen in Figure 4. The welded book can withstand the dilations and shrinkage of the hot press cycles, thereby providing the best possible linear movement of all layers in a multilayer stackup, reducing the internal stress that causes warping and deformations, and moreover reducing the distortions and misalignments between inner layers.
The welded stackup multilayer can be X-rayed to check before and after lamination for compensation adjustments.
Technical Requirements
The key component to this imaginative process is the induction welding heads. Figure 5 shows three different designs for such induction heating systems. The ability to change the energy and pressure on the coupons is important as materials and constructions change. As multilayers of rigid, flex, and rigid-flex change and become more complex, these welding heads also will probably change.
Weld Coupons
The weld coupons on the perimeter of the inner layer cores replace the old punched or drilled holes. The coupons are varied, but in the range of six to 10 mm wide by 15 to 40 mm long copper and recommended copper clearance. All have solid copper decals as seen in Figure 6.
Each equipment supplier has much more detail available from the many years they have been supplying systems.
Conclusion
As Figure 7 illustrates (a complex 32-layer multilayer), the optical alignment process with the welding of all the cores together improves the registration in multilayer lamination. Coupled with the time savings for layup and the cleanup of epoxy around pin plates, pinless lamination can be a great productivity and quality improvement. This is shown by the more than 250 systems being sold since 2000. The optical and pin alignment systems with their induction core welding have also been adapted for flex and rigid-flex layups. The advantages of pinless:
- Increased layer-to-layer registration accuracy
- Increased process predictability and registration data
- Ability to characterize lamination press process
- Ability to register thin cores accurately and consistently
- Flexibility utilizing lamination plates
- Plates do not need tooling holes; this allows the plates to be used for multiple panel sizes, and thus fewer sets of lamination plates are needed
- Separator plates also do not need tooling holes; this allows the plates to be used for multiple panel sizes, thus fewer sets of separator plates are needed
- Cleaner operation; cleaning plates are easier to clean; there are no resin filled tooling holes
- Copper foil does not need clearances for tooling pins, as foil is easily damaged when trying to lay up on pins
- Prepreg does not need clearances for tooling pins which minimizes prepreg dust
- There will be more flexibility in panel sizes without the restrictions of the pins
- The lamination pins and bushings are eliminated, thus eliminating a consumable
- Depinning is not necessary
References
- 24 Essential Skills for Engineers, by Happy Holden.
- “Optical layer-to-layer Alignment,” by Anthony Faraci, The PCB Magazine, June 2012, pp.40-47.
This column originally appeared in the July 2022 issue of PCB007 Magazine.
More Columns from Happy’s Tech Talk
Happy’s Tech Talk #37: New Ultra HDI MaterialsHappy’s Tech Talk #36: The LEGO Principle of Optical Assembly
Happy’s Tech Talk #35: Yields March to Design Rules
Happy’s Tech Talk #34: Producibility and Other Pseudo-metrics
Happy’s Tech Talk #33: Wet Process Management and Control
Happy’s Tech Talk #32: Three Simple Ways to Manage and Control Wet Processes
Happy’s Tech Talk #31: Novel Ultra HDI Architectures
Happy’s Tech Talk #30: The Analog Computer