-
- News
- Books
Featured Books
- pcb007 Magazine
Latest Issues
Current IssueVoices of the Industry
We take the pulse of the PCB industry by sharing insights from leading fabricators and suppliers in this month's issue. We've gathered their thoughts on the new U.S. administration, spending, the war in Ukraine, and their most pressing needs. It’s an eye-opening and enlightening look behind the curtain.
The Essential Guide to Surface Finishes
We go back to basics this month with a recount of a little history, and look forward to addressing the many challenges that high density, high frequency, adhesion, SI, and corrosion concerns for harsh environments bring to the fore. We compare and contrast surface finishes by type and application, take a hard look at the many iterations of gold plating, and address palladium as a surface finish.
It's Show Time!
In this month’s issue of PCB007 Magazine we reimagine the possibilities featuring stories all about IPC APEX EXPO 2025—covering what to look forward to, and what you don’t want to miss.
- Articles
Article Highlights
- Columns
Search Console
- Links
- Media kit
||| MENU - pcb007 Magazine
Rogers Corporation to Highlight Materials for Millimeter Wave Designs at PCB West 2022
September 13, 2022 | Rogers CorporationEstimated reading time: 3 minutes
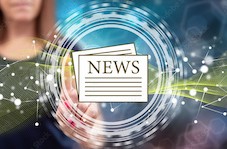
Rogers Corporation will exhibit at PCB West in Santa Clara, CA (booth #201) highlighting some of its high-performance circuit materials used in multilayer structures which include a family of thin laminates and bonding materials.
PCB West provides in-depth technical training and access to a host of leading suppliers to the printed circuit board design, fabrication, and assembly industry. Held at the Santa Clara Convention Center, the event takes place October 5th from 10:00 a.m. – 6:00 p.m.
Rogers Presentation
Rogers’ Technical Marketing Manager, John Coonrod, will present “Understanding High Frequency Materials Test Methods for Dk and Df” on Wednesday, October 5, from 10 to 11 a.m. Coonrod’s presentation will review the many different test methods which can be used to determine the dielectric constant (Dk) or dissipation factor (Df) for a high frequency circuit material. He will explain how it is possible to test the same circuit material, using two different test methods, get two different answers and both answers can be correct.
Rogers’ Materials at Booth 201:
SpeedWave® 300P Ultra-Low Loss Prepreg. With the increasing need for stackup flexibility in high layer count designs for 5G millimeter wave, high resolution 77 GHz automotive radar, aerospace & defense and high speed digital designs, SpeedWave 300P prepreg offers a broad range of competitively priced high performance options for the circuit designer. SpeedWave 300P prepreg can be used to bond a variety of Rogers’ materials including XtremeSpeed™ RO1200™, CLTE-MW™, and RO4000® series laminates.
This prepreg system offers a low dielectric constant of 3.0 – 3.3 and a low dissipation factor of 0.0019 – 0.0022 at 10 GHz with stable performance over a broad frequency range. This material is offered in multiple spread and open weave glass styles and resin content combinations to maximize stackup options.
RO3003G2™ 9 micron Laminates with Electrodeposited HVLP Foil
Thin copper foil can simplify the PCB fabrication steps required to consistently produce reliable millimeter wave radar PCBs. Utilizing 9 micron foils on antenna outer layers for millimeter wave radar PCBs can help PCB fabricators achieve tighter final feature tolerance for signal lines and antenna patterns. Additionally, starting with 9 micron copper on RO3003G2 laminate, instead of 18 micron copper, can reduce the copper reduction steps needed by the PCB fabricator to meet the final PCB copper thickness requirements after filled via formation.
RO4835IND™ LoPro® Laminates
RO4835IND LoPro thermoset laminates are specially designed for 60-81 GHz short-range industrial radar applications, where excellent electrical performance and cost-efficiency are equally important. These laminates also provide environmental reliability and interconnection stability, which are critical criteria for PCB material selection.
With a low insertion loss of 2.13dB/inch at 60 GHz, these laminates meet customers’ critical radar coverage requirements. The expanded weave fiber provides excellent Dk uniformity, and Rogers’ tight quality control provides low Dk variation from lot to lot. RO4835IND LoPro laminates are compatible with standard epoxy/glass (FR-4) processes and have a higher fabrication yield rate than conventional PTFE-based laminates. Low material and fabrication costs make RO4835IND LoPro laminates a cost-effective solution for industrial radar.
RO4000® Products for Multilayer Structures:
Next generation products designed to meet the existing and emerging needs of advanced millimeter wave multilayer designs. RO4835T™ laminates, offered in a 2.5 mil, 3 mil and 4 mil core thickness, are 3.3 Dk, low loss, spread glass reinforced, ceramic filled thermoset materials designed for inner-layer use in multilayer board designs, and they complement RO4835™ laminates when thinner cores are needed.
RO4450T™ 3.2-3.3 Dk, low loss, spread glass reinforced, ceramic filled bonding materials were designed to complement RO4835T laminates and the existing RO4000 laminate family, and come in 2.5, 3, 3.5, 4, 4.5, 5 or 6 mil thicknesses.
RO4835T laminates and RO4450T bonding materials exhibit excellent Dk control for repeatable electrical performance, a low z-axis expansion for plated through-hole reliability and are compatible with standard epoxy/glass (FR-4) processes. These materials are an excellent choice for multilayer designs requiring sequential laminations, as fully cured RO4000 products are capable of withstanding multiple lamination cycles. RO4835T laminates and RO4450T bondplys have the UL 94 V-0 flame retardant rating and are compatible with lead-free processes.
Suggested Items
Trouble in Your Tank: Organic Addition Agents in Electrolytic Copper Plating
04/15/2025 | Michael Carano -- Column: Trouble in Your TankThere are numerous factors at play in the science of electroplating or, as most often called, electrolytic plating. One critical element is the use of organic addition agents and their role in copper plating. The function and use of these chemical compounds will be explored in more detail.
IDTechEx Highlights Recyclable Materials for PCBs
04/10/2025 | IDTechExConventional printed circuit board (PCB) manufacturing is wasteful, harmful to the environment and energy intensive. This can be mitigated by the implementation of new recyclable materials and technologies, which have the potential to revolutionize electronics manufacturing.
Connect the Dots: Stop Killing Your Yield—The Hidden Cost of Design Oversights
04/03/2025 | Matt Stevenson -- Column: Connect the DotsI’ve been in this industry long enough to recognize red flags in PCB designs. When designers send over PCBs that look great on the computer screen but have hidden flaws, it can lead to manufacturing problems. I have seen this happen too often: manufacturing delays, yield losses, and designers asking, “Why didn’t anyone tell me sooner?” Here’s the thing: Minor design improvements can greatly impact manufacturing yield, and design oversights can lead to expensive bottlenecks. Here’s how to find the hidden flaws in a design and avoid disaster.
Real Time with... IPC APEX EXPO 2025: Tariffs and Supply Chains in U.S. Electronics Manufacturing
04/01/2025 | Real Time with...IPC APEX EXPOChris Mitchell, VP of Global Government Relations for IPC, discusses IPC's concerns about tariffs on copper and their impact on U.S. electronics manufacturing. He emphasizes the complexity of supply chains and the need for policymakers to understand their effects.
The Chemical Connection: Surface Finishes for PCBs
03/31/2025 | Don Ball -- Column: The Chemical ConnectionWriting about surface finishes brings a feeling of nostalgia. You see, one of my first jobs in the industry was providing technical support for surface cleaning processes and finishes to enhance dry film adhesion to copper surfaces. I’d like to take this opportunity to revisit the basics, indulge in my nostalgia, and perhaps provide some insight into why we do things the way we do them in the here and now.