-
- News
- Books
Featured Books
- pcb007 Magazine
Latest Issues
Current IssueSales: From Pitch to PO
From the first cold call to finally receiving that first purchase order, the July PCB007 Magazine breaks down some critical parts of the sales stack. To up your sales game, read on!
The Hole Truth: Via Integrity in an HDI World
From the drilled hole to registration across multiple sequential lamination cycles, to the quality of your copper plating, via reliability in an HDI world is becoming an ever-greater challenge. This month we look at “The Hole Truth,” from creating the “perfect” via to how you can assure via quality and reliability, the first time, every time.
In Pursuit of Perfection: Defect Reduction
For bare PCB board fabrication, defect reduction is a critical aspect of a company's bottom line profitability. In this issue, we examine how imaging, etching, and plating processes can provide information and insight into reducing defects and increasing yields.
- Articles
- Columns
- Links
- Media kit
||| MENU - pcb007 Magazine
Estimated reading time: 6 minutes
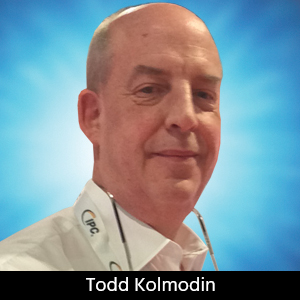
Testing Todd: Breaking the Void
Electrical test is best known for identifying routine opens and shorts. But what has plagued ET, and manufacturers in general, is the barrel void. These voids are breaks in the plating of the drilled barrel that result in circuitry “opens” that pass through the stackup from one layer to another. In some cases, the break in plating is severe and results in an immediate open condition that is detected during electrical test.
However, certain plating anomalies can be present that will go undetected during standard ET. What we must remember is that electricity must follow Ohm’s Law no matter what conditions exist. That is: V = I x R, where V = Voltage, I = Current, and R = Resistance.
The most significant hidden plating anomaly to barrels is thin copper, sometimes known as “taper plate” as shown in Figures 1 and 2. This is a condition where copper may be acceptable close to the outer layers of the PCB but may become thinner as distance increases to the center of the depth of the barrel. Although copper exists, it is a dangerous anomaly that can routinely go undetected. Now I can hear the gallery saying, “Todd, how is this possible? The thin copper should blow like a fuse under the formula of Ohm’s Law.” Well, if Ohm’s Law were to be applied straight away, you would likely be correct, along with most circuitry in the board. The reason? Most small trace widths could not stand up to the abuse.
ET vs. Ohm’s Law
This law cannot be broken. However, we can adapt to the law while still maintaining safety to the PCB and underlying circuitry. Many specifications call for test voltages to be applied during test. Industry and military requirements are 40V minimum, so let’s use that. Calculators ready? Okay, we see 40V. Let’s say the continuity resistance threshold is 20 ohms. Now plug those into Ohm’s Law: 20V = I x 20. Ohm’s Law can be simplified for solving any variable. For instance, V/R = I or V/I = R. Anyway, we have 40 volts and 20 ohms. Solving, V/R = I we see 40/20 = I, or 2 amps. Not many 3- to 5-mil traces are going to survive that let alone the electronics in the test machine.
Now, what many may not understand about ET and how machines check for opens and shorts is that the “test voltage” requirement is not applied to the opens, or continuity test. The simple fact is that, as shown above, the excessive current would be devastating. Two different processes are in place during the opens test. First, the voltage is limited to a low value, typically 12–20V regardless of the test voltage requirement. This is simply because an open will be present at 10 volts, or the low voltage, thus the high voltage is not required. The second is that during the continuity test the machines use bypass circuitry to limit the current that is applied to the circuit under test. Parallel resistive networks in the machine will shunt the current away from the circuit, allowing only enough to safely take the continuity measurements. Pretty sneaky, huh? Indeed.
The higher voltages are applied during the shorts or discontinuity test. Once circuits are validated for opens, the higher voltage is applied to circuits to identify shorts. Again, Ohm’s Law is at play. However, with testing for shorts, we don’t just apply the voltage and hope for the best. In this case, we know the voltage applied but the other variables are unknown. As we are testing network-to-network for possible shorts, the resistance value is expected to be very high to infinite. Using V = I x R, V is known, so in my example, I will use 100V. We don’t know I or current, but we do know the theoretical resistance R. However, we cannot use “0” or infinite as the law will not allow us. 100 = I x 0? It cannot work when we know we have a known voltage value of 100. So, the shorts threshold must have a value in resistance. Most times it is 10 meg ohms or higher. Now the law works again. 100 = I x 10M or 10,000,000 ohms. Solving, 100V/10M ohms = 0.00001 amps or 10 micro-amps. Now that is still way too much current to allow to pass between circuits if a short may exist. Current limit triggers are in place during the shorts test that effectively stop the test on the network when any current is detected between the nets. Therefore, it is relatively rare that a standard automatic electrical test can result in damage to the circuitry. In other words, don’t rely on ET to blow up shorts as, in general, we do not apply enough current to cause shorts to burn. The test can heat up the short momentarily before the fault trigger but usually will not cause the short to go away.
I digressed to theories, so let me come back to voids. Based on my long-winded explanation regarding how the opens and shorts tests work, we cannot lean on ET to detect all types of barrel voids. We limit current flow so that we are not blowing fuses (thin traces.) Furthermore, the difference in resistance of a network with an acceptable signature compared to a network with a taper plate or thin copper wall will not be that different. These changes in resistance are usually in the milli-ohms. Most electrical test machines use a threshold with a tolerance of plus or minus a percentage. For example, 20 ohms ±5%. That is like 1 ohm. A taper plate void scenario may only change the overall resistance of the network by 5–10 milli-ohm. This will not trigger a fault in the continuity test and thus go undetected.
William Thompson to the rescue. If you are familiar with 4-Wire Kelvin testing, you might know that Thompson invented this test in about 1861. This high-resolution measurement system is based on the Kelvin Bridge which Thompson (later known as Lord Kelvin) invented (Figure 3). Using this theory, high resolution measurements can be taken while eliminating the stray or parasitic resistance of the leads and electronics. 4-Wire Kelvin can detect finite differences in resistance in the milli- and micro-ohm ranges. This test will detect taper plate anomalies and poor bonding of micro-vias.
It is common to perform destructive analysis on plated barrels during the manufacturing process. These potted micro-sections can identify plating anomalies if they are a systemic or gross error to the entire order. Remember that these sections are a sample of just a few holes and a PCB may have many thousands of holes. Therefore, this is not always a good indicator of an isolated issue such as a low voltage flight bar in plating or a bad agitation cycle which results in an isolated set of suspect panels. This is where 4-Wire Kelvin can save time and money by detecting these types of issues. If 4-Wire Kelvin is integrated into your manufacturing theatre, a sampling of product with high aspect ratio drilled and plated holes is indicated. A random sample of panels from different flight bars should be tested to identify any possible anomalies. If an anomaly is found, that flight bar can be isolated and the panels fully tested under 4-Wire Kelvin guidelines to validate integrity. Conforming groups can be released for further processing. What this does is remove the threat of latent defects in the field due to poor barrel plating or bonding of the micro-vias. Although this might take some time in the manufacturing process, it far outweighs the cost of returned product and reputation damage with your customer base. Here, the cost of quality has a valuable argument against the cost of non-conforming product and loss of customers. This is especially true today when time to market is crucial and PCBs are increasingly more expensive to manufacture.
This column originally appeared in the August 2022 issue of PCB007 Magazine.
More Columns from Testing Todd
Testing Todd: Why 4-wire Kelvin?Testing Todd: Why TDR?
Testing Todd: Positivity Boosts Employee Morale
Testing Todd: Preparing Employees for the Long Haul
Testing Todd: Where Can We Improve?
Testing Todd: Turning Into the Wind
Testing Todd: Coming Back to Life—Design Recovery
Testing Todd: Decision Time—Invest or Delegate?