-
- News
- Books
Featured Books
- pcb007 Magazine
Latest Issues
Current IssueInventing the Future with SEL
Two years after launching its state-of-the-art PCB facility, SEL shares lessons in vision, execution, and innovation, plus insights from industry icons and technology leaders shaping the future of PCB fabrication.
Sales: From Pitch to PO
From the first cold call to finally receiving that first purchase order, the July PCB007 Magazine breaks down some critical parts of the sales stack. To up your sales game, read on!
The Hole Truth: Via Integrity in an HDI World
From the drilled hole to registration across multiple sequential lamination cycles, to the quality of your copper plating, via reliability in an HDI world is becoming an ever-greater challenge. This month we look at “The Hole Truth,” from creating the “perfect” via to how you can assure via quality and reliability, the first time, every time.
- Articles
- Columns
- Links
- Media kit
||| MENU - pcb007 Magazine
Estimated reading time: 5 minutes
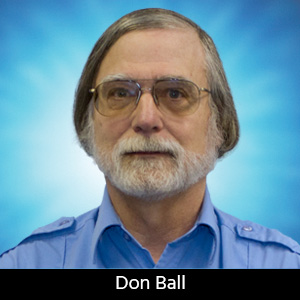
The Chemical Connection: Don't Sludge-Out—A Guide for Alkaline Etching
In my last column,” Etchants of the Industry: Cupric vs. Alkaline,” I compared cupric chloride and alkaline cupric chloride. In that column, I mentioned that alkaline etchant is the most used etchant for PCB fabrication. It is used because it provides a high etch rate, improved etch factor, and compatibility with metallic resists. Although it has some great benefits, it has the drawback of being difficult to control. The etching chemistry requires a delicate balance, and the parameters it needs to stay within are relatively tight. Not only are the margins for error small but falling outside these parameters may have consequences. If you are not careful enough, you could hit the point of “sludge-out”—a point where your etchant will undergo an irreversible precipitation reaction. Sludge-out can dramatically reduce the effectiveness of your etchant, and it can cause severe damage to your products and etching equipment. To prevent sludge-out from happening to you, here is a short guide to understanding the chemistry control for alkaline etchant.
Table 1: Etch and regeneration reactions for alkaline cupric chloride.
Understand the Chemistry
Utilizing alkaline etchant requires a thorough understanding of the chemistry taking place inside the etching machine. Inside the etch chamber, two reactions are the focus: the etch reaction and the regeneration reaction. Those reactions are shown in Table 1. How the reactants are incorporated into the reactions are shown in Figure 1.
From the table, the first reaction is the simple etch reaction where the etchant (Cu+2(NH3)4Cl2) reacts with copper (Cu0) to provide the spent form of alkaline etchant (Cu+1(NH3)2Cl). The etch reaction is relatively simple, unlike the regeneration reaction. The regeneration reaction tends to be the primary cause for concern because it is complex yet essential to your process. The regeneration reaction is important because it allows you to etch your panels and not see a decline in PCB quality or production rate. In the regeneration reaction, the spent form of the etchant reacts with ammonia (NH3), ammonium chloride (NH4Cl), and oxygen (O2) to convert the etchant back to its original form. Water (H2O) is a by-product of this reaction. All the reaction components (ammonia, ammonium chloride, oxygen, and water) play a vital role in maintaining the etchant. Ammonia plays a critical role in pH control, ammonium chloride contributes to chloride content, oxygen acts as the limiting reagent in regeneration, and water helps with specific gravity control (copper concentration control). These components to the reaction help you stay within the parameters alkaline etchant needs to function. The main factors you will need to watch out for are pH, chloride levels, and air flow. These should be the focus of your efforts because these tend to be the most high-risk or difficult things to control.
pH Control
Holding a steady pH value in alkaline etchant is the biggest challenge. One of the main reasons it is difficult to manage is because pH is not a value that is easily measured. Alkaline etchant can easily damage pH probes and cause inaccurate readings. Since pH dropping can cause sludge-out, having inaccurate pH readings cannot be acceptable. To monitor pH, it is recommended to use pH probes along with routine titrations. The pH should be kept within the range of 8.1-8.2 (may vary slightly depending on chemical supplier).1 If you start to notice the formation of dark blue crystals in your etchant, that is also a sign that your pH is too low.
Another reason pH is difficult to control is because it can fall out of range easily. This is because pH is maintained with ammonia gas, and sufficient pH levels rely on having ammonia dissolved in the etchant. With ammonia being highly volatile, keeping it dissolved in your etchant can be difficult. There are many variables that can affect how ammonia remains in the etchant. Temperature, spray pressure, and ventilation are the main parameters that affect whether ammonia escapes or stays in the etchant.
Even if you are not using the etchant at a given time, you still need to worry about maintaining pH. If alkaline etchant is allowed to sit for a long time in an unsealed environment, the ammonia will bleed out of the etchant, drop the pH, and sludge-out will occur. To prevent this, it is best to pump it out of the etching machine and place it in drums if you don’t plan to use it within three days. By placing the etchant in drums, you are sealing it and preventing the ammonia from escaping.
Chloride Control
It is also necessary to sustain chloride levels to prevent sludge-out. Like pH control, it is a good practice to perform routine titrations to check chloride levels. Thankfully, maintaining your chloride level is easier than maintaining pH. This is because the only way to lose your chloride content is by dilution or insufficient input to keep up with the regeneration reaction. The most common cause of chloride loss involves people utilizing only ammonia instead of the typical ammonia-ammonium chloride blend in the "replenish rinse" section. Using only ammonia effectively dilutes the chloride content and causes the concentration to fall out of the desired range. Chloride content should remain within the range of 160-165 g/L. If your chloride levels drop too much, that will result in the formation of light-blue crystals. To bring chloride levels back up, you can simply dissolve ammonium chloride crystals into your etchant.
Optimized Air Flow
To have a steady etch process, it is important to maintain the regeneration reaction. Maintaining a steady regeneration reaction relies on having a sufficient supply of the limiting reagent, oxygen, to keep up with production. Since oxygen must be pulled into the etch chamber through the ventilation system, some additional challenges come into play. This is because the air flow needs to be optimized. With too little air flow, you may not have enough oxygen to sustain your etch rate. Too much air flow will cause your ammonia to leave the etchant and cause the pH to drop—potentially leading to sludge-out.
In cases of large-scale PCB production, sometimes ventilation is not enough. In these cases, additional air sparging in the etcher sump is needed. Air sparging is a method to feed oxygen into an etchant by bubbling compressed air through the bottom of the etch bath. It has some of the same challenges as the normal ventilation approach. Too much sparging can drive excessive ammonia out of the etchant, but too little may not be sufficient to keep production steady. Finding the optimal air flow can be a trial-and-error process, but with a careful watch on pH and etch quality, you can find the optimal amount.
Conclusion
Chemistry control for alkaline etchant has always been a challenge. Most of that difficulty comes from not having the proper understanding of how alkaline etchant works, and what it needs to stay stable. Now that we have covered the main troublesome areas, you are better equipped to maintain and get the most out of your alkaline etchant.
References
1. “Process Guidelines for Alkaline Etching,” Chemcut.net, October 2001.
This column originally appeared in the July 2022 issue of PCB007 Magazine.
More Columns from The Chemical Connection
The Chemical Connection: Experience and Wisdom Gained by Doing BusinessThe Chemical Connection: Sales Organization from a Capital Equipment Perspective
The Chemical Connection: Through-glass Vias in Glass Substrates
The Chemical Connection: Reducing Defects in Circuit Board Production
The Chemical Connection: Common Misconceptions in Wet Processing
The Chemical Connection: Surface Finishes for PCBs
The Chemical Connection: Earthquakes, Astronauts, and Aquatics—A Lighter Look at the Past
The Chemical Connection: Better Fabs Attract a Better Workforce